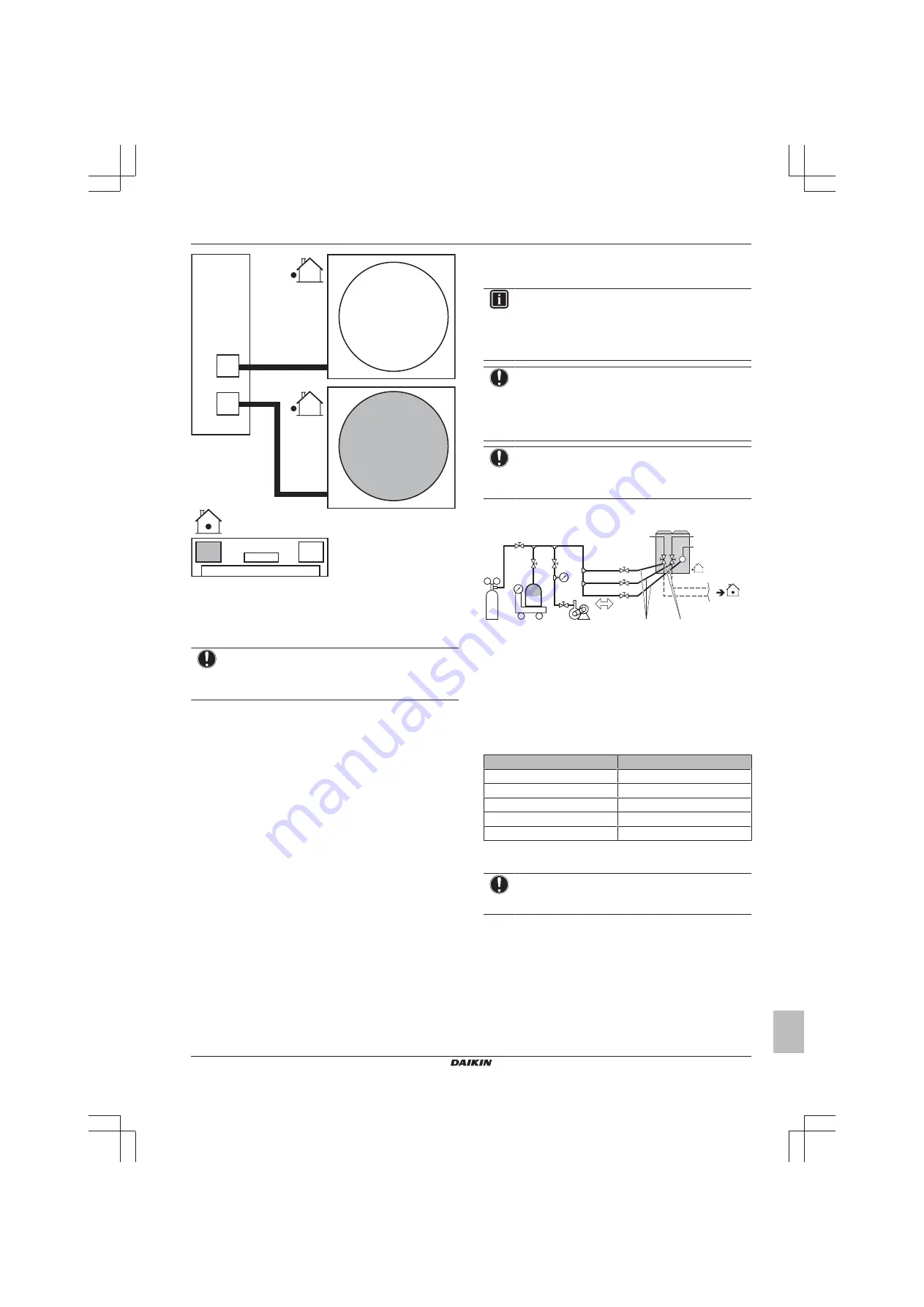
6 Installation
Installer and user reference guide
23
SERHQ020~0 SEHVX20~64BAW
Split packaged air-cooled water chiller
4P508020-1A – 2018.01
VRV
C1
VRV
C2
f
e
g
C2
g
C1
C1
C2
d
d
a
b
c
a
Indoor unit
b
Outdoor unit 1
c
Outdoor unit 2 (only in case of 64BAW)
d
Refrigerant piping
e
Pump
f
Switchbox
g
Evaporator
NOTICE
When installing the piping between the outdoor and indoor
units, also refer to the figure in
supply and transmission cables" on page 33
6.6
Checking the refrigerant piping
6.6.1
About checking the refrigerant piping
The outdoor unit's
internal
refrigerant piping has been factory tested
for leaks. You only have to check the outdoor unit's
external
refrigerant piping.
Before checking the refrigerant piping
Make sure the refrigerant piping is connected between the outdoor
unit and the indoor unit.
Typical workflow
Checking the refrigerant piping typically consists of the following
stages:
1
Checking for leaks in the refrigerant piping.
2
Performing vacuum drying to remove all moisture, air or
nitrogen from the refrigerant piping.
If there is a possibility of moisture being present in the refrigerant
piping (for example, water may have entered the piping), first carry
out the vacuum drying procedure below until all moisture has been
removed.
6.6.2
Precautions when checking the
refrigerant piping
INFORMATION
Also read the precautions and requirements in the
following chapters:
▪ General safety precautions
▪ Preparation
NOTICE
Use a 2-stage vacuum pump with a non-return valve that
can evacuate to a gauge pressure of −100.7 kPa
(−1.007 bar)(5 Torr absolute). Make sure the pump oil
does not flow oppositely into the system while the pump is
not working.
NOTICE
Use this vacuum pump for R410A exclusively. Using the
same pump for other refrigerants may damage the pump
and the unit.
6.6.3
Checking refrigerant piping: Setup
f
i
h
a
b
d
c
e
k
l
m
j
g
a
Pressure reducing valve
b
Nitrogen
c
Weighing scales
d
R410A refrigerant tank (siphon system)
e
Vacuum pump
f
Charge hose
g
Service port for adding refrigerant
h
Liquid line stop valve
i
Gas line stop valve
j
Stop valve service port
k
Valve A
l
Valve B
m
Valve C
Valve
State of valve
Valve A
Close
Valve B
Open
Valve C
Open
Liquid line stop valve
Close
Gas line stop valve
Close
6.6.4
To check for leaks: Pressure leak test
NOTICE
After all the piping has been connected, make sure there is
no gas leak. Use nitrogen to perform a gas leak detection.
1
Break the vacuum by pressurising with nitrogen gas to a gauge
pressure of 4.0 MPa (40 bar). Never set the gauge pressure
higher than the maximum operation pressure of the unit, i.e.
4.0 MPa (40 bar).
6.6.5
To perform vacuum drying
To remove all moisture from the system, proceed as follows:
1
Evacuate the system for at least 2 hours to a target vacuum of
–100.7 kPa (–1.007 bar)(5 Torr absolute).