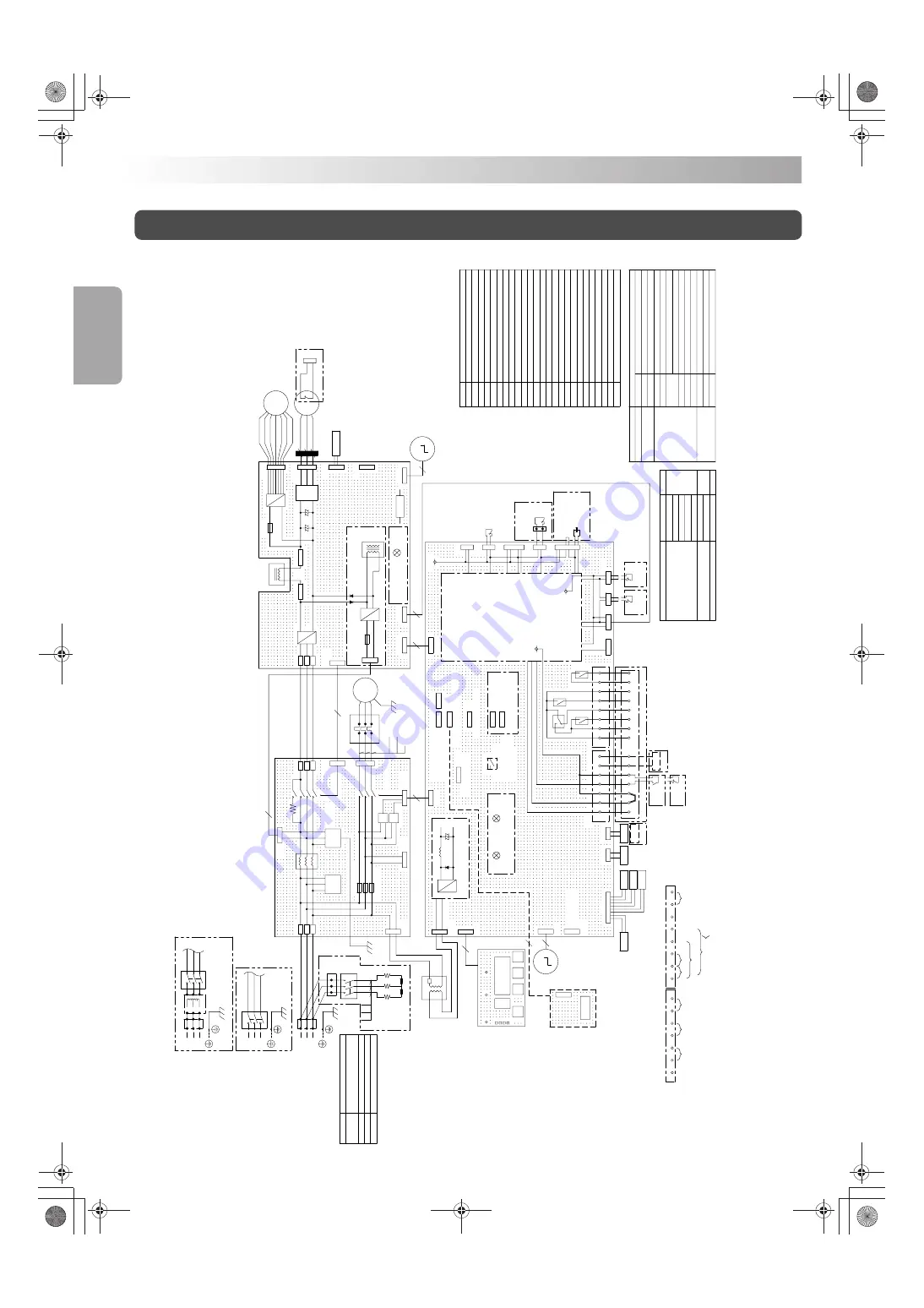
12
Electric wiring diagram (Typical: AKZ329)
A5P
Additional par
t symbol
Model
Expansion board f
or comm
unication with main machine
Th-9
AKZ9-OP-CS
AKZ9-OP-Y10
AKZ9-OP-Y5
Th-1
Oil temper
ature control ther
mistor
AKZ9-OP-A10
AKZ9-OP-A5
AKZ9-OP-K10
A5P
AKZ9-OP-K5
Machine temper
ature tuning ther
mistor
-047, -048 model only
X3M
Th-1
31
30
13
12
11
10
9
67
66
65
64
63
62
61
60
X3M, X4M
S4T
E1H
"-H" model only
X4M 24
23
S4T
T1R
t˚
"-B" model
MCCB
L2
L3
L1
K2M
MCCB
Circuit breaker
Compressor protection thermostat
High-pressure pressure switch
Temperature fuse
Heater
Magnetic contactor
Magnetic contactor coil
Overheat preventive temperature switch
Oil lack preventive pressure switch
Terminal block
Circuit breaker
Trans
Terminal block
MCCB
-H (Buit-in heater)
-047, -048
-C (CE model)
-B (Built-in break
er model)
(Diff
erent-v
oltage
model)
Men
u model
Standard, -046 (Diff
erent-v
oltage model)
COR
67
66
65
64
63
62
61
60
Th-6
Th-7
Th-8
S9
T1R
Th-Fin
S3PH
S151
S150
CE model only
Hv
Hu
Vcc
GND
W
V
U
θ
S2T
S172
X2M
9
Alar
m and r
un signals
31
30
13
12
11
10
A4P
Y1E, Y2E
X1M, X2M
Th300
Th-9
Th-6
Th-7
Th-8
Th-1
Th-4
Th-3
DCL
DCL
6.3A 250V
LED300
CN103
-
~
X2M
A4P
A3P
A2P
A1P
Comm
unication
–
~
–
+
Th300
Th-Fin
Y1E
Y2E
M2C
M3F
M
IC600
–
+
–
~
CN650
X500
M1P
DC
M
3~
M
3~
M
CN14
S0
S160
S90
LED_A
LED140
S10
CN12
Optional par
ts
Th-2
M2C
M3F
S2T
CN, S, X
K1S
M1P
FU
A3P
C
A2P
Alar
m output
ACDC
θ
S2T
S3PH
S172
S171
S170
S179
95
96
K1S
A1P
Th-9
S60
+12V
S140
+12V
+15VE
CN2
S183
S184
S182
S185
31
30
13
12
11
10
9
67
66
65
64
63
62
61
L1
Th-2
Th-3
Th-4
CN11
CN10
S80
S200
CN7
CN6
CN110
CN20
CN18
+
–
C551
C550
CN15
–
+
3.15A 250V
FU550
DCL2
DCL1
FU650
3.15A 250V
U1
V1
W1
K1S
T3
T2
T1
L3
L2
60
X530
X510
X520
X519
X501
FU513
FU512
FU511
R
S
T
SA
SA
L3
L2
L1
N=4
X1M
Optional par
ts
S130
CN600
R
S
T
X3M
ST
R
K2M
W2
V2
U2
Black
Black
Black
E1H
F1UT
F2UT
K2M
t˚
t˚
M
5
6
3
2
6
5
2
S5P
F1UT, F2UT
24
4
S5P
X3M
L2
L3
L1
Tr
~
–
Power supply
3~ 200/200·220V 50/60Hz
Standard,
-C,
-B, -T, -H
-046
-047
-048
3~ 220·230V 50/60Hz
3~ 380·400·415V 50/60Hz
3~ 440·460·480V 50/60Hz
Model
Power supply
MR52Pa
MR30Y
MR30X
MR30W
AKZ9-OP-K15
COR
X3M
L2
L3
L1
Tr
Input
Output
0V
MCCB
-047, -048 model only
Black (Red)
Black (White)
Black
Shor
t-circuit bar
Black (Red)
Black (White)
Black
Black (Red)
Black (White)
Black
"-H" model only
Red
Red
Blac
k
Blac
k
Remote
control
Optional
protectiv
e
de
vice
F
or connection
of machine
temper
ature
tuning
ther
mistor
Alar
m le
v
el output
Alar
m/po
w
er f
ailure
Nor
mal pump r
un
OFF
:Le
v
el1
ON :Le
v
el2
W
ar
ning output
Optional par
ts
Optional par
ts
"-H" model only
Note) 1.
T
o use optional oil temper
ature control ther
mistor (Th-9), substitute it
for the outlet oil temper
ature ther
mistor (Th-2) on CN11.
2.
F
or details
, ref
er to the electr
ic wir
ing diag
ram f
or each model.
CE model only
CE model only
Shor
t-circuit
bar
Shor
t-circuit
bar
Magnetic
contactor coil
"-H" model only
Yello
w
Red
White
Blac
k
Bro
wn
Or
ange
Blue
Red
Y
ello
w
Blue
In
ver
ter CPU nor
mal
P
o
w
er supply circuit
Blac
k
Blac
k
Blac
k
Surge absorber
RELA
Y control
Blac
k (Red)
Blac
k (White)
Blac
k
Photocoupler
RELA
Y control
Base
comm
unication
Control CPU
nor
mal
P
o
w
er supply circuit
Expansion
user I/O
F
or
comm
unication
(par
allel)
F
or ser
ial comm
unication
Analog monitor
PR
O
TECT SW
(erroneous oper
ation
pre
vention)
F
or shipping adjustment
High-precision
analog input
Protection de
vice
input circuit
Optional par
ts
P
ar
t type
T
ype
Name
Control board
In
v
er
ter board
Noise filter board
Displa
y board
Condenser
Connector
F
err
ite Core
Reactor
Fuse
Ov
er-current rela
y
Mor
tor (pump)
Mor
tor (compressor)
Mor
tor (f
an)
Machine temper
ature tuning ther
mistor (Optional)
Outlet oil temper
ature ther
mistor
Air (room temper
ature) ther
mistor
Inlet oil temper
ature ther
mistor
Exhaust gas temper
ature ther
mistor
Condenser temper
ature ther
mistor
EV v
alv
e outlet temper
ature ther
mistor
Oil temper
ature ther
mistor (Optional)
Fin temper
ature ther
mistor
Control bo
x temper
ature ther
mistor
T
rans
T
er
minal b
loc
k
Electr
ic e
xpansion v
alv
e
Installation
Installation
Pr
ocedure
PIM00318A_EN.fm Page 12 Tuesday, October 26, 2010 12:37 PM