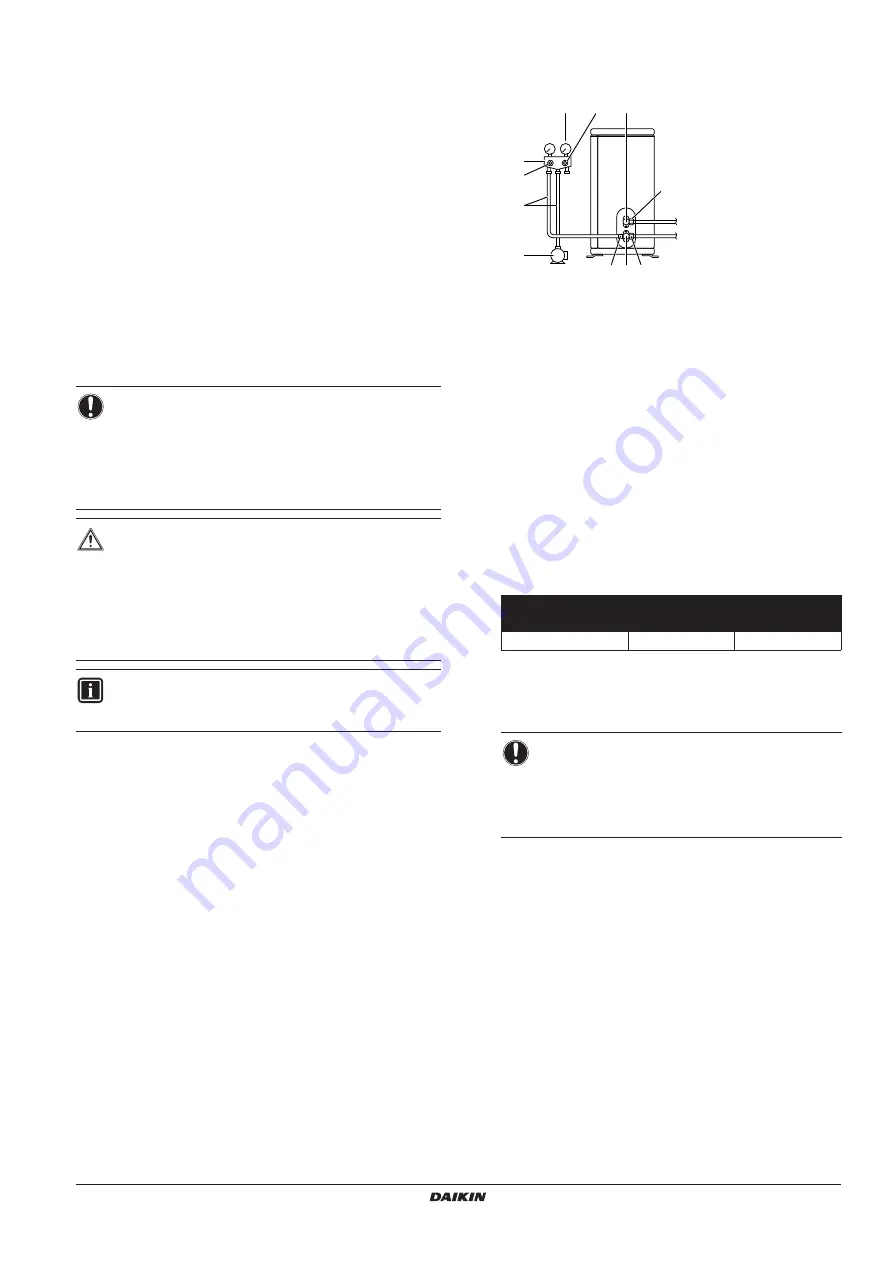
ERHQ006~0 ERLQ006~008BBV3
Outdoor unit for air to water heat pump
4PW68002-1A – 03.2011
Installation manual
11
11. L
EAK
TEST
AND
VACUUM
DRYING
When all piping work is complete and the outdoor unit is connected to
the indoor unit, it is necessary to:
■
check for any leakages in the refrigerant piping
■
to perform vacuum drying to remove all moisture in the
refrigerant piping.
If there is a possibility of moisture being present in the refrigerant
piping (for example, rainwater may have entered the piping), first
carry out the vacuum drying procedure below until all moisture has
been removed.
11.1. General guidelines
■
All piping inside the unit has been factory tested for leaks.
■
Use a 2-stage vacuum pump with a non-return valve which can
evacuate to a gauge pressure of –100.7 kPa (5 Torr absolute,
–755 mm Hg).
■
Connect the vacuum pump to the service port of the gas stop
valve.
■
If using additional refrigerant, perform air purging from the
refrigerant pipes and indoor unit using a vacuum pump, then
charge additional refrigerant.
■
Use a hexagonal wrench (4 mm) to operate the stop valve rod.
■
All refrigerant pipe joints should be tightened with a torque
wrench at the specified tightening torque. See
the refrigerant piping to the outdoor unit" on page 10
for details.
1
Pressure meter
2
Gauge manifold
3
Low-pressure valve (Lo)
4
High-pressure valve (Hi)
5
Charging hoses
6
Vacuum pump
7
Service port
8
Valve lids
9
Gas stop valve
10
Liquid stop valve
1
Connect the projection side (on which the worm pin is pressed)
of the charging hose coming from the gauge manifold to the gas
stop valve's service port.
2
Fully open the gauge manifold's low-pressure valve (Lo) and
completely close its high-pressure valve (Hi).
The high-pressure valve subsequently requires no operation.
3
Apply vacuum pumping. Check that the compound pressure
gauge reads –0.1 MPa (–760 mm Hg).
4
Close the gauge manifold's low-pressure valve (Lo) and stop the
vacuum pump.
Leave as is for 4-5 minutes and make sure that the coupling
meter needle does not go back.
5
Remove the covers from the liquid stop valve and gas stop valve.
6
Turn the liquid stop valve's rod 90 degrees counterclockwise with
a hexagonal wrench to open the valve.
Close it after 5 seconds, and check for gas leakage.
Using soapy water, check for gas leakage from the indoor unit's
flare and the outdoor unit's flare and the valve rods.
After the check is complete, wipe all soapy water off.
7
Disconnect the charging hose from the gas stop valve's service
port, then fully open the liquid and gas stop valves.
Do not attempt to turn the valve rod beyond its stop.
8
Tighten the valve lids and service port caps for the liquid and
gas stop valves with a torque wrench at the specified torques.
See
"10.2. Connecting the refrigerant piping to the outdoor unit"
for details.
NOTICE
■
Make sure that the gas stop valve and liquid stop
valve are firmly closed before performing the leak test
or vacuum drying.
■
Use a vacuum pump for R410A exclusively. Using the
same vacuum pump for different refrigerants may
damage the vacuum pump or the unit.
WARNING
■
Do not mix any substance other than the specified
refrigerant (R410A) into the refrigeration cycle.
■
When refrigerant gas leaks occur, ventilate the room
as soon and as much as possible.
■
R410A, as well as other refrigerants, should always
be recovered and never be released directly into the
environment.
INFORMATION
Do not purge the air with refrigerants. Use a vacuum pump
to evacuate the installation.
Pipe length
≤≤≤≤
15 m
>
15 m
Run time
≥
10 minutes
≥
15 minutes
NOTICE
If the meter needle does go back, this may indicate
presence of moisture or leaking from connecting
parts. Repeat steps 2 through 4 after checking all
connecting parts and slightly loosening and
retightening the nuts.
1
4
10
2
6
5
3
7 8 9
8
Summary of Contents for ERHQ006BBV3
Page 19: ......