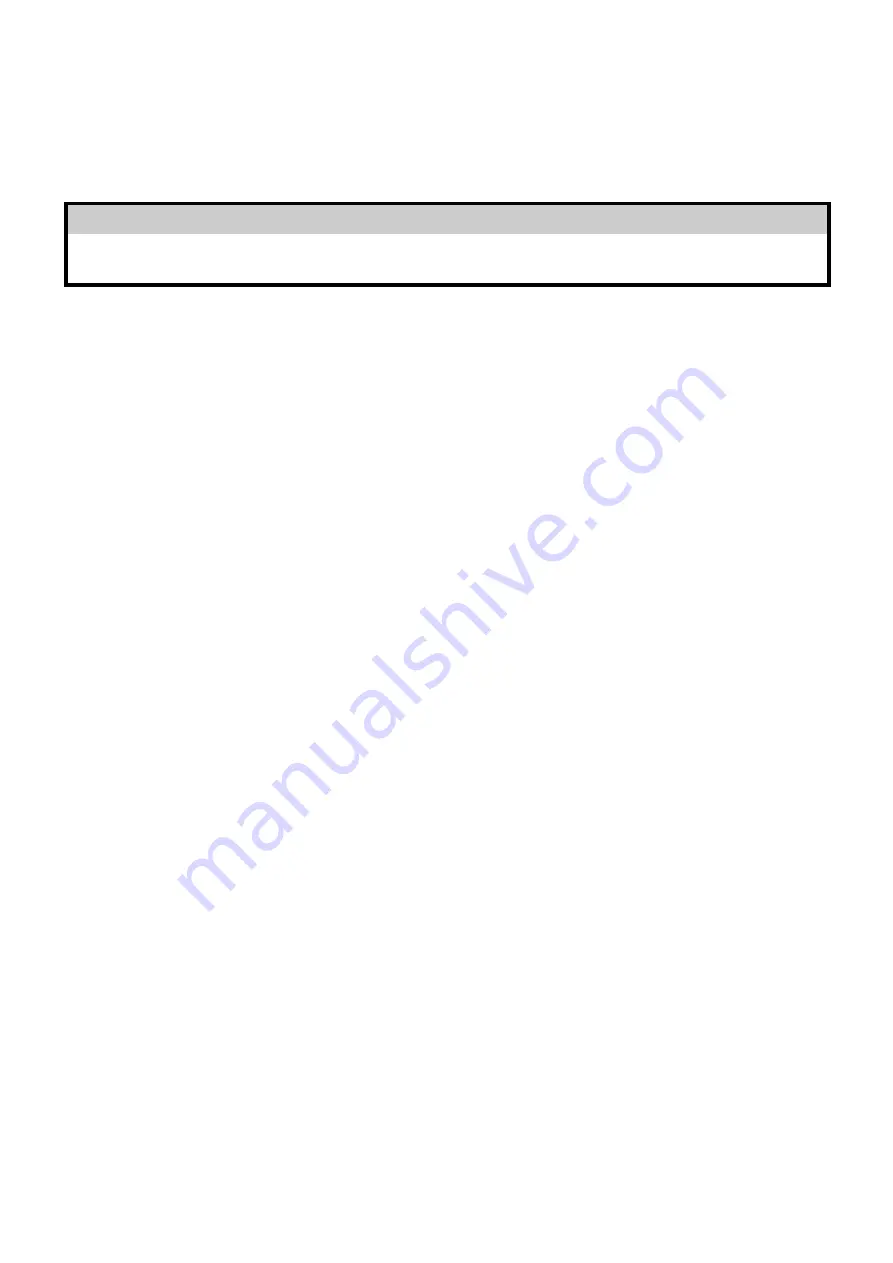
D-EIMWC003D01-17EN-AR - 20/80
The cooling circuit also installs an electronic overflow valve that, in addition to managing the level of refrigerant
in the heat exchangers and guaranteeing the correct operation of the compressor, also manages the PUMP-
DOWN function.
All the described components are managed by an innovative microprocessor control system that, by monitoring
all the machine operating parameters, optimizes operations.
A diagnostic system helps the operator in identifying alarm and fault causes.
WARNING
Before starting the compressors ensure that all valves are open and the closing caps are repositioned and
tightened.
Cooling cycle description
The low temperature refrigerant gas coming from the evaporator is sucked by the compressor and flows through
the electric motor, cooling it. It is subsequently compressed and during this phase the refrigerant mixes with the
oil, injected in the compressor, from the separator.
The high-pressure oil-refrigerant mixture is introduced inside the three-stage high efficiency oil separator which
performs the separation. The oil deposited on the bottom of the separator is sent, by pressure difference, to the
compressor again while the refrigerant separated from the oil is sent to the condenser.
The refrigerant fluid inside the condenser, which crosses the heat exchanger pipes in countercurrent,
desuperheats and starts to condense. The desuperheating heat and condensation is subtracted from the
condensation water which heats accordingly.
The condensed fluid at saturation temperature passes through the subcooling section, where it yields heat to
further increase cycle efficiency. The subcooled fluid flows through the overflow device which, through a
pressure drop, initiates the expansion process by vaporizing a part of the refrigerant liquid.
The result at this point is a mixture of liquid and gas at low pressure and temperature, poor in heat, which is
introduced into the evaporator.
The liquid-vapor refrigerant after being evenly distributed along the tube bundle exchanges heat with the water
to be cooled by reducing the temperature, and it gradually changes state until being fully evaporated.
Reaching the vapor state, it leaves the evaporator to be sucked by compressor again and restart the cycle.
Evaporator
The evaporator is a flooded shell and tube type with water flowing inside the tubes and the gas refrigerant
outside. Normally it does not require any maintenance and service. Should a tube require replacement, the old
tube can be removed and replaced. The water dome gasket must be replaced after tube cleaning and/or
replacement.
Condenser
The condenser is a shell and tube type with water flowing inside the tubes and the refrigerant outside. The
condenser tubes are externally finned and expanded on the tube plate. A subcooler is built into the condenser
on all units. Should a tube require replacement, the old tube can be removed and replaced. The water dome
gasket must be replaced after tube cleaning and/or replacement.
Expansion valve
The expansion valve is electrically controlled by the electronic controller by means of a specifically designed
electronic board. A special algorithm designed for machines with flooded evaporators, manages the refrigerant
flow to the evaporator according to machine operating parameters. In the event of blackout, the expansion valve
automatically closes thanks to an electric power accumulation system placed inside the electronic control board
(supercap)
Compressors
The refrigeration compressor is the single screw type with the rotation shaft directly coupled to the electric
motor.
The vapor flows through the electric motor cooling the windings before entering the suction ports. Sensors able
to constantly monitor temperature are located inside the motor windings to fully protect the motor against
Summary of Contents for EWWD VZ Series
Page 3: ...D EIMWC003D01 17EN AR 3 80 Description of the labels applied to the unit Single circuit unit...
Page 26: ...D EIMWC003D01 17EN AR 26 80 Fig 6 Typical single circuit cooling circuit...
Page 41: ...EIMWC003D01 17EN AR 41 80 EWWD VZ 055 0055 05 HFC R134a D EIMWC003D01 17EN AR...
Page 43: ...D EIMWC003D01 17EN AR 43 80...
Page 45: ...D EIMWC003D01 17EN AR 45 80 0 6 0 7 3 1 4 1 0 05...
Page 47: ...EIMWC003D01 17EN AR 47 80 0 00 Daikin Applied Europe S p A Daikin Applied Europe S p A...
Page 48: ...EIMWC003D01 17EN AR 48 80 0...
Page 50: ...EIMWC003D01 17EN AR 50 80 Daikin 00 Victaulic 3 4 0 0...
Page 51: ...EIMWC003D01 17EN AR 51 80 5 05 Daikin Applied Europe...
Page 52: ...EIMWC003D01 17EN AR 52 80 EWWD VZ 3 05 00 05 00 60 00 4 05...
Page 53: ...EIMWC003D01 17EN AR 53 80 TWLE TWLE 0 0 51 3 000 4 000 51...
Page 55: ...EIMWC003D01 17EN AR 55 80 4 0 6 6 Daikin Applied Europe SpA 3 4 05 05 5 05 3 0 0 0 0...
Page 56: ...EIMWC003D01 17EN AR 56 80 05 4 0 0 3 4 0 0 0 3 0 4...
Page 58: ...EIMWC003D01 17EN AR 58 80 05 EWWD VZ 035 Q0 Daikin Applied Europe 0 35 EWWD VZ...
Page 59: ...EIMWC003D01 17EN AR 59 80 Daikin Daikin Daikin VVR...
Page 60: ...EIMWC003D01 17EN AR 60 80 supercap EWWD VZ 145 04 4155 15 VVR VVR 3...
Page 61: ...EIMWC003D01 17EN AR 61 80 055 0 0 Daikin Mobil EAL Artic 220H Daikin EWWD VZ Venturi 3 4...
Page 62: ...EIMWC003D01 17EN AR 62 80 0 PID niaiaD TLLnD WE TLLn WE HP...
Page 63: ...EIMWC003D01 17EN AR 63 80 IGBT EN 60204 1 5 PED d e f...
Page 65: ...EIMWC003D01 17EN AR 65 80 6...
Page 68: ...EIMWC003D01 17EN AR 68 80 4 0 6 05 3 4 1 1 05 00 0 5 5 00 03 04...
Page 69: ...EIMWC003D01 17EN AR 69 80 Daikin Applied Europe Spa 055 6 7 1 1 05...
Page 70: ...EIMWC003D01 17EN AR 70 80 Daikin Applied Europe Daikin Daikin...
Page 72: ...EIMWC003D01 17EN AR 72 80 6 O X X X X X X X 7 X X 1 X O X niaiaD...
Page 73: ...EIMWC003D01 17EN AR 73 80 00 Daikin...
Page 74: ...D EIMWC003D01 17EN AR 74 80 4102 86 CE DCP...
Page 75: ...EIMWC003D01 17EN AR 75 80 R134a GWP 0 0435 0 GWP...
Page 76: ...EIMWC003D01 17EN AR 76 80 0 0 0 3 0 0 3 x 0555 a b c d e f g h m n GWP p 2 x 0555...
Page 77: ...EIMWC003D01 17EN AR 77 80...
Page 78: ...EIMWC003D01 17EN AR 78 80 05...