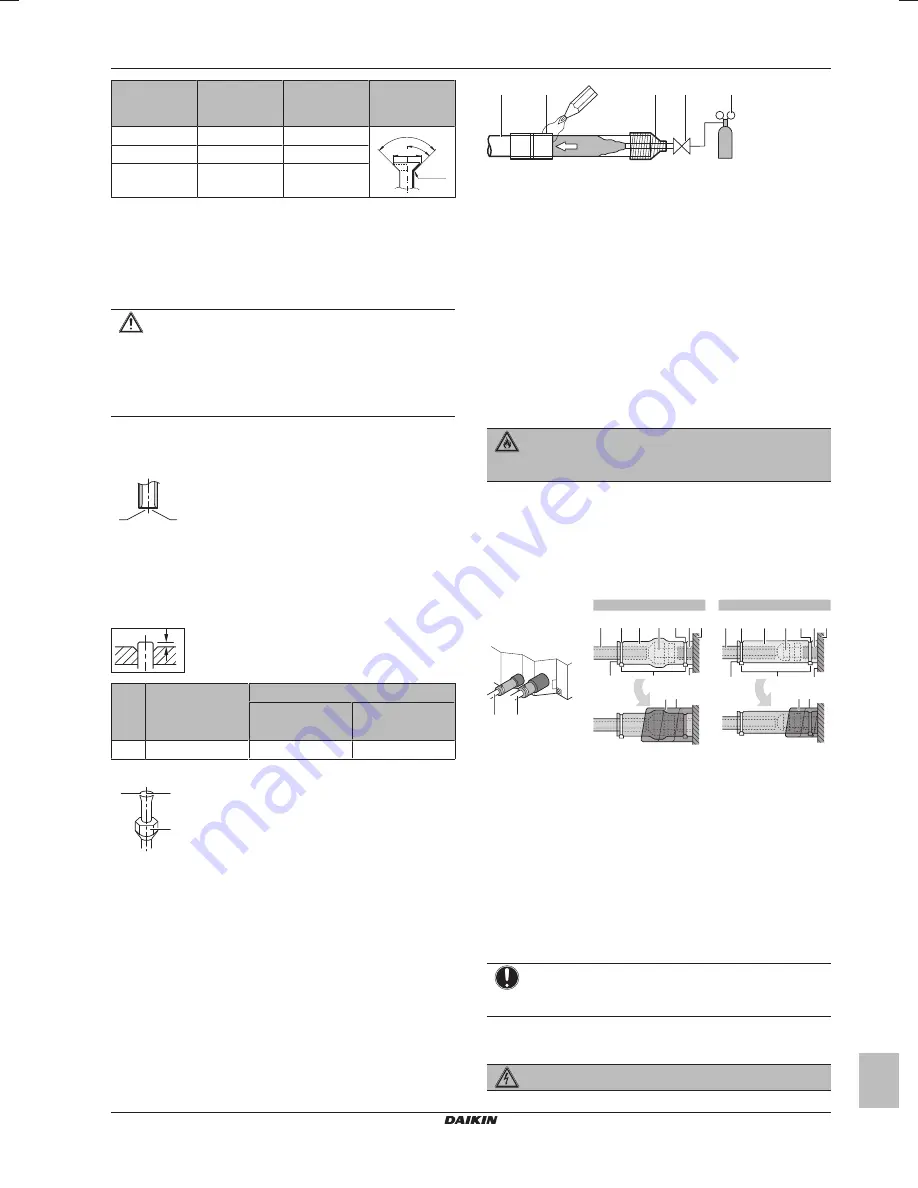
5 Installation
Installation and operation manual
9
FFA25~60A2VEB
Split system air conditioners
4P456960-1 – 2017.03
Piping size
(mm)
Tightening
torque (N•m)
Flare
dimensions (A)
(mm)
Flare shape
(mm)
Ø6.4
15~17
8.7~9.1
R=0.4~0.8
45° ±2
90°±2
A
Ø9.5
33~39
12.8~13.2
Ø12.7
50~60
16.2~16.6
5.2.4
Pipe bending guidelines
Use a pipe bender for bending. All pipe bends should be as gentle
as possible (bending radius should be 30~40 mm or larger).
5.2.5
To flare the pipe end
CAUTION
▪ Incomplete flaring may cause refrigerant gas leakage.
▪ Do NOT re-use flares. Use new flares to prevent
refrigerant gas leakage.
▪ Use flare nuts that are included with the unit. Using
different flare nuts may cause refrigerant gas leakage.
1
Cut the pipe end with a pipe cutter.
2
Remove burrs with the cut surface facing down so that the
chips do not enter the pipe.
a
b
a
Cut exactly at right angles.
b
Remove burrs.
3
Remove the flare nut from the stop valve and put the flare nut
on the pipe.
4
Flare the pipe. Set exactly at the position as shown in the
following illustration.
A
Flare tool for
R410A or R32
(clutch type)
Conventional flare tool
Clutch type
(Ridgid-type)
Wing nut type
(Imperial-type)
A
0~0.5 mm
1.0~1.5 mm
1.5~2.0 mm
5
Check that the flaring is properly made.
a
b
c
a
Flare’s inner surface must be flawless.
b
The pipe end must be evenly flared in a perfect circle.
c
Make sure the flare nut is fitted.
5.2.6
To braze the pipe end
The indoor unit and outdoor unit have flare connections. Connect
both ends without brazing. If brazing should be needed, take the
following into account:
▪ When brazing, blow through with nitrogen to prevent creation of
large quantities of oxidised film on the inside of the piping. This
film adversely affects valves and compressors in the refrigerating
system and prevents proper operation.
▪ Set the nitrogen pressure to 20 kPa (0.2 bar) (just enough so it
can be felt on the skin) with a pressure-reducing valve.
a
b
c
d
e
f
f
a
Refrigerant piping
b
Part to be brazed
c
Taping
d
Manual valve
e
Pressure-reducing valve
f
Nitrogen
▪ Do NOT use anti-oxidants when brazing pipe joints.
Residue can clog pipes and break equipment.
▪ Do NOT use flux when brazing copper-to-copper refrigerant
piping. Use phosphor copper brazing filler alloy (BCuP), which
does not require flux.
Flux has an extremely harmful influence on refrigerant piping
systems. For instance, if chlorine based flux is used, it will cause
pipe corrosion or, in particular, if the flux contains fluorine, it will
deteriorate the refrigerant oil.
5.2.7
To connect the refrigerant piping to the
indoor unit
WARNING: FLAMMABLE MATERIAL
The R32 refrigerant (if applicable) in this unit is mildly
flammable.
(a)
(a)
Refer to the outdoor unit specifications for the type of
refrigerant to be used.
▪
Pipe length
. Keep refrigerant piping as short as possible.
▪
Flare connections
. Connect refrigerant piping to the unit using
flare connections.
▪
Insulation
. Insulate the refrigerant piping on the indoor unit as
follows:
A
B
a
d
c
e f
b
b
a
d
c
e f
b
b
2
4
3
g
1
2
3
4
g
A
B
1
A
Gas piping
B
Liquid piping
a
Insulation material (field supply)
b
Cable tie (accessory)
c
Insulation pieces: Large (gas pipe), small (liquid pipe)
(accessories)
d
Flare nut (attached to the unit)
e
Refrigerant pipe connection (attached to the unit)
f
Unit
g
Sealing pads: Medium 1 (gas pipe), medium 2 (liquid pipe)
(accessories)
1
Turn up the seams of the insulation pieces.
2
Attach to the base of the unit.
3
Tighten the cable ties on the insulation pieces.
4
Wrap the sealing pad from the base of the unit to the top of
the flare nut.
NOTICE
Make sure to insulate all refrigerant piping. Any exposed
piping might cause condensation.
5.3
Connecting the electrical wiring
DANGER: RISK OF ELECTROCUTION