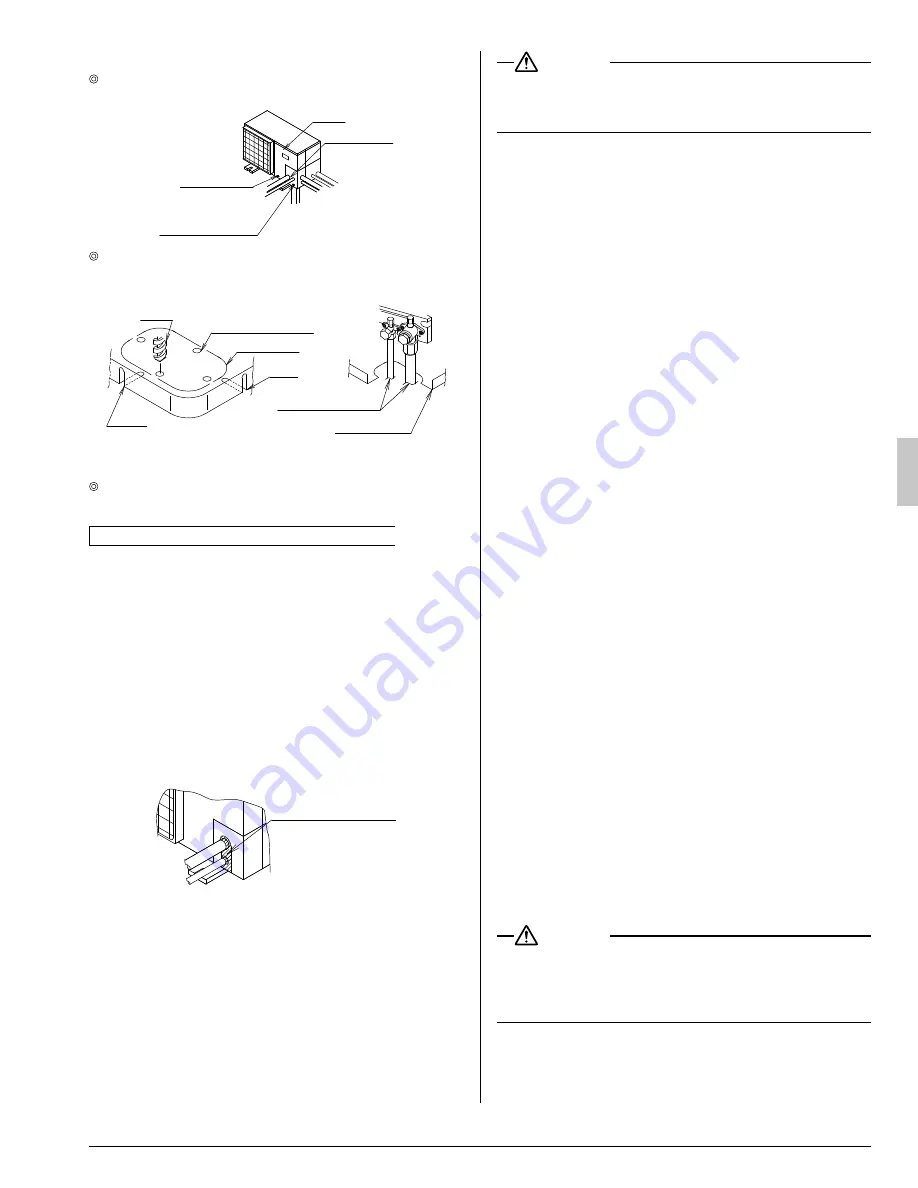
English
10
Refrigerant piping work procedure
6-4
The fi eld piping can be connected in three directions.
Piping cover
Screw for
front panel
Screw for piping
cover (front)
Front
panel
Lateral
direction
Front direction
Downward
direction
When connecting the pipings downward, remove the knock-
out by making four holes in the middle on the each side of
the knockout with a drill.
Field pipings
Bottom frame
Knockout
Drill
Slit
Middle on the side
Slit
Then cut out the corner of the bottom frame along the slits (in
two positions) by using a hacksaw.
After removing the parts, it is recommended to apply repair
paint on the edges, to prevent rusting.
Cautions on connecting the connection piping
When it is expected that water condensed in the stop valve
•
will reach the indoor unit through the gap between the heat
insulating material and the piping (for example, when the
outdoor unit is installed in a higher position than the indoor
unit), take proper action such as caulking the connection
area.
[Measures to prevent invasion of small creatures and litter]
Block all gaps in the piping penetration areas with putty or
•
heat insulating material (arranged in the local fi eld) as
shown in the fi gure below.
(If small creatures, such as insects, or litter, enters the
outdoor unit, a short-circuit may be caused inside the elec-
tric parts box.)
Putty or heat
insulating material
(arranged in local field)
Heat insulation of piping
6-5
Make sure to insulate the fi eld pipings (on both the liquid line
•
and gas line) and refrigerant branching kit.
(If they are not insulated, water leakage may be caused.)
(The maximum temperature of the piping on the gas line is
about 248 °F during heating operation. Use an insulation
suffi ciently resistant to this temperature.)
Reinforce the refrigerant piping according to the installation
•
environment. If it is not reinforced, condensate may form on
the surface of the insulation.
WARNING
Make sure to insulate the fi eld piping up to the piping con-
•
nection area inside the unit. If the piping is exposed, dew
condensation and burn by contact may be caused.
Airtight test and vacuum drying
6-6
The unit has been checked for leaks by the manufacturer.
Confi rm that the valves are fi rmly closed before airtight test or
vacuumdrying.
To prevent entry of any impurities and insure suffi cient pres-
sure resistance, always use the special tools dedicated for
R410A.
Perform the following inspections securely after the
piping work.
Airtight test
•
- Make sure to use nitrogen gas. (For the
service port position, refer to the fi gure in “
Stop valve
operation method
”.)
[Procedure] Pressurize the air conditioner from the liquid
pipe and gas pipe up to 450 psi (Make sure not to exceed
450 psi). When the pressure does not drop for 24 hours, the
piping work shall be accepted.
If the pressure drops, check for leakage positions. (Confi rm
that there is no leakage, then release nitrogen.)
Vacuum drying
•
- Use a vacuum pump which can evacuate
up to –14.6 psi or less.
[Procedure] Operate the vacuum pump for evacuation for
2 hours or more using both liquid pipe and gas pipe until the
vacuum pressure reaches –14.6 psi or less. Leave the air
conditioner at –14.6 psi or less for 1 hour or more, and
confi rm that the vacuum pressure indicated by the vacuum
gage does not increase.
(If the vacuum pressure increases, the system may contain
moisture or have leakage.)
If there is a possibility of moisture remaining in the piping
(for example, when there is a possibility of dew condensation
inside the piping because the piping work was performed in
the rainy season or over a long period of time, or when rainwa-
ter may have entered the piping during the work)
Perform evacuation described above for 2 hours (vacuum
drying), pressurize the air conditioner up to 7 psi (vacuum
break) with nitrogen gas, then evacuate the air conditioner
using the vacuum pump for 1 hour to achieve –14.6 psi or less
(vacuum drying).
(If the vacuum pressure does not reach –14.6 psi or less even
after evacuation for 2 hours or more, repeat vacuum break and
vacuum drying.) Leave the air conditioner in the vacuum status
for 1 hour or more, and confi rm that the vacuum pressuree
indicated by the vacuum gauge does not increase.
Additional refrigerant charge
6-7
WARNING
To avoid injury always use protective gloves and eye protec-
•
tion when charging refrigerant.
To avoid injury do not charge with unsuitable substances.
•
Use only the appropriate refrigerant.
01_EN_3PA60114-14U.indd 10
01_EN_3PA60114-14U.indd 10
2/24/2009 5:23:07 PM
2/24/2009 5:23:07 PM
Summary of Contents for SkyAir RZQ18PVJU
Page 19: ...3PA60114 14U EM08A096 0902 HT ...