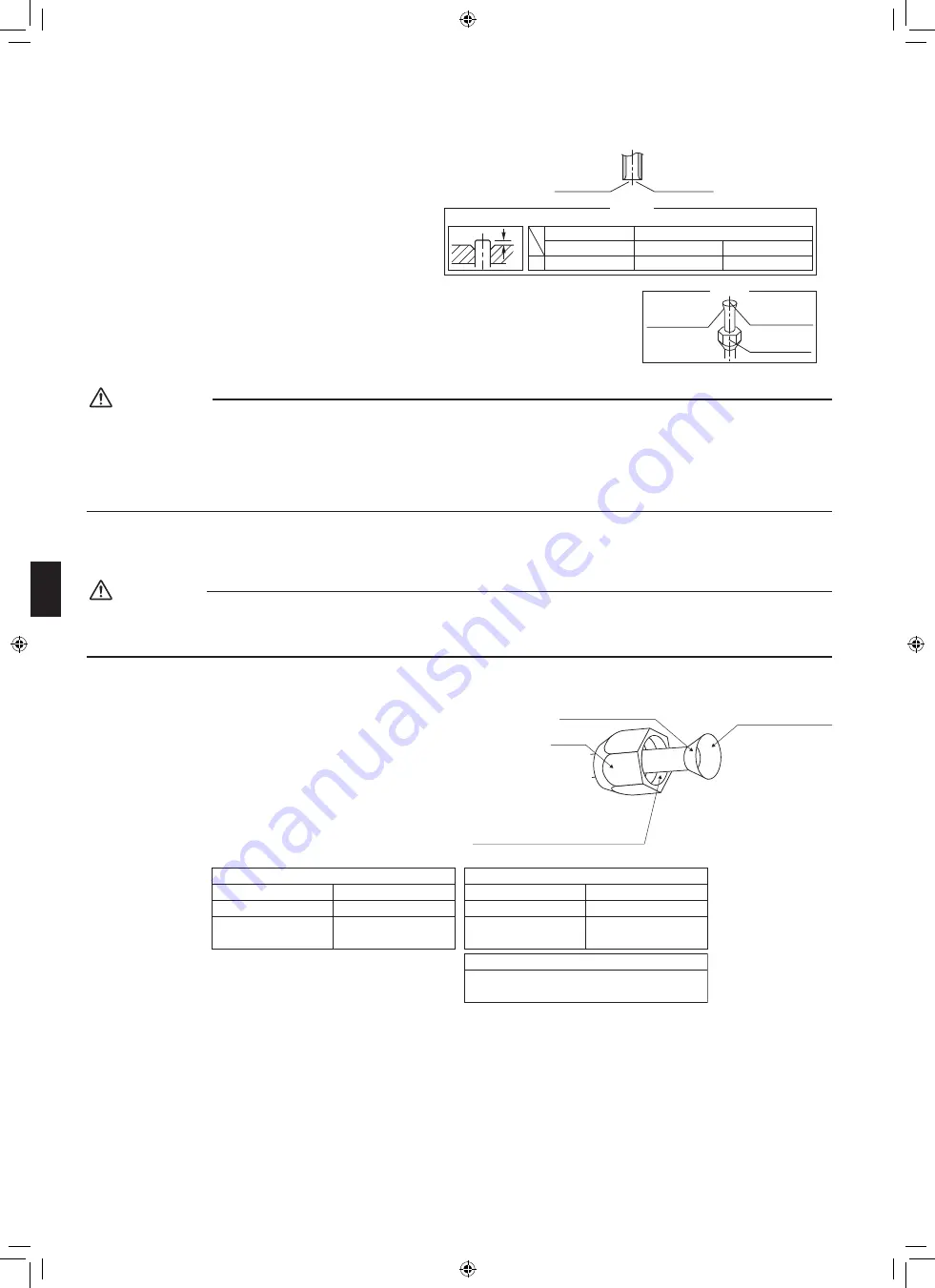
5
■
English
Outdoor Unit Installation
3.
Flaring the pipe end
1) Cut the pipe end with a pipe cutter.
2) Remove burrs with the cut surface facing
downward so that the chips do not enter the pipe.
3) Put the flare nut on the pipe.
4) Flare the pipe.
5) Check that the flaring is properly made.
(Cut exactly at
right angles.)
Remove burrs.
Set exactly at the position shown below.
A
Flaring
Die
Check
Flare’s inner
surface must
be flaw-free.
The pipe end must
be evenly flared in
a perfect circle.
Make sure that the
flare nut is fitted.
A
0-0.5mm
Clutch-type
Flare tool for R410A
1.0-1.5mm
Clutch-type (Rigid-type)
1.5-2.0mm
Wing-nut type (Imperial-type)
Conventional flare tool
WARNING
• Do not use mineral oil on flared part.
• Prevent mineral oil from getting into the system as this would reduce the lifetime of the units.
• Never use piping which has been used for previous installations. Only use parts which are delivered with the unit.
• Do never install a drier to this R410A unit in order to guarantee its lifetime.
• The drying material may dissolve and damage the system.
• Incomplete flaring may cause refrigerant gas leakage.
4.
Refrigerant piping work
CAUTION
• Use the flare nut fixed to the main unit. (To prevent cracking of the flare nut by aged deterioration.)
• To prevent gas leakage, apply refrigeration oil only to the inner surface of the flare. (Use refrigeration oil for R410A.)
• Use torque wrenches when tightening the flare nuts to prevent damage to the flare nuts and gas leakage.
• Align the centres of both flares and tighten the flare nuts 3
or 4 turns by hand. Then tighten them fully with the torque
wrenches.
Do not apply refrigeration
oil to the outer surface.
Flare nut
Apply refrigeration oil to
the inner surface of the
flare.
Do not apply refrigeration oil to the flare nut
to avoid tightening with excessive torque.
[Apply oil]
Flare nut tightening torque
Gas side
Liquid side
3/8 inch
1/4 inch
32.7-39.9N • m
(333-407kgf • cm)
14.2-17.2N • m
(144-175kgf • cm)
Valve cap tightening torque
Gas side
Liquid side
3/8 inch
1/4 inch
21.6-27.4N • m
(220-280kgf • cm)
21.6-27.4N • m
(220-280kgf • cm)
Service port cap tightening torque
10.8-14.7N
• m
(110-150kgf
• cm)
01_EN_3P297037-2D.indd 5
11/1/2012 11:04:42 AM