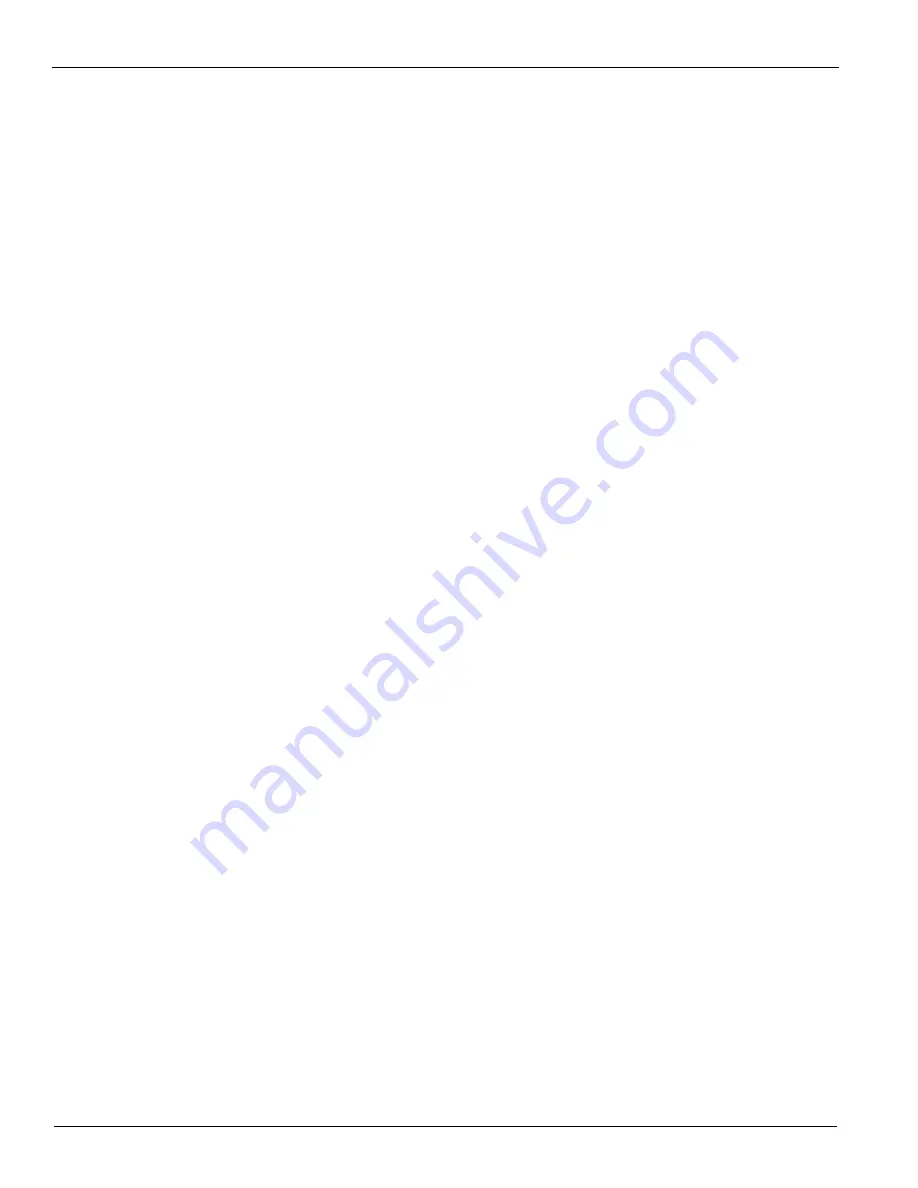
6
Daikin
IM 902
Installation
6
Connect the suction line and suction connection (Figure 4
on page 5).
7
Install the expansion valve (Figure 4 on page 5). Follow the
expansion valve manufacturer’s recommendations for
installation to avoid damaging the valve. If the valve is
externally equalized, use a tubing cutter to cut off the
plugged end of the factory installed equalizer line. Next,
use a de-burring tool to remove any loose metal from the
equalizer line (Figure 4 on page 5) and attach it to the
expansion valve. If the valve is internally equalized, the
factory installed equalizer line can be left as is or it can be
cut back and sealed.
8
The expansion valve’s remote sensing bulb (Figure 4 on
page 5) should be securely strapped to the horizontal run of
the suction line at the 3 or 9 o’clock position and insulated.
9
Connect the liquid line (Figure 4 on page 5) to the
expansion valve. Pressurize the coil, expansion valve
assembly and suction connection to 100 psig with dry
nitrogen or other suitable gas. The coil should be left
pressurized for a minimum of 10 minutes.
10
If the coil holds pressure, the hook-up can be considered
leak free. If the pressure drops by 5 psi or less, re-
pressurize the coil and wait another 10 minutes. If the
pressure drops again, there are more than likely one or
more small leaks, which should be located and repaired.
Pressure losses greater than 5 psi would indicate a larger
leak, which should be isolated and repaired. Be sure to
check valves and fittings as potential sites for leakage or
bleed. If the coil is found to be leaking, contact your local
Daikin
coil representative.
Note:
Unauthorized repair of the coil may void the coil’s
warranty (see the
Daikin
warranty policy on back
cover).
11
Use a vacuum pump to evacuate the coil and any
interconnecting piping that has been open to atmosphere.
Measure the vacuum in the piping using a micron gauge
located as far from the pump as possible (the vacuum at the
pump will be greater than the rest of the system). Evacuate
the coil to 500 microns or less then close the valve between
the pump and the system. If the vacuum holds to 500
microns or less for one minute, the system is ready to be
charged or refrigerant pumped down in another portion of
the system can be opened to the coil. A steady rise in
microns would indicate that moisture is still present and
that the coil should be further vacuumed until the moisture
has been removed.
12
Failure to obtain a high vacuum is indicative of a great deal
of moisture or a small leak. Break the vacuum with a
charge of dry nitrogen or other suitable gas and recheck for
leaks (soapy water works well). If no leaks are found,
continue vacuuming the coil until the desired vacuum is
reached.
13
All field piping must be self-supporting.