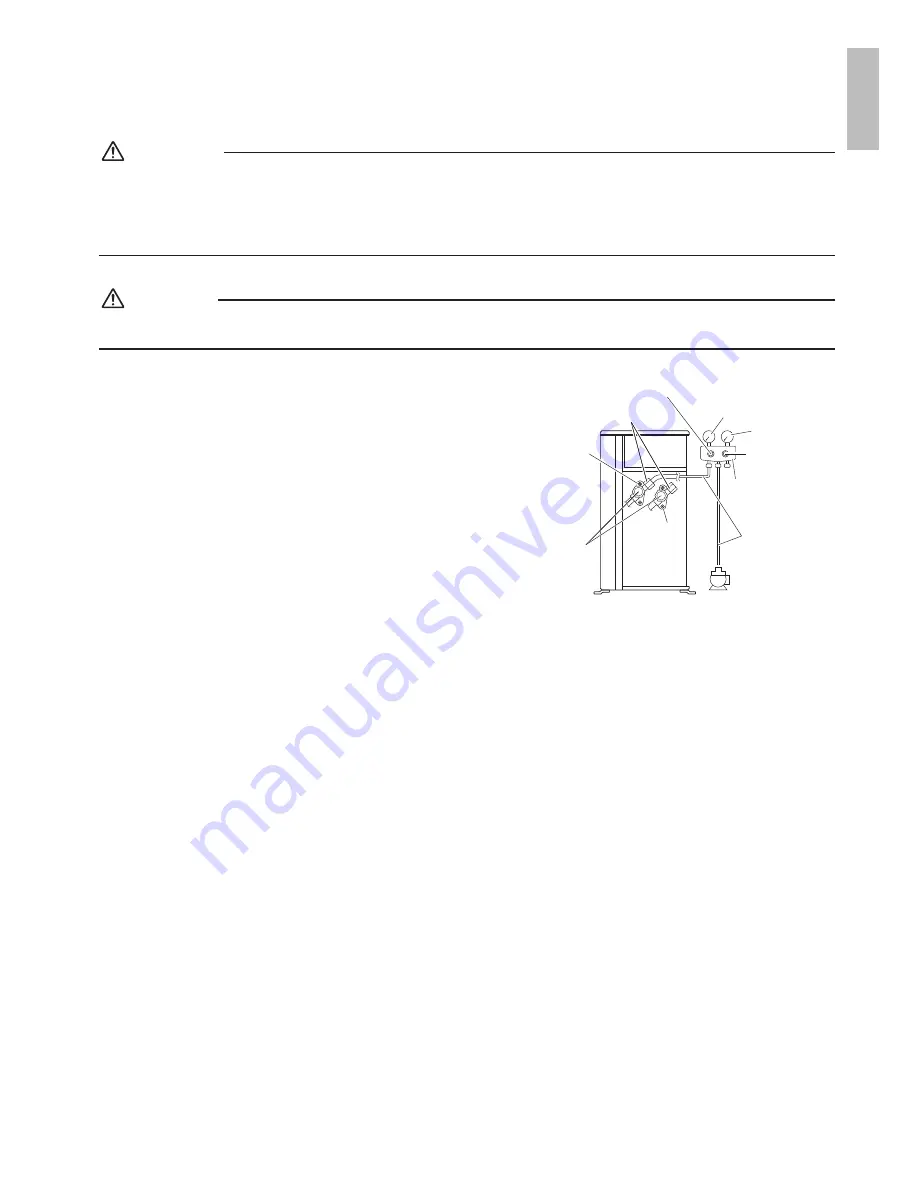
10
■
English
5.
Pressure test and evacuating system
WARNING
•
Make sure that air or any matter other than refrigerant (R410A) does not get into the refrigeration cycle.
•
If refrigerant gas leaks should occur, ventilate the room as soon and as much as possible.
•
R410A, as well as other refrigerants, should always be recovered and never be released directly into the environment.
• Use a vacuum pump for R410A exclusively. Using the same vacuum pump for different refrigerants may damage the vacuum
pump or the unit.
CAUTION
It is highly recommended that you do not open/close the stop valves when the outdoor temperature is below −5°F (−21°C) as
this may result in refrigerant leakage.
•
When piping work is complete, it is necessary to perform a pressure test
and evacuate system with a vacuum pump.
•
If using additional refrigerant, perform air purging from the refrigerant
pipes and indoor unit using a vacuum pump, then charge additional
refrigerant.
• Use a hexagonal wrench (3/16 inch (4mm)) to operate the stop valve rods
.
•
All refrigerant pipe joints should be tightened with a torque wrench to the
specified tightening torque.
Compound
pressure gauge
Pressure meter
High-pressure
valve
Low-pressure valve
Vacuum
pump
Gas
stop
valve
Charging
hoses
Gauge
manifold
Service port
Liquid
stop
valve
Valve
caps
1) Pressurize the liquid pipe and gas pipe from the service ports of each stop valve to 550psi (3.8MPa) (do not pressurize
more than 550psi (3.8MPa)) for 1 hour minimum, 24 hours recommended. If there is a pressure drop, check for leaks,
make repairs and perform the pressure test again.
2) Connect the gauge manifold’s charging hose to the gas stop valve’s service port.
3) Fully open the low-pressure valve (Lo) on the gauge manifold and fully close the high-pressure valve (Hi).
(High-pressure valve will require no further operation.)
4)
Evacuate system using vacuum pump to below 500 microns for 1 hour minimum.
5) Close the low-pressure valve (Lo) on the gauge manifold and stop vacuum pump.
(Maintain this condition for 4-5 minutes to make sure that the compound pressure gauge pointer does not swing back.)*
1
6) Remove the valve caps from the liquid stop value and gas stop valve.
7)
To open the liquid stop valve, turn the rod of the valve 90° counter-clockwise using a hexagonal wrench.
Close it after 5 seconds, and check for gas leakage.
Using soapy water, check for gas leakage from the indoor unit’s flare and outdoor unit’s flare and valve rods.
After the check is complete, wipe all soapy water off.
8) Disconnect the charging hoses from the service port for the gas stop valve, then fully open the liquid and gas stop valves.
(Do not attempt to turn the valve rods further than they can go.)
9)
Tighten the valve caps and service port caps for the liquid and gas stop valves with a torque wrench to the specified
torques.
Refer to
“4. Refrigerant piping”
on page 9 for details.
*
1
If the compound pressure gauge pointer swings back, the refrigerant may have water content or there may be a loose
pipe joint.
Check all pipe joints and retighten nuts as needed, then repeat steps 3) through 5).
English
01_EN_3P537039-1.indd 10
9/12/2018 7:37:44 PM