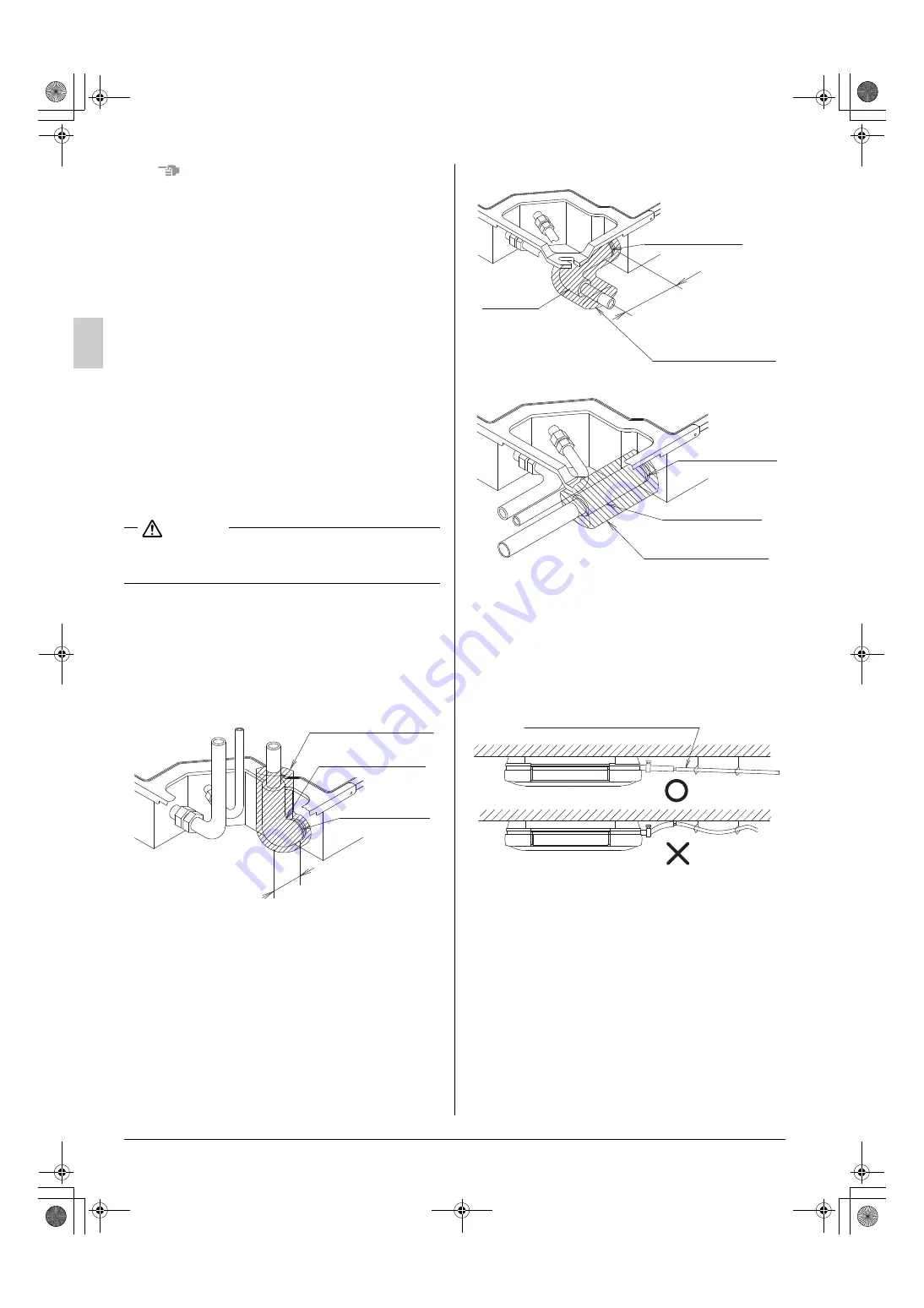
11
English
NOTE
1.
The proper pressure for having nitrogen flow through the
piping is approximately 0.02MPa, a pressure that makes
one feel like breeze and can be obtained through a pressure
reducing valve.
2.
Do not use flux when brazing refrigerant piping.
Use phosphor copper brazing filler metal (BCuP-2: JIS Z
3264/B-Cu93P-710/795: ISO 3677) that does not require
flux.
(If chlorinated flux is used, the piping will be corroded and,
in addition if fluorine is contained, the refrigerant oil will be
deteriorated and the refrigerant circuit will be affected
badly.)
3.
When carrying out leakage test of refrigerant piping and the
indoor unit after the installation of indoor unit is finished,
confirm the connecting outdoor unit installation manual for
test pressure.
Refer to also the outdoor unit installation manual or techni-
cal document for refrigerant piping.
4.
In case of refrigerant shortage due to forgetting additional
refrigerant charge etc., it will result in malfunction such as
does not cool or does not heat.
Refer to the outdoor unit installation manual or technical
document for refrigerant piping.
CAUTION
Do not use antioxidant when brazing piping.
It may result in malfunction of components and clogging of
piping due to residue.
7.
DRAIN PIPING WORK
(1) Carry out drain piping.
Carry out drain piping so that drainage can ensured.
•
Drain piping can be connected from 3 directions.
(Refer to Fig. 25, 26, and 27)
•
Select the piping diameter equal to or larger than (except
for riser) that of the connection piping (polyvinyl chloride
piping, nominal diameter 20mm, outside diameter
26mm).
•
Install the drain piping as short as possible with down-
ward inclination of 1/100 or more and without where air
may stagnate.
(Refer to Fig. 28)
(It may cause abnormal sound such as bubbling noise)
Sealing material (Large) (8)
(accessory)
Elbow (10) (accessory)
Metal clamp (2)
(accessory)
Shorter side
Fig. 25
(Upward piping)
Fig. 26
(Backward piping)
Metal clamp (2)
(accessory)
Longer side
Sealing material (Large) (8)
(accessory)
Elbow (10)
(accessory)
Fig. 27
(Rightward piping)
Metal clamp (2)
(accessory)
Drain hose (1)
(accessory)
Sealing material (Large) (8)
(accessory)
Fig. 28
Downward inclination of 1/100 or more
Not acceptable
OK
01_EN_3P177351-7S.fm Page 11 Thursday, March 21, 2013 10:19 PM