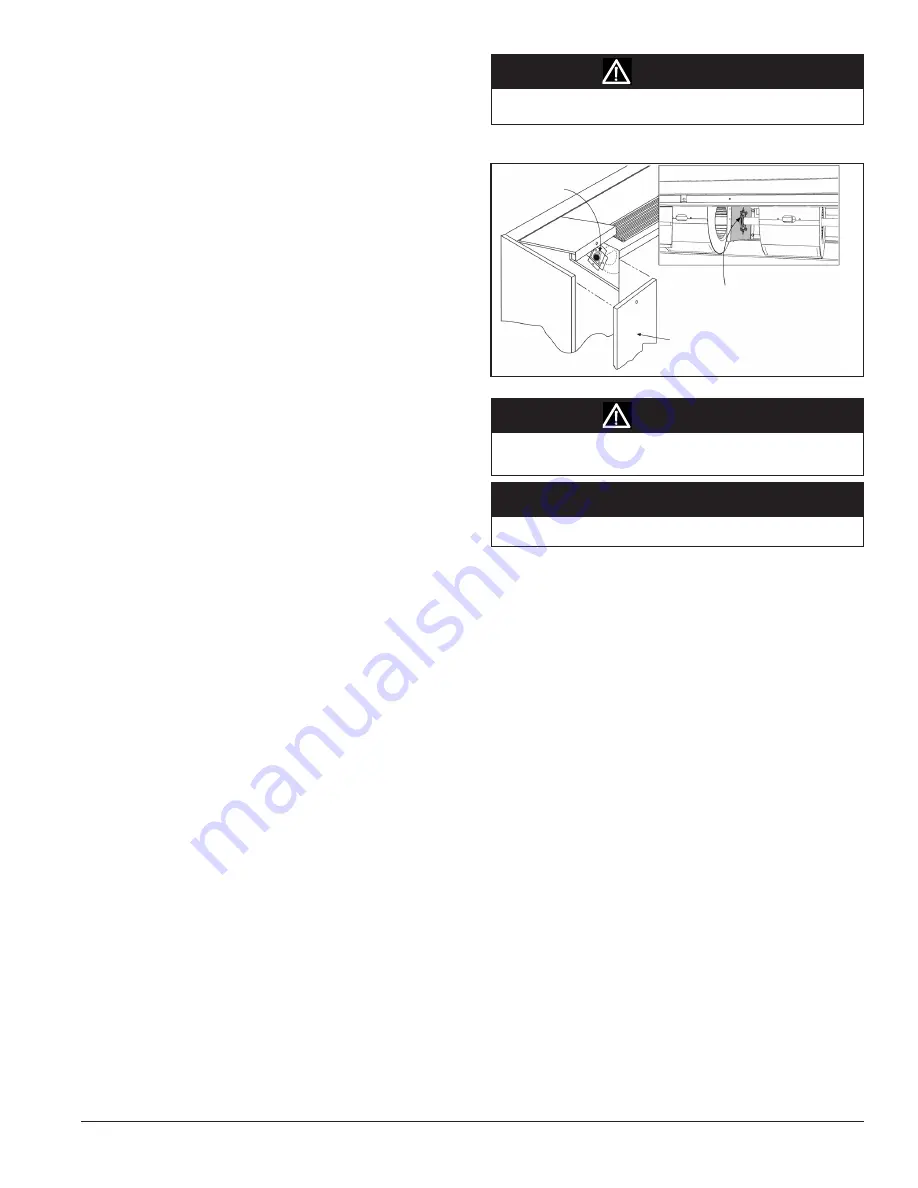
IM 1083
Self-Contained WSHP Unit Ventilator Models ARQ, ERQ, GRQ
Page 39 of 42
Figure 74: Fan Shaft Bearing(s) Oil Cup Location(s)
Room Air Fan
Shaft Bearing
Left Front Access Panel
Prepare Unit Ventilator for Start-up
Post Installation Checklist
□
Unit securely fastened to wall
□
Electrical hook-up complete; power, control, wall
thermostat (if applicable) in accordance with unit wiring
diagram(s)
□
Air filter clean and in place
□
All access and end panels in place and protective
covering removed
□
No debris, dust, dirt, or obstructions exist in front of
the return air intake grille at the floor
□
All installation work has been completed in
accordance with applicable local, state and national
codes
□
Room air fan shaft bearing oiled
□
Unit square and level and running smoothly and
quietly
□ No air infiltration
□
Paint nicks and scratches touched up (as required)
□
Access space provided for maintenance, service and
unit removal
□ Shipping carton replaced over unit for protection
□
Owner or maintenance personnel provided with a
copy of this manual and other manuals/documents
shipped with the unit.
□ Owner or maintenance personnel instructed on
proper operation and maintenance
Oiling
Do not attempt to operate the unit fans until the room air fan shaft
bearing has been oiled.
Access to fan shaft bearing is through left top access door. Use a high
grade SAE 20 or 30 nondetergent mineral oil. A few drops are sufficient.
Do not over oil.
Refer to Figure 74 for the oil point.
Note:
Unit size 048 has a fan shaft bearing located between the first
and second fan from the unit left end that is required to be oiled.
Filter(s)
AAF
®
-HermanNelson
®
single-use filters are standard on all units.
Permanent wire mesh and renewable media filters are available in lieu
of single-use filters.
• Single-use filters feature Amerglas media. They are designed to be
used once and discarded.
• Permanent filters are metal filters that may be removed for cleaning
and reused numerous times.
• Renewable media filters (figure 75) consist of a heavy painted metal
structural frame and renewable Amerglas media.
Turn off unit before servicing to avoid danger of injury from
rotating fans.
WARNING
Motor manufacturer recommends not oiling the room fan motor.
NOTICE
When oiling the middle fan shaft bearing DO NOT allow oil to
drip down on the components located below the bearing.
CAUTION
Unit Size 048 Bearing, Located
Between First and Second
Fan from Left End of Unit
Summary of Contents for ARQ
Page 2: ......