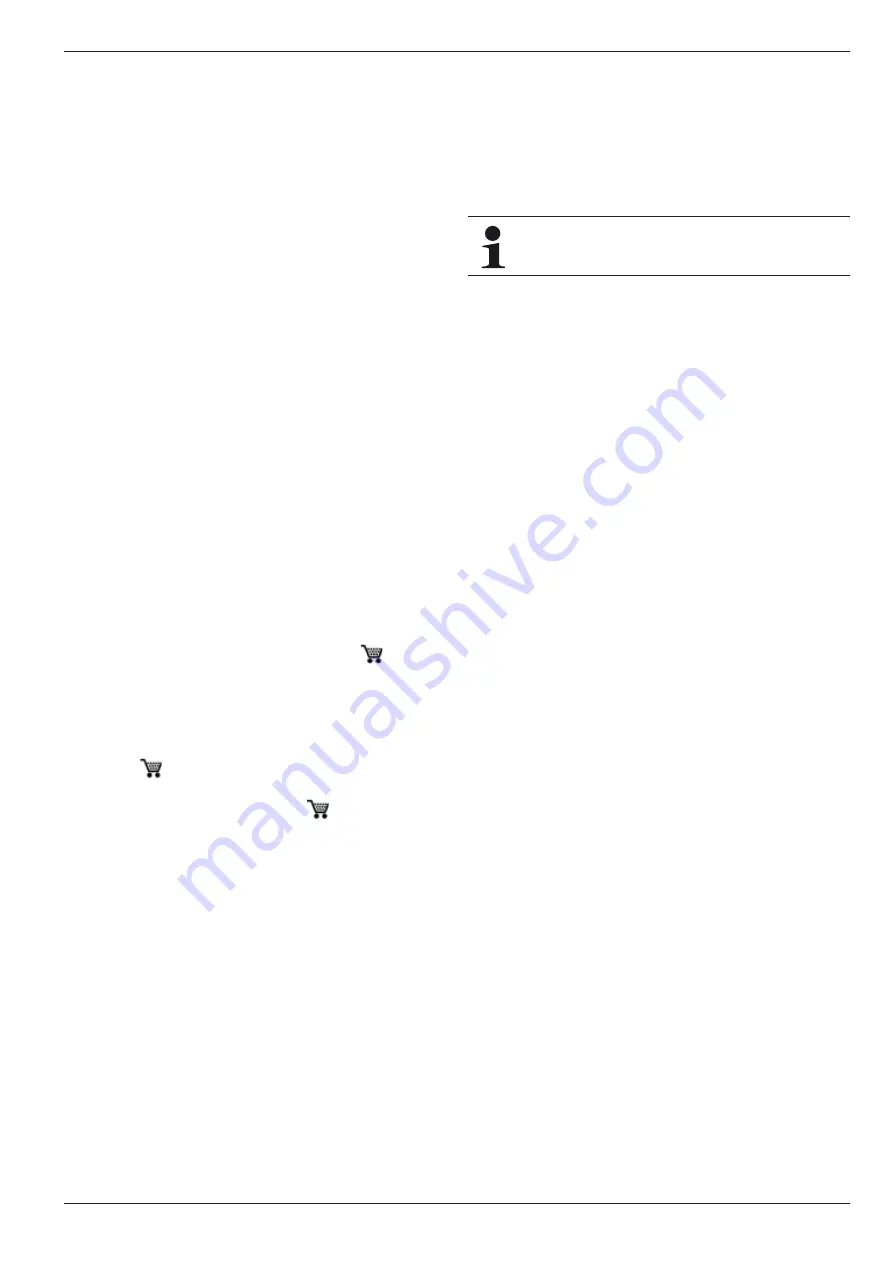
3
x
Product description
FA ROTEX A1 BOe - 02/2014
7
3.2 Brief description
The ROTEX Oil condensing boiler in the A1 BO series is a fully
preassembled oil condenser unit.
Operating instructions
The ROTEX Oil condensing boiler A1 BO is designed to be
operated independently of the room air (concentric flue gas/air
inlet piping). The burner suctions the combustion air directly in
through an installation shaft or a double-walled flue gas pipe. This
operating mode has several advantages:
– The heating room does not need any ventilation opening into
the open air and therefore does not cool down.
– Lower energy consumption.
– Additional energy recovery in the flue gas pipe through pre-
heating the combustion air.
– Contamination from the environment of the burner are not
suctioned in. The heating room can thus be used as a
work-space, laundry room etc. at the same time.
– Possible to set up in loft areas or attic.
The collecting condensate is neutralised in the integrated
ROTEX condensate treatment unit and then conducted into the
drainage system through a plastic tube.
Safety management
The safety management of the Oil condensing boiler is handled
entirely by the electronic controller. If there is water shortage, oil
shortage or undefined operating conditions, there is a safety
shutdown. A corresponding fault signal provides an engineer with
all the necessary information for troubleshooting.
Electronic control
An electronic digital controller combined with the "intelligent" au-
tomatic firing unit of the burner controls all heating and hot water
functions automatically for the direct heating circuit and a storage
tank charging circuit.
Optionally, connected mixer modules
RoCon M1
(
15 70 68
)
can be used to connect and regulate one or more mixed circuits.
All settings, displays and functions are carried out by the RoCon
B1 controller. The display and operating elements offer con-
venient operating possibilities.
As an option, for increased convenience, a digital room controller
(
RoCon U1
,
15 70 34
) is available as an option. This can be
used as a remote control and a room thermostat.
Using the optional gateway (
RoCon G1
,
15 70 56
), the con-
troller can be connected to the internet. This means that the
ROTEX A1 BO can be controlled remotely via mobile phone
(using an App).
Condensing technology
Condensing technology makes optimum use of the energy con-
tained in the heating oil. The flue gas is cooled down in the boiler
and in the flue system - when operated independently of ambient
air - such that the temperature is below the dew point. Part of the
water vapour created on combustion of the oil thereby con-
denses. The condensation heat is fed to the heating, in contrast
to low-temperature boilers, thus making it possible to achieve
over 100% efficiency.
Fuel
The ROTEX Oil condensing boiler A1 BO can be operated using
standard or low-sulphur heating oil (sulphur content <50 ppm).
It is prepared for combustion of heating oil with biogenic content.
As things currently stand, admixing bio-heating oil up to 20 %
(B20) is permitted without an additional conversion being re-
quired.
Condensate treatment
The condensate generated during the combustion in an Oil con-
densing boiler has a pH value of 1.8- 3.7. It must be neutralised
before it enters the drainage system.
The ROTEX condensate treatment unit fulfils the following
functions:
– Removes floating particles in the settling basin,
– Neutralises the condensate in the shell limestone.
ROTEX recommends using EL low sulphur heating oil
in order to achieve the highest efficiency and to keep
the maintenance expenditure low.