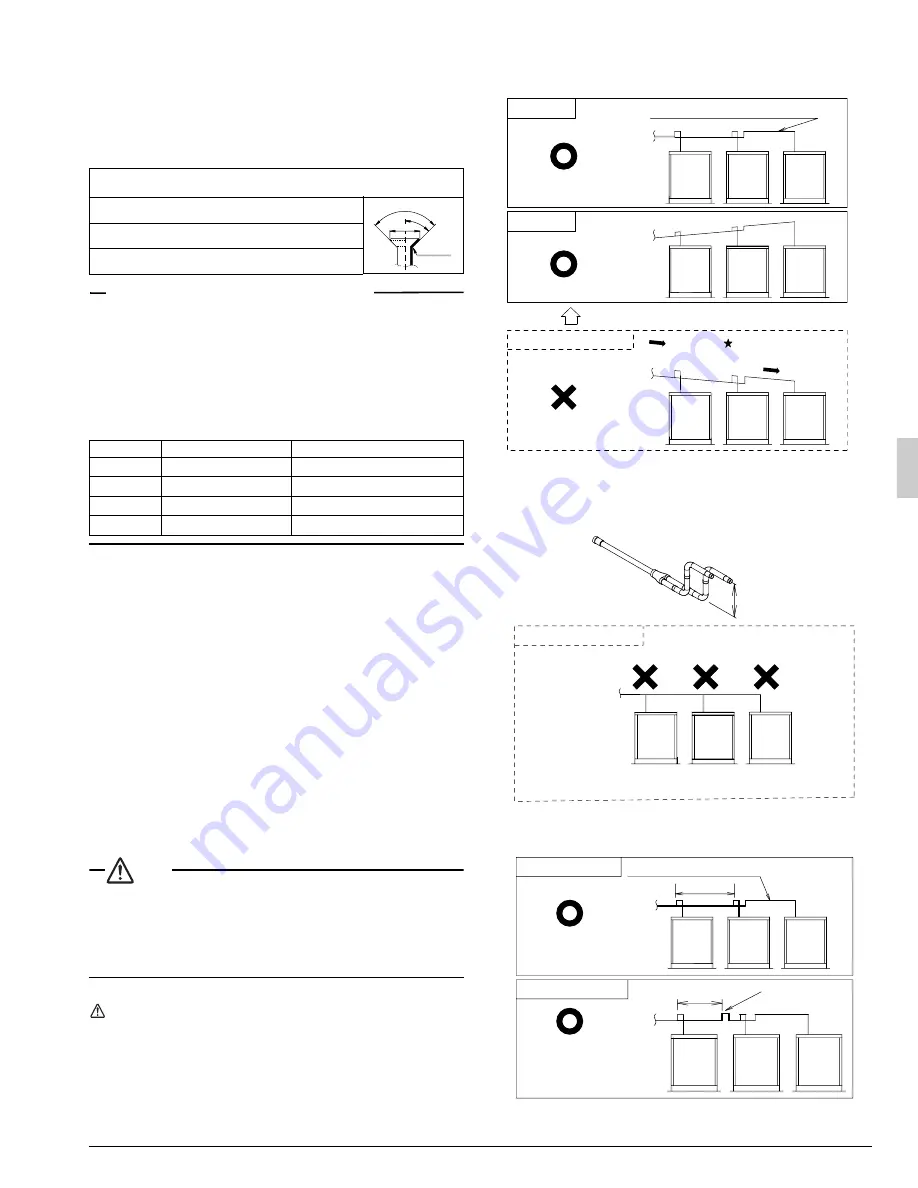
English
12
Precautions when connecting pipes
• See the following table for flare part machining dimensions.
• When connecting the flare nuts, apply refrigerant oil to the inside of
the flares and turn them three or four times at first.
(Use ester oil or ether oil.)
• See the following table for tightening torque.
(Applying too much torque may cause the flares to crack.)
• After all the piping has been connected, check the gas leak with
nitrogen.
Not recommendable but in case of emergency
You must use a torque wrench but if you are obliged to install the unit
without a torque wrench, you may follow the installation method men-
tioned below.
After the work is finished, make sure to check that there is no gas
leak.
When you keep on tightening the flare nut with a spanner, there is a
point where the tightening torque suddenly increases. From that posi-
tion, further tighten the flare nut the angle shown below:
(Unit: in.)
9-4 Connecting the refrigerant piping
Connect piping to outside unit by using accessory pipes
(Refer to figure 20)
1.
Gas side piping
2.
(field supply)
3.
Gas side accessory pipe (for suction gas (1))
4.
Liquid side pipe (field supply)
5.
Flare nut (Included in the unit)
6.
Accessory pipes (for discharge gas and suction gas (2))
is not used.
7.
Piping on discharge gas side (field supply)
8.
Piping on suction gas side (field supply)
9.
Cut off the hatched area and use it as a cover for the drilled.
10.
Hatched area
11.
Accessory pipe (for discharge gas)
12.
Accessory pipe (for suction gas)
13.
Guideline for pipe machining
14.
Accessory pipe (for suction gas (2))
15.
Brazing
16.
Accessory pipe (for suction gas (1))
17.
Before fitting to the product, apply brazing.
NOTE
•
Be sure to use the attached pipe when carrying out piping work in
the field.
•
Be sure that the local piping does not touch other pipes, the bottom
panel or side panel. Especially for the bottom and side connection, be
sure to protect the local piping with the provided insulation, to prevent
it from coming into contact with the casing.
Precautions for installation of units
NOTE
•
The outside unit multi connection piping kit that is sold separately as
an option (BHFP2 84U, BHFP2 84U) is neces-
sary for the multi installation of outside units.
• See the installation manual attached to the kit with attention to instal-
lation restrictions described in “connecting the refrigerant piping”
when installing.
〈
Cautions for installation of multiple outdoor units
〉
1.
The piping between the outdoor units must be routed level or slightly
upward to avoid the risk of oil detention to the piping side.
2.
The gas piping (both discharge and suction gas pipings in case of
the heat recovery system) after branched, install without fail a trap of
8 in. or more using the piping included in the piping kit for connecting
the outside unit. Otherwise, the refrigerant may stay within the pip-
ing, causing any damage to the outside unit.
3.
If the piping length between the outside unit connecting pipe kit or
between the outside units exceeds 80 in., create a rise of 8 in. or
more in the gas line within a length of 80 in. from the kit.
pipe size
(in.)
tightening torque
(ft. · lbf)
A
(in.)
flare shape
φ
3/8”
24.1 - 29.4
0.504 - 0.520
φ
1/2”
36.5 - 44.5
0.638 - 0.654
φ
5/8”
45.6 - 55.6
0.760 - 0.776
Pipe size
Further tightening angle
Recommended arm length of tool
φ
3/8”
60 to 90 degrees
Approx. 7-7/8
φ
1/2”
30 to 60 degrees
Approx. 9-13/16
φ
5/8”
30 to 60 degrees
Approx. 11-13/16
φ
3/4”
20 to 35 degrees
Approx. 17-3/4
R=0.016~0.031
45˚±2
90˚±2
A
Pattern 1
Pattern 2
Prohibited pattern
to indoor
unit
to indoor
unit
to indoor
unit
Downward
inclination
Downward
inclination
Change to pattern 1 or pattern 2
Oil remains in piping
Piping between outside units
8 in. or more
No trap has been installed in the gas piping.
★
Oil may remain in the farthest outside unit.
Change to pattern 1 or pattern 2
to indoor unit
Prohibited pattern
to indoor
unit
to indoor
unit
If 80 in. or less
If 80 in. or more
80 in. or less
80 in. or less
Rising height:
8 in. or more
Piping between outside unit