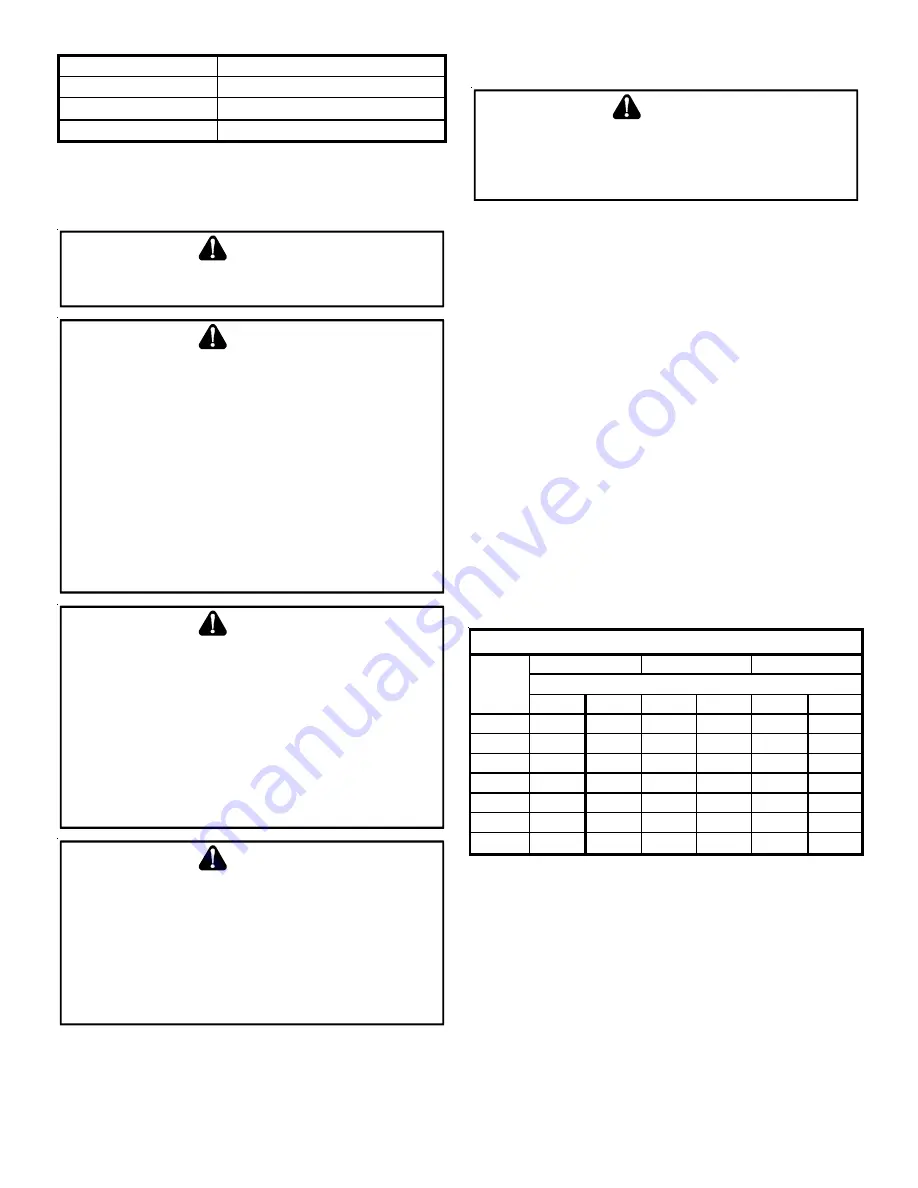
3
Design Temperature
Suggested Minimum Elevation
+15° and above
2 1/2"
-5° to +14°
8"
below -5°
12"
S
AFE
R
EFRIGERANT
H
ANDLING
While these items will not cover every conceivable situation, they
should serve as a useful guide.
T
O
AVOID
POSSIBLE
INJURY
,
EXPLOSION
OR
DEATH
,
PRACTICE
SAFE
HANDLING
OF
REFRIGERANTS
.
WARNING
R
EFRIGERANTS
ARE
HEAVIER
THAN
AIR
. T
HEY
CAN
“
PUSH
OUT
”
THE
OXYGEN
IN
YOUR
LUNGS
OR
IN
ANY
ENCLOSED
SPACE
. T
O
AVOID
POSSIBLE
DIFFICULTY
IN
BREATHING
OR
DEATH
:
• N
EVER
PURGE
REFRIGERANT
INTO
AN
ENCLOSED
ROOM
OR
SPACE
. B
Y
LAW
,
ALL
REFRIGERANTS
MUST
BE
RECLAIMED
.
• I
F
AN
INDOOR
LEAK
IS
SUSPECTED
,
THOROUGHLY
VENTILATE
THE
AREA
BEFORE
BEGINNING
WORK
.
• L
IQUID
REFRIGERANT
CAN
BE
VERY
COLD
. T
O
AVOID
POSSIBLE
FROST
BITE
OR
BLINDNESS
,
AVOID
CONTACT
AND
WEAR
GLOVES
AND
GOGGLES
. I
F
LIQUID
REFRIGERANT
DOES
CONTACT
YOUR
SKIN
OR
EYES
,
SEEK
MEDICAL
HELP
IMMEDIATELY
.
• A
LWAYS
FOLLOW
EPA
REGULATIONS
. N
EVER
BURN
REFRIGERANT
,
AS
P
OISONOUS
GAS
WILL
BE
PRODUCED
.
WARNING
T
O
AVOID
POSSIBLE
EXPLOSION
:
• N
EVER
APPLY
FLAME
OR
STEAM
TO
A
REFRIGERANT
CYLINDER
. I
F
YOU
MUST
HEAT
A
CYLINDER
FOR
FASTER
CHARGING
,
PARTIALLY
IMMERSE
IT
IN
WARM
WATER
.
• N
EVER
FILL
A
CYLINDER
MORE
THAN
80%
FULL
OF
LIQUID
REFRIGERANT
.
• N
EVER
ADD
ANYTHING
OTHER
THAN
R-22
TO
AN
R-22
CYLINDER
OR
R-
410A
TO
AN
R-410A
CYLINDER
. T
HE
SERVICE
EQUIPMENT
USED
MUST
BE
LISTED
OR
CERTIFIED
FOR
THE
TYPE
OF
REFRIGERANT
USED
.
• S
TORE
CYLINDERS
IN
A
COOL
,
DRY
PLACE
. N
EVER
USE
A
CYLINDER
AS
A
P
LATFORM
OR
A
ROLLER
.
WARNING
T
O
AVOID
POSSIBLE
EXPLOSION
,
USE
ONLY
RETURNABLE
(
NOT
DISPOSABLE
)
SERVICE
CYLINDERS
WHEN
REMOVING
REFRIGERANT
FROM
A
SYSTEM
.
• E
NSURE
THE
CYLINDER
IS
FREE
OF
DAMAGE
WHICH
COULD
LEAD
TO
A
LEAK
OR
EXPLOSION
.
• E
NSURE
THE
HYDROSTATIC
TEST
DATE
DOES
NOT
EXCEED
5
YEARS
.
• E
NSURE
THE
PRESSURE
RATING
MEETS
OR
EXCEEDS
400
PSIG
.
W
HEN
IN
DOUBT
,
DO
NOT
USE
CYLINDER
.
WARNING
R
EFRIGERANT
L
INES
T
HE
COMPRESSOR
POE
OIL
FOR
R-410A
UNITS
IS
EXTREMELY
SUSCEPTIBLE
TO
MOISTURE
ABSORPTION
AND
COULD
CAUSE
COMPRESSOR
FAILURE
. D
O
NOT
LEAVE
SYSTEM
OPEN
TO
ATMOSPHERE
ANY
LONGER
THAN
NECESSARY
FOR
INSTALLATION
.
CAUTION
Use only refrigerant grade (dehydrated and sealed) copper tubing
to connect the condensing unit with the indoor evaporator. After
cutting the tubing, install plugs to keep refrigerant tubing clean
and dry prior to and during installation. Tubing should always be
cut square keeping ends round and free from burrs. Clean the
tubing to prevent contamination.
Do NOT let refrigerant lines come in direct contact with plumbing,
ductwork, floor joists, wall studs, floors, and walls. When run-
ning refrigerant lines through a foundation or wall, openings
should allow for sound and vibration absorbing material to be
placed or installed between tubing and foundation. Any gap be-
tween foundation or wall and refrigerant lines should be filled
with a pliable silicon-based caulk, RTV or a vibration damping
material. Avoid suspending refrigerant tubing from joists and studs
with rigid wire or straps that would come in contact with the
tubing. Use an insulated or suspension type hanger. Keep both
lines separate and always insulate the suction line.
These sizes are suitable for line lengths of 79 feet or less. If a run
of more than eighty feet is required, refer to Remote Cooling Ser-
vice Manual, or TP-106 Long Line Set Application R-22, or TP-107
Long Line Set Application R-410A or contact your distributor for
assistance.
Cond
Unit
Tons
Suct
Liq
Suct
Liq
Suct
Liq
1 1/2
5/8
1/4
3/4
3/8
3/4
3/8
2
5/8
1/4
3/4
3/8
3/4
3/8
2 1/2
5/8
1/4
3/4
3/8
7/8
3/8
3
3/4
3/8
7/8
3/8
1 1/8
3/8
3 1/2
7/8
3/8
1 1/8
3/8
1 1/8
3/8
4
7/8
3/8
1 1/8
3/8
1 1/8
3/8
5
7/8
3/8
1 1/8
3/8
1 1/8
3/8
Line Diameter (In. OD)
RECOMMENDED INTERCONNECTING TUBING (Ft)
0-24
25-49
50-79*
* Lines greater than 79 feet in length or vertical elevation changes more
than 50 feet
refer to the Remote Cooling Service Manual or contact your
distributor for assistance.
Insulation is necessary to prevent condensation from forming
and dropping from the suction line. Armaflex (or satisfactory
equivalent) with 3/8” min. wall thickness is recommended. In
severe conditions (hot, high humidity areas) 1/2” insulation may
be required. Insulation must be installed in a manner which
protects tubing from damage and contamination.
Where possible, drain as much residual compressor oil from ex-
isting systems, lines, and traps; pay close attention to low areas
where oil may collect.
NOTE:
If changing refrigerant types, ensure
the indoor coil and metering device is compatible with the type of
refrigerant being used; otherwise, the indoor coil must be replaced.