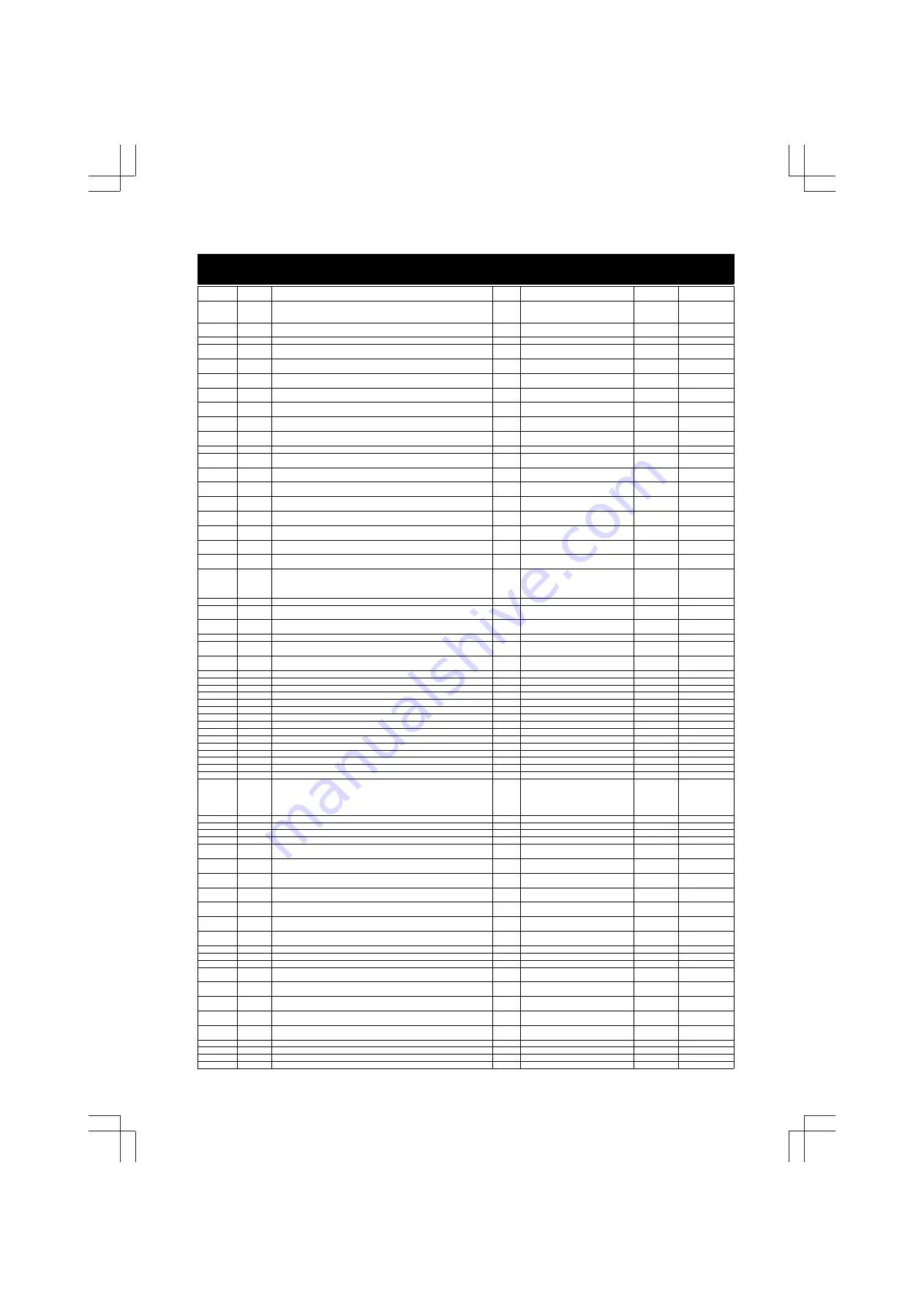
5/7
Breadcrumb
Field code
Setting name
Range, step
Default value
Date
Value
Field settings table
Installer setting at variance with
default value
A.8
[4-07]
R/W
0: No
1: Yes
A.8
[4-08]
R/W
0: No limitation
1: Continuous
2: Digital inputs
A.8
[4-09]
R/W
0: Current
1: Power
A.8
[4-0A]
0
A.8
[4-0B]
R/W
1~10°C, step: 0,5°C
1°C
A.8
[4-0D]
R/W
1~10°C, step: 0,5°C
3°C
A.8
[4-0E]
Is the installer on site?
R/W
0: No
1: Yes
A.8
[5-00]
R/W
0: Allowed
1: Not allowed
A.8
[5-01]
R/W
-15~35°C, step: 1°C
-4°C
A.8
[5-02]
R/W
0: Disabled
1: Enabled
A.8
[5-03]
R/W
-15~35°C, step: 1°C
0°C
A.8
[5-04]
10
A.8
[5-05]
R/W
0~50 A, step: 1 A
50 A
A.8
[5-06]
R/W
0~50 A, step: 1 A
50 A
A.8
[5-07]
R/W
0~50 A, step: 1 A
50 A
A.8
[5-08]
R/W
0~50 A, step: 1 A
50 A
A.8
[5-09]
R/W
0~20 kW, step: 0,5 kW
20 kW
A.8
[5-0A]
R/W
0~20 kW, step: 0,5 kW
20 kW
A.8
[5-0B]
R/W
0~20 kW, step: 0,5 kW
20 kW
A.8
[5-0C]
R/W
0~20 kW, step: 0,5 kW
20 kW
A.8
[5-0D]
R/W
0~5
1: 1P,(1/1+2)
4: 3PN,(1/2)
5: 3PN,(1/1+2)
A.8
[5-0E]
1
A.8
[6-00]
R/W
2~20°C, step: 1°C
2°C
A.8
[6-01]
R/W
0~10°C, step: 1°C
2°C
A.8
[6-02]
0
A.8
[6-03]
R/W
0~10 kW, step: 0,2 kW
3 kW
A.8
[6-04]
R/W
0~10 kW, step: 0,2 kW
0 kW
A.8
[6-05]
0
A.8
[6-06]
0
A.8
[6-07]
0
A.8
[6-08]
10
A.8
[6-09]
0
A.8
[6-0A]
55°C
A.8
[6-0B]
45°C
A.8
[6-0C]
45°C
A.8
[6-0D]
1
A.8
[6-0E]
60°C
A.8
[7-00]
0°C
A.8
[7-01]
2°C
A.8
[7-02]
R/O
0: 1 LWT zone
A.8
[7-03]
2,5
A.8
[7-04]
0
A.8
[7-05]
R/W
0: Very high
1: High
2: Medium
3: Low
4: Very low
A.8
[8-00]
1 min
A.8
[8-01]
30
A.8
[8-02]
0,5
A.8
[8-03]
50
A.8
[8-04]
R/W
0~95 min, step: 5 min
95 min
A.8
[8-05]
R/W
0: No
1: Yes
A.8
[8-06]
R/W
0~10°C, step: 1°C
3°C
A.8
[8-07]
R/W
[9-03]~[9-02], step: 1°C
18°C
A.8
[8-08]
R/W
[9-03]~[9-02], step: 1°C
20°C
A.8
[8-09]
R/W
[9-01]~[9-00], step: 1°C
45°C
A.8
[8-0A]
R/W
[9-01]~[9-00], step: 1°C
40°C
A.8
[8-0B]
13
A.8
[8-0C]
10
A.8
[8-0D]
16
A.8
[9-00]
R/W
37~55°C, step: 1°C
55°C
A.8
[9-01]
R/W
15~37°C, step: 1°C
25°C
A.8
[9-02]
R/W
18~22°C, step: 1°C
22°C
A.8
[9-03]
R/W
5~18°C, step: 1°C
5°C
A.8
[9-04]
R/W
1~4°C, step: 1°C
1°C
A.8
[9-05]
25
A.8
[9-06]
55
A.8
[9-07]
5
A.8
[9-08]
22
--
--
--
--
--
What is the maximum desired LWT for main zone in heating?
What is the mimimum desired LWT for main zone in heating?
What is the maximum desired LWT for main zone in cooling?
What is the mimimum desired LWT for main zone in cooling?
Leaving water temperature overshoot temperature.
What is the desired comfort main LWT in cooling?
What is the desired eco main LWT in cooling?
What is the desired comfort main LWT in heating?
What is the desired eco main LWT in heating?
--
--
--
--
--
Additional running time for the maximum running time.
Allow modulation of the LWT to control the room temp?
Leaving water temperature maximum modulation.
--
How many leaving water temperature zones are there?
--
--
Boiler efficiency
--
--
--
--
--
--
--
What is the capacity of the backup heater step 2?
--
--
--
--
--
What type of backup heater installation is used?
--
The temperature difference determining the heat pump ON temperature.
The temperature difference determining the heat pump OFF temperature.
--
What is the capacity of the backup heater step 1?
What is the requested limit for DI3?
What is the requested limit for DI4?
What is the requested limit for DI1?
What is the requested limit for DI2?
What is the requested limit for DI3?
What is the requested limit for DI4?
What is the equilibrium temperature for the building?
Space heating priority.
Space heating priority temperature.
--
What is the requested limit for DI1?
What is the requested limit for DI2?
Which power limitation mode is required on the system?
Which power limitation type is required?
--
Automatic cooling/heating changeover hysteresis.
Automatic cooling/heating changeover offset.
Is backup heater operation allowed above equilibrium temperature during space
heating operation?
Enable the second step of the backup heater?
(*1) EWYQ*_(*2) EWAQ*
4P469115-1B - 2017.06