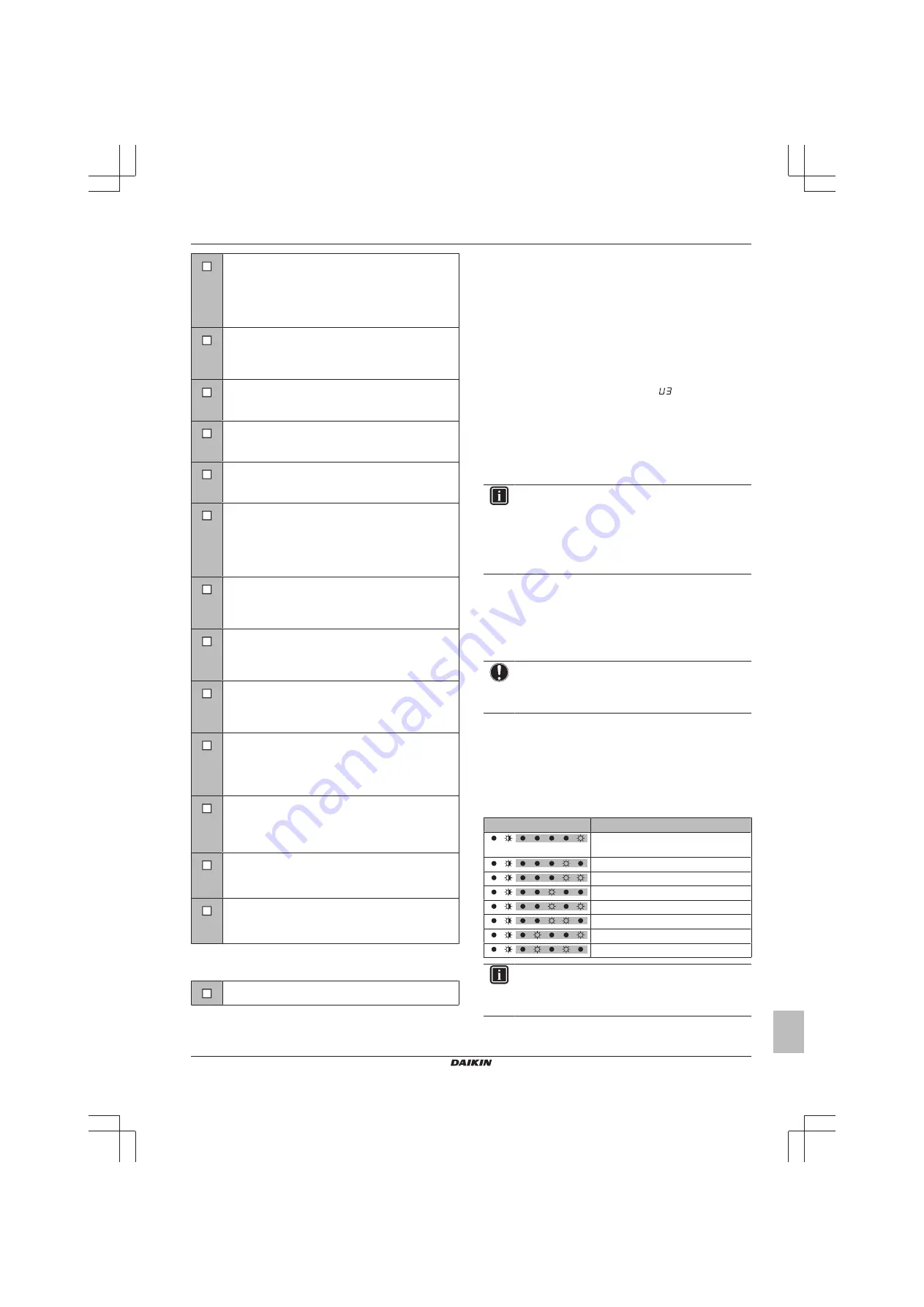
7 Commissioning
Installation and operation manual
21
RKXYQ5T7Y1B
VRV IV compressor unit for indoor installation
4P408443-1 – 2015.07
Fuses, circuit breakers, or protection devices
Check that the fuses, circuit breakers, or the locally
installed protection devices are of the size and type
specified
in
the
chapter
. Be sure that neither a fuse nor a
protection device has been bypassed.
Internal wiring
Visually check the electrical component box and the
inside of the unit on loose connections or damaged
electrical components.
Pipe size and pipe insulation
Be sure that correct pipe sizes are installed and that the
insulation work is properly executed.
Stop valves
Be sure that the stop valves are open on both liquid and
gas side.
Damaged equipment
Check the inside of the unit on damaged components or
squeezed pipes.
Refrigerant leak
Check the inside of the unit on refrigerant leakage. If there
is a refrigerant leak, try to repair the leak. If the repair is
unsuccessful, call your local dealer. Do not touch any
refrigerant which has leaked out from refrigerant piping
connections. This may result in frostbite.
Oil leak
Check the compressor for oil leakage. If there is an oil
leak, try to repair the leak. If the repairing is unsuccessful,
call your local dealer.
Air inlet/outlet
Check that the air inlet and outlet of the unit is not
obstructed by paper sheets, cardboard, or any other
material.
Additional refrigerant charge
The amount of refrigerant to be added to the unit shall be
written on the included "Added refrigerant" plate and
attached to the rear side of the front cover.
Installation date and field setting
Be sure to keep record of the installation date on the
sticker on the rear of the front panel according to
EN60335‑2‑40 and keep record of the contents of the field
setting(s).
Insulation and air leaks
Make sure the unit is fully insulated and checked for air
leaks.
Possible consequence:
Condensate water might drip.
Drainage
Make sure drainage flows smoothly.
Possible consequence:
Condensate water might drip.
External static pressure
Make sure the external static pressure is set.
Possible consequence:
Insufficient cooling or heating.
7.3
Checklist during commissioning
To perform a
test run
.
7.3.1
About test run
The procedure below describes the test operation of the complete
system. This operation checks and judges following items:
▪ Check of wrong wiring (communication check with indoor units
and heat exchanger unit).
▪ Check of the stop valves opening.
▪ Check of wrong piping.
Example:
Gas or liquid pipes switched.
▪ Judgement of piping length.
Make sure to carry out the system test operation after the first
installation. Otherwise, the malfunction code
will be displayed on
the user interface and normal operation or individual indoor unit test
run cannot be carried out.
Abnormalities on indoor units cannot be checked for each unit
separately. After the test operation is finished, check the indoor units
one by one by performing a normal operation using the user
interface. Refer to the indoor unit installation manual for more details
concerning the individual test run.
INFORMATION
▪ It may take 10 minutes to achieve a uniform refrigerant
state before the compressor starts.
▪ During the test operation, the refrigerant running sound
or the magnetic sound of a solenoid valve may become
loud and the display indication may change. These are
not malfunctions.
7.3.2
To perform a test run (7-LEDs display)
1
Make sure all field settings you want are set; see
.
2
Turn ON the power to the compressor unit, heat exchanger unit,
and the connected indoor units.
NOTICE
Be sure to turn on the power 6 hours before operation in
order to have power running to the crankcase heater and
to protect the compressor.
3
Make sure the default (idle) situation is existing (H1P is OFF);
see
"6.1.4 To access mode 1 or 2" on page 16
. Push BS4 for 5
seconds or more. The unit will start test operation.
Result:
The test operation is automatically carried out, the
compressor unit H2P flashes and the indication "Test operation"
and "Under centralised control" will display on the user interface
of indoor units.
Steps during the automatic system test run procedure:
Step
Description
Control before start up (pressure
equalisation)
Cooling start up control
Cooling stable condition
Communication check
Stop valve check
Pipe length check
Pump down operation
Unit stop
INFORMATION
During the test operation, it is not possible to stop the unit
operation from a user interface. To abort the operation,
press BS3. The unit will stop after ±30 seconds.
4
Check the test operation results on the compressor unit 7‑LEDs
display.