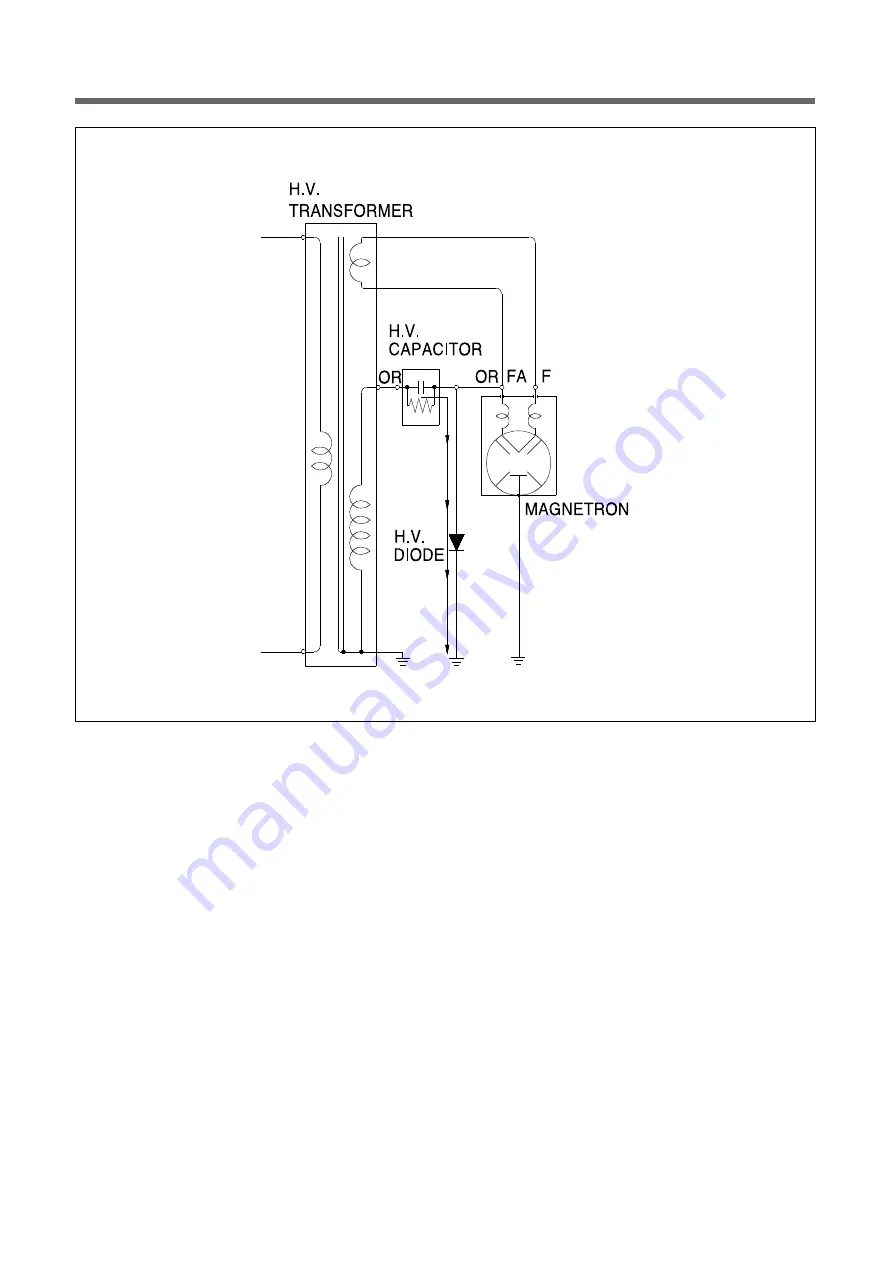
43
The Touch control circuit controls the ON-OFF time of RELAY 1 in order to vary the output power of the microwave oven
from power level 1 to HI (100%) power.
One complete ON and OFF cycle of the RELAY 1 is 29 seconds. The relation between indications on the control panel
and the output of the microwave oven is as shown.
AUTO DEFROST CYCLE
When auto defrost is selected and the desired defrosting time is chosen, the automatic cycle divides the defrosting time
into 5 periods of alternating defrost and stand times, by cycling on and off.
4. When the door is opened during cooking.
1) The primary interlock switch is opened to cut off primary voltage to the high voltage transformer to stop microwave
oscillation.
2) The secondary interlock switch is opened to give the door open information to touch control circuit. The contacts of
the RELAY 1,5 and 6 open, the display stops counting down.
Summary of Contents for KOT-170S0A
Page 8: ...7 FIG 1...
Page 22: ...21 FIG 13 1 FIG 13 2...
Page 42: ...41 WIRING DIAGRAM 1 WIRING DIAGRAM...
Page 56: ...55 3 PRINTED CIRCUIT BOARD FILM MP1 MP3 MP2...
Page 57: ...56...
Page 58: ...57 4 PCB CIRCUIT DIAGRAM...
Page 66: ...65 3 TOTAL ASSEMBLY...