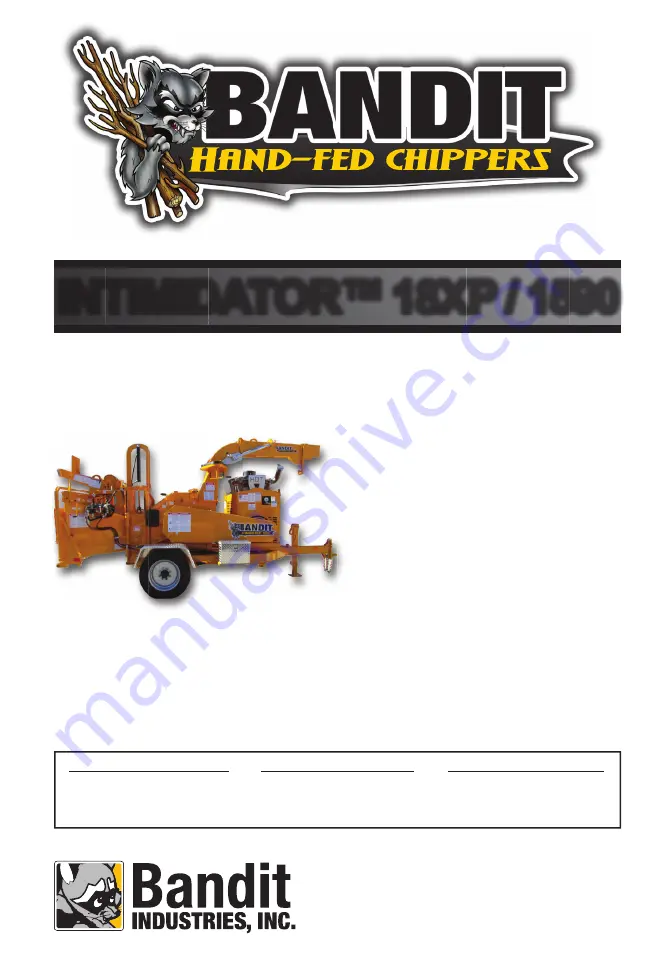
INTIMIDATOR 18XP / 1590
Model No: __________________________
Serial No: __________________________
Engine Make: _______________________
Serial No: __________________________
Clutch Make: ________________________
Model: ___________ S/N _____________
DEALER:
Name: _____________________________
Address: ___________________________
City/State: __________________________
Phone No: __________________________
Delivery Date: _______________________
Copyright 12/17
ATTENTION:
Depending on what replacement parts you are ordering, we will need the following information:
CHIPPER COMPONENTS
Serial Number
Model Number of Chipper
ENGINE COMPONENTS
Brand
Engine Serial Number
Engine Model Number
CLUTCH COMPONENTS
Brand
Clutch Serial Number
Clutch Model Number
INTIMIDATOR™ 18XP / 1590
OPERATING & PARTS MANUAL
6750 Millbrook Rd. • Remus, MI 49340 • 1-989-561-2270
MANUFACTURED BY BANDIT INDUSTRIES, INC
PHONE:
(
989
)
561-2270
PHONE:
(
800
)
952-0178 IN USA
FAX:
(
989
)
561-2273 ~ SALES DEPT.
FAX:
(
989
)
561-2962 ~ PARTS/SERVICE
WEBSITE:
www.banditchippers.com