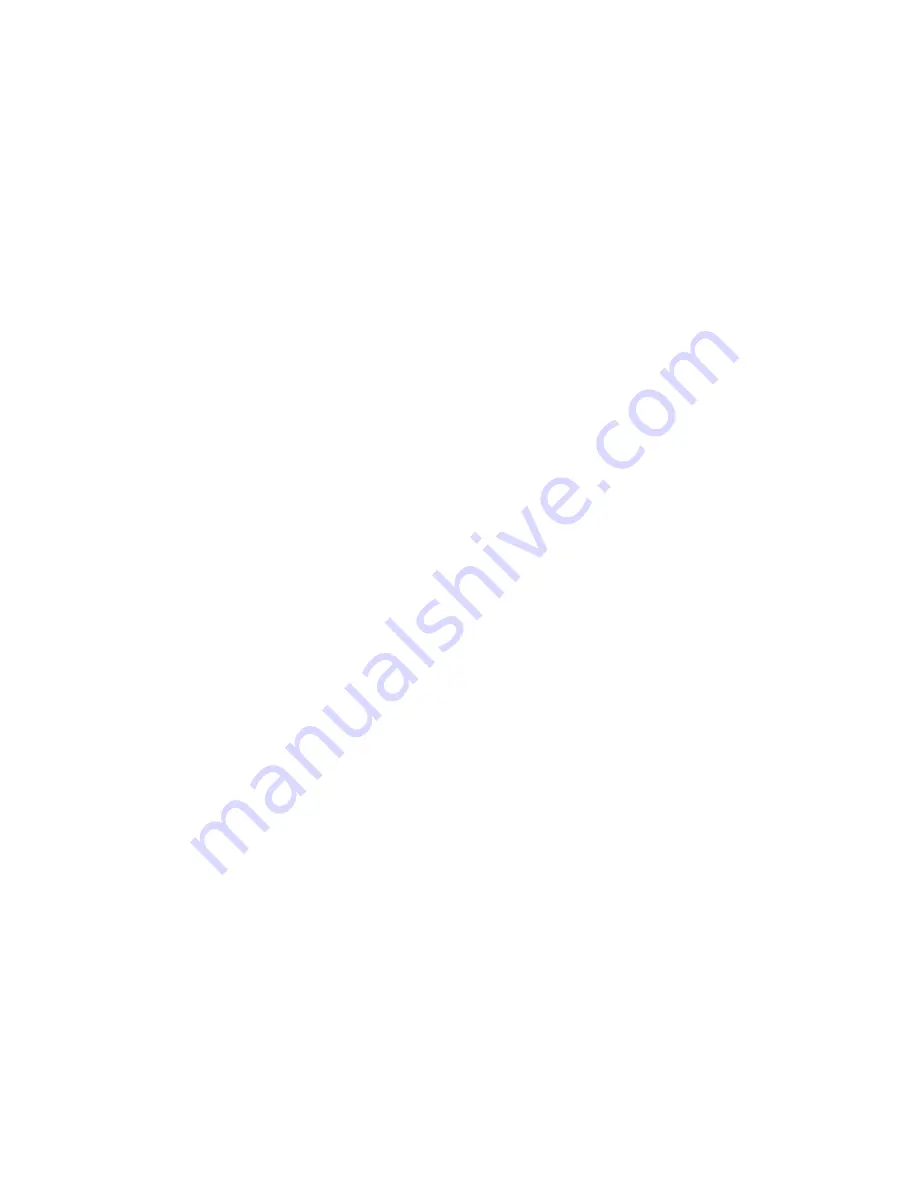
8
3. Check subcooling and superheat. Systems with TXV
application should have a subcooling of 6°F +/- 1°F and
superheat of 8°F +/- 1°F.
a.
If subcooling and superheat are low,
adjust
TXV to
8°F +/- 1°F superheat, then check subcooling.
NOTE:
To adjust superheat, turn the valve stem clock-
wise to increase and counter clockwise to decrease.
b.
If subcooling is low and superheat is high,
add
charge
to raise subcooling to 6°F+/-1°F then check superheat.
c.
If subcooling and superheat are high,
adjust
TXV valve
to 8°F +/- 1°F superheat, then check subcooling.
d.
If subcooling is high and superheat is low,
adjust
TXV
valve to 8°F +/- 1°F. superheat and
remove
charge to
lower the subcooling to 6°F +/- 1°F.
NOTE:
Do
NOT
adjust the charge based on suction pressure
unless there is a gross undercharge.
4. Disconnect manifold set, installation is complete.
SUBCOOLING FORMULA = SAT. LIQUID TEMP. - LIQUID LINE TEMP.
NOTE:
Check the Schrader ports for leaks and tighten valve cores
if necessary. Install caps finger-tight.
H
EAT
P
UMP
- H
EATING
C
YCLE
The proper method of charging a heat pump in the heat mode is by
weight with the additional charge adjustments for line size, line
length, and other system components. For best results on outdoor
units with TXVs, superheat should be 5°F +/- 1°F at 4-6" from the
compressor. Make final charge adjustments in the cooling cycle.
A
DDITIONAL
N
OTES
1. There are (3) 7-segment LED displays on the PCB. Refer to
the Troubleshooting chart at the end of this manual for
definitions of the LED status.
2. “TERM” dip switch is used for communications bus
configuration. Leave the settings to the factory default
position.
3. “LEARN” push button is used to reset the commnications
between the equipment. Used only for troubleshooting
purposes.
4. Press “TEST” push button, during system “Standby” mode
to turn on both the compressor and outdoor fan for five
seconds.
5. The “RECALL” push button is used to retrieve the six most
recent faults. The control must be in Standby Mode (no
thermostat inputs) to use the feature. Depress the push
button for approximately two seconds and less than five
seconds. The 7-segment LED displays will then display the
six most recent faults beginning with the most recent fault
and decrementing to the least recent fault. The faults may
be cleared by depressing the button for greater than five
seconds. Consecutively repeated faults are displayed a
maximum of three times. Refer to the fault code definitions
at the end of this manual for more details.
6. A forced defrost can be initiated by pressing “TEST” and
“RECALL” push buttons simultaneously for more than 1
second with a valid call for heat. The forced defrost can be
terminated by
•
A 10 minute lapse in time,
•
A coil temperature rise above 75°F or
•
By pressing the two buttons again for more than 1 sec-
ond.
C
OMFORT
N
ET
™ S
YSTEM
O
VERVIEW
The ComfortNet system is a system that includes a ComfortNet
compatible air handler/furnace/modular blower and air condi-
tioner or heat pump . Any other system configurations are consid-
ered invalid ComfortNet systems and must be connected as a tra-
ditional (or legacy) system.
A ComfortNet heating/air conditioning system differs from a legacy/
traditional system in the manner in which the indoor unit, out-
door unit and thermostat interact with one another. In a tradi-
tional system, the thermostat sends commands to the indoor and
outdoor units via analog 24 VAC signals. It is a one-way commu-
nication path in that the indoor and outdoor units typically do
not return information to the thermostat.
On the other hand, the indoor unit, and outdoor unit comprising a
ComfortNet system “communicate” digitally with one another. It
is now a two-way communications path. The thermostat still
sends commands to the indoor and outdoor units. However, the
indoor and outdoor units may also request and receive informa-
tion from one another to optimize system performance.
Two-way digital communications is accomplished using only two
wires between the indoor and outdoor units. The heat pump con-
trol board is powered by 24 VAC, which is supplied by the factory-
installed transformer in the heat pump control box. (If you are
attempting to install a CTK0* thermostat, installation
instructions can be found at www.comfortcontrols.com/#instal-
lation.)
A
IRFLOW
C
ONSIDERATION
Airflow demands are managed differently in a fully communicat-
ing system than they are in a legacy wired system. The system
operating mode (as determined by the thermostat) determines
which unit calculates the system airflow demand. If the indoor
unit is responsible for determining the airflow demand, it calcu-
lates the demand and sends it to the ECM motor. If the outdoor
unit or thermostat is responsible for determining the demand, it
calculates the demand and transmits the demand along with a
fan request to the indoor unit. The indoor unit then sends the
demand to the ECM motor. The table below lists the various
ComfortNet systems, the operating mode, and airflow demand
source.