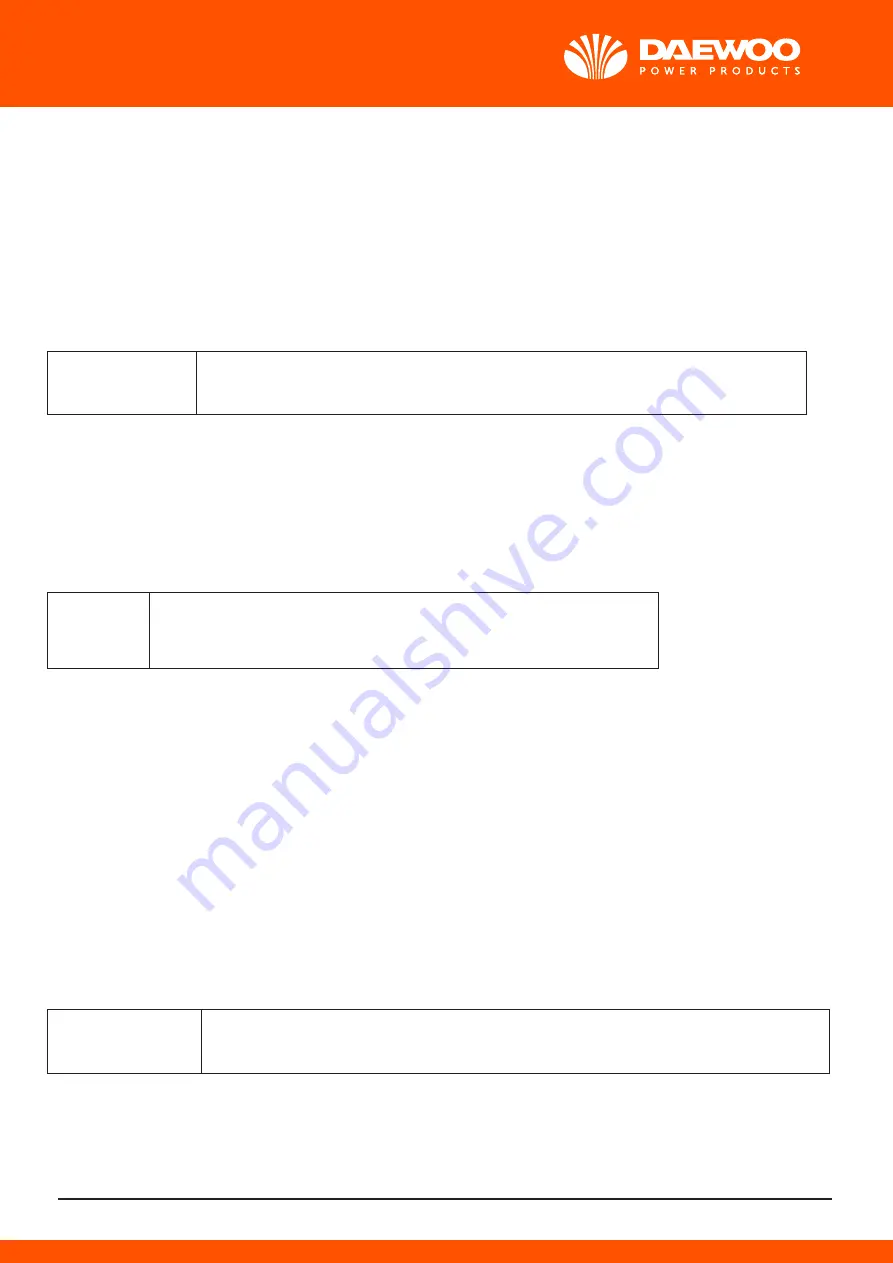
Blown Air Drying
Remove the covers from all apertures to allow the escape of the water-laden air. During drying,
air must be able to flow freely through the generator in order to carry off the moisture.
Direct hot air from two electrical fan heaters of around 1-3 KW into the generator air inlet aper-
tures. Ensure the heat source is at least 300mm away from the windings to avoid over heating
and damage to the insulation.
Apply the heat and plot the insulation value at half hourly intervals. The process is complete
when the parameters covered in the section entitled, 'Typical Drying Out Curve', are met.
Remove the heaters, replace all covers and re-commission as appropriate.
If the set is not to be run immediately ensure that the anticondensation heaters are energized,
and retest prior to running.
Shirt Circuit Method
NOTE: This process shou ld only be performed by a competent engineer familiar with safe
operating practices within and around generator sets of the type in question. Ensure the gene-
rator is safe to work on, initiate all mechanical and electrical safety procedures pertaining to the
genset and the site.
Bolt a short ci rcuit of adequate current carrying capacity, across the main terminals of the
generator. The shorting link should be capable of taking full load current.
Disconnect the cables from terminals "X" and "XX" of the AVR.
Connect a variable de supply to the "X" (positive) and "XX" (negative) field cables. The de
supply must be able to provide a current up to 2.0 Amp at 0-24Volts.
Position a suitable ac ammeter to measure the shorting link current.
Set the de supply voltage to zero and start the generating set. Slowly increase the de voltage to
pass current through the exciter field winding. As the excitation current increases, so the stator
current in the shorting link will increase. This stator output current level must be monitored, and
not allowed to exceed 80% of the generators rated output current.
After every 30 minutes of this exercise: Stop the generator and switch off the separate excita-
tion supply, and measure and record the stator winding IR values, and plot the results.
The resulting graph should be compared with the classic shaped graph. This drying out proce-
dure is complete when the parameters covered in the section entitled 'Typical Drying Out
Curve' are met.
Once the insulation Resistance is raised to an acceptable level minimum value 10MΩ - the de
supply may be removed and the exciter field leads "X" and "XX" re-connected to their terminals
on the AVR.
Rebuild the genset, replace all covers and re-commission as appropriate.
If the set is not to be run immediately ensure that the anticondensation heaters are energised,
and retest the generator prior to running.
Typical Drying Out Curve
Whichever method is used to dry out the generator the resistance should be measured every
half-hour and a curve plotted as shown.(Fig 9)
The illustration shows a typical curve for a machine that has absorbed a considerable amount
of moisture. The curve indicates a temporary increase in resistance, a fall and then a gradual
rise to a steady state. Point 'A', the steady state, must be greater than 1.0MΩ (If the windings
are only slightly damp the dotted portion of the curve may not appear).
For general guidance expect that the typical time to reach point 'A' will be approximately 3
hours for a LV 6 generator.
Drying should be continued after point "A" has been reached for at least one hour.
It should be noted that as winding temperature increases, values of insulation resistance may
significantly reduce. Therefore, the reference values for insulation resistance can only be esta-
blished with windings at a temperature of approximately 20°C.
After drying out, the insulation resistances should be rechecked to verify minimum resistances
quoted above are achieved. On re-testing it is recommended that the main stator insulation
resistance is checked as fol lows:
-Separate the neutral leads.
Ground V and W phase and megger U phase to ground
Ground U and W phase and megger V phase to ground
Ground U and V phase and megger W phase to ground.
If the minimum value of 1.0MΩ is not obtained, drying out must be continued and the test
repeated.
If the minimum value of 1.0MΩ for all components cannot be achieved rewinding or refurbish-
ment of the generator will be necessary.
The generator must not be put into service until the minimum value, Of 1.0MΩ for all compo-
nents, can be achieved.
8.2 BEARINGS
All bearings are supplied from the factory pre-packed with Kluber Asonic GHY 72 grease.
Do not mix kluber Asonic GHY 72 with any grease of different specifications. Mixing grease of
differing specifications will reduce bearing life. The specification for Kluber Asonic FHY 72 is
available on request from the factory.
Sealed for life bearings are fitted with integral seals and are not re-greasable.
BEARING LIFE
IMPORTANT!
The life of a bearing in service is subject to the working conditions and the
environment.
IMPORTANT!
High levels of vibration from the engine or misalignment of the set will
stress the bearing and reduce its service life. If the vibration limits set out
im BS 5000-3 and ISO 8528-9 are exceeded bearing life will be reduced.
Refer to 'vibration’ below.
IMPORTANT!
Long stationary periods in an environment where the generator is subject
to vibration can cause false brinneling, which puts flats on the ball and
grooves on the races, leading to premature failure.
IMPORTANT!
Very humid atmospheric or wet conditions can emulsify the grease causing
corrosion and deterioration of the grease, leading to premature failure of
the
bearings.
HEALTH MONLTORING OF THE BEARINGS
It recommends that the user check the bearing condition, using monitoring equipment, to
determine the state of the bearings. The 'best practice' is to take initial readings as a base line
and periodically monitor the bearings to detect a deteriorating trend. It will then be possible to
plan a bearing change at an appropriate generating set or engine service interval.
VLBRATION
The generators are designed ti withstand the vibration levels encountered on generating sets
built to meet the requirements of ISO 8528-9 and BS5000-3. (Where ISO 8528 is taken to be
broad band measurements and BS5000 refers to the predominant frequency of any vibrations
on the generating set.)
Definition of BSS000-3
Generators shall be capable of continuously withstanding linear vibration levels with amplitudes
of 0.25 mm between 5 Hz and velocities of 9.0 mm/s. Between 8 Hz and 200 Hz when measu-
red at any point directly on the carcass or main frame of the machine. These limits refer Only to
the predominant frequency of v ibration of any complex waveform.
Definition of ISO 8528-9
ISO 8528-9 refers to a broad band of frequencies, the broad band is taken to be between 2
Hertz and 300 Hertz. The table below is an example from ISO 8528-9 (value 1 ). This simplified
table lists the vibration limits by kVA range and speed for acceptable genset operation.
IMPORTANT!
Exceeding either o f the above specifications will have a detrimental effect
on the life of the bearing. This will invalidate the generator warranty. If you
are in any doubt, contact Newage International limited.
If the vibration levels of the generating set are not within the parameters quoted above.
1. consult the genset builder. The genset builder should address the genset design to reduce
the vibration levels as much ad possible.
2. Discuss the impact of not meeting the above levels on both bearing and generator life
expectancy.
Where requested, or deemed necessary, Newage will work with the genset builder in an
attempt to find a satisfactory solution.
BEARING 'SERVICELIFE' EXPECTANCY
Bearing manufacturers recognize that the "service life" of their bearings is dependent upon
many factors that are not in their control, they cannot therefore quote a "service life".
Although "service life" cannot be guaranteed, it can be maximized by attention to the genera-
ting set design. An understanding of the genset application will also help the user to maximize
the service life expectancy of the bearings. Particular attention should be paid to the alignment,
reduction of vibration levels, environmental protection, maintenance and monitoring procedu-
res. We does not quote life expectancy figures for bearings, but suggests practicable replace-
ment intervals based on the L 10 life of the bearing, the grease and the recommendations of
the bearing and grease manufacturers. For general-purpose applications, provid ing the vibra-
tion levels do not exceed the levels stated in ISO8528-9* and BS5000-3* and the ambient
temperature does not exceed 50°C the following approximations can be applied when *
(See section on vibration)
Sealed for life Bearings. - Approximately 30,000hours.
Re-greaseable bearings.- Approximately 40,000hours.
This is provided the correct maintenance is carried out, and only Kluber Asonic GHY 72 grease
(or equivalent) is used in all bearings. It is important to note that bearings in service. Under
good operating conditions, can continue to run beyond the remembered re placement period.
It should also be remembered that the r isk of bearing failure increases with time.
8.3 ALR FILTERS
Air filters for the removal of airborne particulate matter (dus) are offered as an addition to the
standard build option. Filters on it's need to be ordered with the generator. Air filters need to
be charged with oil before the genset is put to work (see 8.3.2) The frequency of fi lter mainte-
nance will depend upon the severity of the site conditions. Regular inspection of the elements
will be required to establish when cleaning is necessary.
Danger!
Removal of filter elements enables access to LIVE parts. Only remove elements
with the generator out of service.
8.3.1 CLEANING PROCEDURE
Remove the filter elements from the filter frames. Immerse of flush the element with a suitable
degreasing agent until the element is cleas.
As an alternative procedure a high-pressure water hose with a flat nozzle can be used. Sweep
the water spray back and forth across the element from the clean side (fine mesh side of
element) holding the nozzle firm ly against the element surface. Cold water may be adequate
depending upon type of contamination although hot water is preferable.
The element can be inspected for cleanliness by looking through the filter towards the light.
When the roughly clean, no cloudy areas will be seen. Dry elements thoroughly before attemp-
ting to carry out the recharging procedure.
8.3.2 RECHARGING (GHARGING) AIR FILTERS
Charging is best done by totally immersing the dry element into a dip tank containing "Filterko-
te Type k" or commercial lubricating oil SAE 20/50. oils of higher or lower viscosity are not
recommended.
Allow elements to completely drain before refitting the elements into the frames and putting
into service.
8.4 FAULT FINDING
IMPORTANT!
Before commencing any faultfinding procedures, examine all wiring for
broken or loose connections.
Two types of AVR can be fitted to the WH generator. The Refer to the generator nameplate for
type of AVR fitted.
8.4.1 MX341 AVR, FAULT FINDING
8.5 SEPARATE EXCITATION TEST PROCEDURE
The generator windings, diode assembly and AVR can be checked using the appropriate
following sections.
8.5.1 GENERATOR WINDINGS, ROTATING DIODES and PERMANENT MAGNET GENERA-
TOR (PMG)
IMPORTANT!
The resistances quoted apply to a standard winding. For generators
having windings or voltages other than those specified refer to fac-
tory for details. Ensure all disconnected leads are isolated and free
from
earth.
IMPORTANT!
Incorrect speed setting will give proportional error in voltage out put.
Checking Generator Windings and Rotating Diodes
This procedure is carried out w ith lead X and XX disconnected at the AVR or transformer
control rectifier bridge and using a 12 volt d. c. Supply to leads X and XX.
Start the set and run at rated speed.
Measure the voltages at the main output terminals U, V and W. if voltages are balanced and
/-10% of the generator nomial voltage, refer to 7 .5.1.1.
Check voltages at AVR terminals 6, 7 and 8. These should be balanced and between 170-250
volts.
If voltages at main terminals are balanced but voltage at 6, 7
and 8 are unbalanced, check continuity of leads 6,7 and 8.
If voltages are unbalanced , refer to 7 .5.1.2.
8.5.1.1 BALANCED MAIN TERMINAL VOLTAGES
If all voltages are balanced within 1 % at the main terminals, it can be assumed that all exciter
windings, main windings and main rotating diodes are in good order ,and the fault is in the
AVR or transformer control. Refer to subsection 7 .3.2 for test procedure.
If voltages are balanced but low, there is a fault in the main excitation windings or rotating
diode assembly. proceed as follows to identity:-
Rectifier Diodes
The diodes on the main rectifier assembly can be checked with a multimeter. The flexible leads
connected to each diode should be disconnected at the terminal end, and the forward and
reverse resistance checked. A healthy diode will indicate a very high resistance ( infinity) in the
reverse direction, and a low resistance in the forward direction. A faulty diode will give a full
deflection reading in both directions with the test meter on the 10,000 ohms scale, or an
infinity reading in both directions. On an electronic digital meter a healthy diode will give a low
Blown Air Drying
Remove the covers from all apertures to allow the escape of the water-laden air. During drying,
air must be able to flow freely through the generator in order to carry off the moisture.
Direct hot air from two electrical fan heaters of around 1-3 KW into the generator air inlet aper-
tures. Ensure the heat source is at least 300mm away from the windings to avoid over heating
and damage to the insulation.
Apply the heat and plot the insulation value at half hourly intervals. The process is complete
when the parameters covered in the section entitled, 'Typical Drying Out Curve', are met.
Remove the heaters, replace all covers and re-commission as appropriate.
If the set is not to be run immediately ensure that the anticondensation heaters are energized,
and retest prior to running.
Shirt Circuit Method
NOTE: This process shou ld only be performed by a competent engineer familiar with safe
operating practices within and around generator sets of the type in question. Ensure the gene-
rator is safe to work on, initiate all mechanical and electrical safety procedures pertaining to the
genset and the site.
Bolt a short ci rcuit of adequate current carrying capacity, across the main terminals of the
generator. The shorting link should be capable of taking full load current.
Disconnect the cables from terminals "X" and "XX" of the AVR.
Connect a variable de supply to the "X" (positive) and "XX" (negative) field cables. The de
supply must be able to provide a current up to 2.0 Amp at 0-24Volts.
Position a suitable ac ammeter to measure the shorting link current.
Set the de supply voltage to zero and start the generating set. Slowly increase the de voltage to
pass current through the exciter field winding. As the excitation current increases, so the stator
current in the shorting link will increase. This stator output current level must be monitored, and
not allowed to exceed 80% of the generators rated output current.
After every 30 minutes of this exercise: Stop the generator and switch off the separate excita-
tion supply, and measure and record the stator winding IR values, and plot the results.
The resulting graph should be compared with the classic shaped graph. This drying out proce-
dure is complete when the parameters covered in the section entitled 'Typical Drying Out
Curve' are met.
Once the insulation Resistance is raised to an acceptable level minimum value 10MΩ - the de
supply may be removed and the exciter field leads "X" and "XX" re-connected to their terminals
on the AVR.
Rebuild the genset, replace all covers and re-commission as appropriate.
If the set is not to be run immediately ensure that the anticondensation heaters are energised,
and retest the generator prior to running.
Typical Drying Out Curve
Whichever method is used to dry out the generator the resistance should be measured every
half-hour and a curve plotted as shown.(Fig 9)
The illustration shows a typical curve for a machine that has absorbed a considerable amount
of moisture. The curve indicates a temporary increase in resistance, a fall and then a gradual
rise to a steady state. Point 'A', the steady state, must be greater than 1.0MΩ (If the windings
are only slightly damp the dotted portion of the curve may not appear).
For general guidance expect that the typical time to reach point 'A' will be approximately 3
hours for a LV 6 generator.
Drying should be continued after point "A" has been reached for at least one hour.
It should be noted that as winding temperature increases, values of insulation resistance may
significantly reduce. Therefore, the reference values for insulation resistance can only be esta-
blished with windings at a temperature of approximately 20°C.
After drying out, the insulation resistances should be rechecked to verify minimum resistances
quoted above are achieved. On re-testing it is recommended that the main stator insulation
resistance is checked as fol lows:
-Separate the neutral leads.
Ground V and W phase and megger U phase to ground
Ground U and W phase and megger V phase to ground
Ground U and V phase and megger W phase to ground.
If the minimum value of 1.0MΩ is not obtained, drying out must be continued and the test
repeated.
If the minimum value of 1.0MΩ for all components cannot be achieved rewinding or refurbish-
ment of the generator will be necessary.
The generator must not be put into service until the minimum value, Of 1.0MΩ for all compo-
nents, can be achieved.
8.2 BEARINGS
All bearings are supplied from the factory pre-packed with Kluber Asonic GHY 72 grease.
Do not mix kluber Asonic GHY 72 with any grease of different specifications. Mixing grease of
differing specifications will reduce bearing life. The specification for Kluber Asonic FHY 72 is
available on request from the factory.
Sealed for life bearings are fitted with integral seals and are not re-greasable.
BEARING LIFE
IMPORTANT!
The life of a bearing in service is subject to the working conditions and the
environment.
IMPORTANT!
High levels of vibration from the engine or misalignment of the set will
stress the bearing and reduce its service life. If the vibration limits set out
im BS 5000-3 and ISO 8528-9 are exceeded bearing life will be reduced.
Refer to 'vibration’ below.
IMPORTANT!
Long stationary periods in an environment where the generator is subject
to vibration can cause false brinneling, which puts flats on the ball and
grooves on the races, leading to premature failure.
IMPORTANT!
Very humid atmospheric or wet conditions can emulsify the grease causing
corrosion and deterioration of the grease, leading to premature failure of
the
bearings.
HEALTH MONLTORING OF THE BEARINGS
It recommends that the user check the bearing condition, using monitoring equipment, to
determine the state of the bearings. The 'best practice' is to take initial readings as a base line
and periodically monitor the bearings to detect a deteriorating trend. It will then be possible to
plan a bearing change at an appropriate generating set or engine service interval.
VLBRATION
The generators are designed ti withstand the vibration levels encountered on generating sets
built to meet the requirements of ISO 8528-9 and BS5000-3. (Where ISO 8528 is taken to be
broad band measurements and BS5000 refers to the predominant frequency of any vibrations
on the generating set.)
Definition of BSS000-3
Generators shall be capable of continuously withstanding linear vibration levels with amplitudes
of 0.25 mm between 5 Hz and velocities of 9.0 mm/s. Between 8 Hz and 200 Hz when measu-
red at any point directly on the carcass or main frame of the machine. These limits refer Only to
the predominant frequency of v ibration of any complex waveform.
Definition of ISO 8528-9
ISO 8528-9 refers to a broad band of frequencies, the broad band is taken to be between 2
Hertz and 300 Hertz. The table below is an example from ISO 8528-9 (value 1 ). This simplified
table lists the vibration limits by kVA range and speed for acceptable genset operation.
IMPORTANT!
Exceeding either o f the above specifications will have a detrimental effect
on the life of the bearing. This will invalidate the generator warranty. If you
are in any doubt, contact Newage International limited.
If the vibration levels of the generating set are not within the parameters quoted above.
1. consult the genset builder. The genset builder should address the genset design to reduce
the vibration levels as much ad possible.
2. Discuss the impact of not meeting the above levels on both bearing and generator life
expectancy.
Where requested, or deemed necessary, Newage will work with the genset builder in an
attempt to find a satisfactory solution.
BEARING 'SERVICELIFE' EXPECTANCY
Bearing manufacturers recognize that the "service life" of their bearings is dependent upon
many factors that are not in their control, they cannot therefore quote a "service life".
Although "service life" cannot be guaranteed, it can be maximized by attention to the genera-
ting set design. An understanding of the genset application will also help the user to maximize
the service life expectancy of the bearings. Particular attention should be paid to the alignment,
reduction of vibration levels, environmental protection, maintenance and monitoring procedu-
res. We does not quote life expectancy figures for bearings, but suggests practicable replace-
ment intervals based on the L 10 life of the bearing, the grease and the recommendations of
the bearing and grease manufacturers. For general-purpose applications, provid ing the vibra-
tion levels do not exceed the levels stated in ISO8528-9* and BS5000-3* and the ambient
temperature does not exceed 50°C the following approximations can be applied when *
(See section on vibration)
Sealed for life Bearings. - Approximately 30,000hours.
Re-greaseable bearings.- Approximately 40,000hours.
This is provided the correct maintenance is carried out, and only Kluber Asonic GHY 72 grease
(or equivalent) is used in all bearings. It is important to note that bearings in service. Under
good operating conditions, can continue to run beyond the remembered re placement period.
It should also be remembered that the r isk of bearing failure increases with time.
8.3 ALR FILTERS
Air filters for the removal of airborne particulate matter (dus) are offered as an addition to the
standard build option. Filters on it's need to be ordered with the generator. Air filters need to
be charged with oil before the genset is put to work (see 8.3.2) The frequency of fi lter mainte-
nance will depend upon the severity of the site conditions. Regular inspection of the elements
will be required to establish when cleaning is necessary.
Danger!
Removal of filter elements enables access to LIVE parts. Only remove elements
with the generator out of service.
8.3.1 CLEANING PROCEDURE
Remove the filter elements from the filter frames. Immerse of flush the element with a suitable
degreasing agent until the element is cleas.
As an alternative procedure a high-pressure water hose with a flat nozzle can be used. Sweep
the water spray back and forth across the element from the clean side (fine mesh side of
element) holding the nozzle firm ly against the element surface. Cold water may be adequate
depending upon type of contamination although hot water is preferable.
The element can be inspected for cleanliness by looking through the filter towards the light.
When the roughly clean, no cloudy areas will be seen. Dry elements thoroughly before attemp-
ting to carry out the recharging procedure.
8.3.2 RECHARGING (GHARGING) AIR FILTERS
Charging is best done by totally immersing the dry element into a dip tank containing "Filterko-
te Type k" or commercial lubricating oil SAE 20/50. oils of higher or lower viscosity are not
recommended.
Allow elements to completely drain before refitting the elements into the frames and putting
into service.
8.4 FAULT FINDING
IMPORTANT!
Before commencing any faultfinding procedures, examine all wiring for
broken or loose connections.
Two types of AVR can be fitted to the WH generator. The Refer to the generator nameplate for
type of AVR fitted.
8.4.1 MX341 AVR, FAULT FINDING
8.5 SEPARATE EXCITATION TEST PROCEDURE
The generator windings, diode assembly and AVR can be checked using the appropriate
following sections.
8.5.1 GENERATOR WINDINGS, ROTATING DIODES and PERMANENT MAGNET GENERA-
TOR (PMG)
IMPORTANT!
The resistances quoted apply to a standard winding. For generators
having windings or voltages other than those specified refer to fac-
tory for details. Ensure all disconnected leads are isolated and free
from
earth.
IMPORTANT!
Incorrect speed setting will give proportional error in voltage out put.
Checking Generator Windings and Rotating Diodes
This procedure is carried out w ith lead X and XX disconnected at the AVR or transformer
control rectifier bridge and using a 12 volt d. c. Supply to leads X and XX.
Start the set and run at rated speed.
Measure the voltages at the main output terminals U, V and W. if voltages are balanced and
/-10% of the generator nomial voltage, refer to 7 .5.1.1.
Check voltages at AVR terminals 6, 7 and 8. These should be balanced and between 170-250
volts.
If voltages at main terminals are balanced but voltage at 6, 7
and 8 are unbalanced, check continuity of leads 6,7 and 8.
If voltages are unbalanced , refer to 7 .5.1.2.
8.5.1.1 BALANCED MAIN TERMINAL VOLTAGES
If all voltages are balanced within 1 % at the main terminals, it can be assumed that all exciter
windings, main windings and main rotating diodes are in good order ,and the fault is in the
AVR or transformer control. Refer to subsection 7 .3.2 for test procedure.
If voltages are balanced but low, there is a fault in the main excitation windings or rotating
diode assembly. proceed as follows to identity:-
Rectifier Diodes
The diodes on the main rectifier assembly can be checked with a multimeter. The flexible leads
connected to each diode should be disconnected at the terminal end, and the forward and
reverse resistance checked. A healthy diode will indicate a very high resistance ( infinity) in the
reverse direction, and a low resistance in the forward direction. A faulty diode will give a full
deflection reading in both directions with the test meter on the 10,000 ohms scale, or an
infinity reading in both directions. On an electronic digital meter a healthy diode will give a low
reading in one direction, and a high reading in the other.
Replacement of Faulty Diodes
The rectifier assembly is split into two plates, the positive and negative, and the main rotor is
connected across these plates. Each plate carries 3 diodes, the negative plate carrying negati-
ve biased diodes and the positive plate carrying positive biased diodes. Care must be taken to
ensure that the correct polarity diodes are fitted to each respective plate. When fitting the
diodes to the plates they must be tight enough to ensure a good mechanical and electrical
contact, but should not be over-tightened. The recommended torque tightening is 4.06-4.74
Nm (36-42Ib in).
Surge suppressor
The surge suppressor is a metal-oxide varistor connected across the two rectifier plates to
prevent high transient reverse voltages in the fie ld winding from damaging the diodes. This
device is not polarized and will show a virtually infinite reading in both directions with an ordi-
nary resistance meter. If defective this will be visible by inspection, since it will normally fail to
short circuit and show signs of disintegration. Replace if faulty.
If after establishing and correcting any fault on the rectifier assembly the output is still low
when separately excited, then the main rotor, exciter stator and exciter rotor winding resistan-
ces should be checked (see Resistance charts ), as the fault must be in one of these windings.
The exciter stator resistance is measured across leads X and XX. The exciter rotor is conne.
Main Excitation Windingscted to six studs that also carry the diode lead t erminals. The main
rotor winding is connected across the two rectifier plates. The respective leads must be
disconnected before taking the readings.
8.5.1.2 UNBALANCED MAIN TERMINAL VOLTAGES
If voltages are unbalanced, this indicates a fault on the main stator winding or main cables to
the circuit breaker. NOTE: Faults on the stator winding or cables may also cause noticeable
load increase on t he engine when excitation is applied. Disconnect the main cables and sepa-
rate the winding leads U1-U2,(U5-U6),V1-V2,(V5-V6),W1-W2,(W5-W6) to isolate each winding
section. Note: -leads suffixed 5 and 6 apply to 12 wire windings only.
Measure each section resistance values should be balanced and /- 10% fo the value.
Measure insulation resistance between sections and each section to earth.
Unbalanced or incorrect winding resistances and/or low insulation resistances to earth indica-
te rewinding of the stator will be necessary. Refer to removal and replacement of component
assemblies' subsection 8.5.3.
5. INSTALLATION-PART 1
5.1 LIFTING
Warning!
Incorrect lifting or inadequate lifting capacity can result In severe personal injury
or equipment damage MINIMUM LIFTING CAPACITY REQUIRED IS AS INDICA
TED ON THE LIFTING LABEL. Generator lifting lugs should not be used for lifting
the
complete
Two lifting lugs are provided for use with a shackle and pin type lifting aid, A spreader with
chains, to ensure that the lift is vertical, of suitable length and lifting capacity must be used.
Lifting points are designed to position the craneage possible, but due to design restrictions it is
not possible to guarantee that the generator frame will remain horizontal while lifting, Care is
therefore needed to avoid personal injury or equipment damage, The correct lifting arrange-
ment is shown on the label attached to the lifting lug. (See sample below).
Single bearing generators are supplied fitted with a rotor retaining bar at the drive end of the
shaft. Single bearing generators are also fitted with wooden wedges supporting the fan for
transit purposes.
Once the bar is removed to couple the rotor to engine, the rotor is free to move in the frame,
and care is needed during coupling and alignment to ensure the frame is kept in the horizontal
plane.
5.2 ENGINE TO ASSEMBLY GENERATOR COUPLING
During the assembly of the generator to the engine it will be necessary to firstly carefully align,
the rotate, the combined Generator rotor - Engine crankshaft assembly, as part of the cons-
truction process, to allow location, insertion and tightening of the coupling bolts. This require-
ment to rotate the combined assemblies exists for both single and two beating units.
During the construction of single bearing units it is necessary to align the generator's coupling
holes with the engine flywheel holes. It is suggested that two diametrically opposite
Location dowel pins are fitted to the engine flywheel. The coupling can then slide into final
location on the engine flywheel recess. The dowels must be removed and replaced by coupling
bolts before the final bolt tightening sequence.
While fitting and tightening the coupling bolts it will be necessary to rotate the engine cranks-
haft - Generator rotor assembly. Care should be taken to ensure that rotation is carried out in
an approved manner that ensures safe working practice when reaching inside the machine to
insert or tighten coupling bolts, and that no component of the assembly is damaged by
non-approved methods of assembly rotation.
Engine Manufacturers have available a proprietary tool designed to enable manual rotation of
the crankshaft assembly. This tool must always be used, having been engineered as an appro-
ved method of assembly rotation, by engaging the manually driven pinion with the engine
flywheel starter ring-gear.
Danger!
Before working inside the generator, during the aligning and fitting of coupling
bolts, care should be taken to lock the assembly to ensure there is no possibility.
Of assembly rotational movement.
5.2.1 TWO BEARING GENERATORS
A flexible coupling should be fitted and aligned in accordance with the coupling manufacturer's
instruction.
If a close coupling adaptor is used the alignment of machine faces must be checked by offe-
ring the generator up to the engine. Shim the generator feet if necessary. Ensure adaptor
guards are fitted after generator/engine assembly is complete.
Open coupled sets require a suitable guard, to be provided by the set builder.
Axial loading of the generator beatings should be avoided. Should it be unavoidable contact
the factory for advice.
CAUTION! Incorrect guarding and/or generator a lignment can result in personal injury and/or
equipment
damage.
5.2.2 SINGLE BEARING GENERATORS
For transit and storage purposes the generator frame spigot and rotor coupling plates have
been coated with a rust preventative This MUST BE removed before assembly to engine.
A practical method for removal of this coating is to clean the mating surface areas with a
degreasing agent based on a petroleum solvent.
CAUTION! Care should be taken not to allow any cleaning agent to come into prolonged
contact with skin.
Alignment of single bearing generators is critical. If necessary shim the generator feet to ensure
alignment of the machined surfaces.
The sequence of assembly to the engine should generally be as follows:
1. On the engine check the distance from the coupling mating-face on the flywheel to the-
flywheel housing mating face. This should be within 0.5mm of nominal dimension. This is
necessary toensure that a thrust is not applied to the ac generator bearing or engine bearing.
2. Check that the bolts securing the flexib le plates to the coupling bub are tight and locked
into position. Refer to section 7. Subsection 7.5.3.4 for tightening torques.
3. Remove covers from the drive end of the generator to gain access to coupling and adaptor
bolts, check coupling joint interfaces are clean and inbrucant free.
4. Check that coupling discs are concentric with adaptor spigot. This can be adjusted by the
use of tapered wooden wedges between the fan and adaptor. Alternatively the rotor can be
suspended by means of a rope sling through the adaptor opening. Offer the generator to
engine and engage both coupling discs and housing spigots at same time, pushing generator
towards engine until coupling discs are against flywheel face, and housing spigots located.
5. Fit housing and coupling bolts taking care to use heavy gauge washers between coupling
bolt head and coupling disc. Tighten bolts evenly around assembly sufficiently to ensure
correct alignment.
6. Tighten housing bolts.
7. Tighten coupling disc to flywheel bolts. Refer to engine manufacturers manual for correct
tightening torque.
8. Remove rotor - aligning aids either wooden wedges, or the two M 10 set screws and sheet
metal wear plates.
Incorrect guarding and/or generator alignment can result in personal injury and/or equipment
damage.
5.3 EARTHING
The generator frame should be solidly bonded to the generating set bed-plate. If anti-vibration
mounts are fitted between the generator frame and its bed-plate a suitably rated earth conduc-
tor (normally one half of the cross sectional area of the main line cable) should bridge across
the anti - vibration mount. Refer to local regulations to ensure that the correct earthing proce-
dure has been followed.
5.4 PRE-RUNNING CHECKS
5.4.1 INSULATION CHECK
Insulation tests should be carried out before running the generator set, both after assembly
and after installation on site. (see Section 7.1)
IMPORTANT!
The windings have been H.V. Tested during manufacture and further H.V.
Testing may degrade the in sulation with consequent reduction in operating
life. Should It be necessary to demonstrate H.V. Testing, for customer
acceptance, the tests must be carried out at reduced voltage levels I.e.
Test Voltage=0.8(2 X Rated 1000)
5.4.2 DIRECTION OF ROTATION
The standard direction of rotation is clockwise, as viewed from the drive end. This matches the
predominant direction of rotation used by diesel engine manufacturers. The generator can be
driven in the opposite direction with a small reduction in efficiency and an increased noise
level. The phase rotation will also be effected.
5.4.2.1 PHASE ROTATION
Phase rotation is fixed for the standard direction of rotation, clockwise as viewed from the drive
end. If the generator is to be rotated in the counter - clockwise direction it will be necessary to
connect the customer output cables accordingly. Refer to the factory for 'reverse rotation
wiring diagram'.
5.4.3 VOLTAGE AND FREQUENCY
Check that the voltage and frequency that are required for the generating set application is as
indicated on the generator nameplate. If it is necessary to reconnect the stator for the voltage
required , refer to diagrams in the back of this manual.
5.4.4 AVR SETTINGS
To make AVR selections and adjustments remove the AVR cover and refer to depending upon
type of AVR fitted. Reference to the generator nameplate will indicate AVR type. Most of the
AVR adjustments are factory set in positions that will give satisfactory per formance during
initial running tests. Subsequent adjustment may be required to achieve Optimum performance
of the set under site operating conditions. Refer to 'Load Testing' section for details.
5.4.4.1 TYPE SX440 AVR
The following 'jumper' connections on the AVR should be checked to ensure they are correctly
set for the generating set application.
Refer to Fig.5 a for location of selection links.
1. Frequency seclection
4 pole 50Hz operation LINK C-50
4 pole 60Hz operation LINK C-60
2. Stability selection terminals
below
90kW
LINKA-C
below
550kW LINK
B-C
3. Stability selection terminals LINK 2-3
LINK4-5
LINK
6-7
4. Excitation Interruption Link
LINK K1-K2
5.5 GENERATOR SET TESTING
Warning!
During testing It may be necessary to remove covers to adjust controls exposing
'live' terminals or components. Only personnel qualified to perform electrical
service should carry out testing
5.5.1 TEST METERING/CABLING
Connect any instrument wiring and cabling requited for initial test purposes with permanent or
spring-clip type connectors Minimum instrumentation for testing should be line to line or line to
neutral voltmeter, Hz meter, load current meteting and kW meter. If reactive load is used a
power factor meter is desitable.
IMPORTANT!
When fitting power cables for load testing purposes, ensure cable voltage
rating is at least equal to the generator rated voltage. The load cable termi
nation should be placed on top of the winding lead termination and clam
ped between the two nuts provided.
CAUTION!
Check that all wiring terminations for internal or external wiring are secure,
and fit all terminal box covers and guards. Failure to secure wiring and/or
covers may result In personal Injury and/or equipment failure.
5.6 INITIAL START-UP
Warning!
During testing it may be necessary to remove covers t o adjus t controls expo
sing 'live' terminals or components
Only personnel qualified to perform electrical service should carry out testing
and/or adjustments. Replace all access covers after adjustments are completed.
On completion of generating set assembly and before starting the generating set ensure that
all engine manufacturer's pre-running procedures have been completed, and that adjustment
of the engine governor is such that the generator will not be subjected to speeds in excess of
125% of the rated speed.
IMPORTANT!
Over-speeding of the generat or is never advisable as this can result in
damage to the generator rotating components special care is necessary
during Initial setting of the speed governor.
In addition remove the AVR access cover and turn VOLTS control fully anti - clockwise. Start
the generating set and run on no - load at nominal frequency. Slowly turn VOLTS control
potentiometer clockwise until rated voltage is reached, refer to fig. 5 for control potentiometer
location.
IMPORTANT!
Do not increase the voltage above therated generator voltage shown on
the
generator
nameplate.
This STABILITY control potentiometer will have been pre-set and should normally not require
adjustment, but should this be required, usually identified by oscillation of the voltmeter, refer
to Fig. 5 for control potentiometer location and proceed as follows:
1. Run the generating set on no-load and check that speed is correct and stable.
2. Turn the STABILITY control potentiometer clockwise, then turn slowly anti-clockwise until the
generator voltage starts to become unstable.
The correct setting is slightly clockwise from this position ( i. E. Where the machine volts are
stable but close to the unstable region).
5.7 LOAD TESTING
Warning!
During test ing it may be necessary to remove covers to adjust controls exposing
'live’ terminals or components
Only personnel qualified to perform electrical service should carry out testing
and/or adjustments. Refit all access covers after adjustments are completed.
5.7.1 AVR ADJUSTMENTS
Refer to Fig. 5 for control potentiometer locations. Having adjusted VOLTS and STABILITY
during the initial start-up procedure, other AVR control functions should not normally need
adjustment. If instability on load is experienced, recheck stability setting. Refer to subsection
4.6.
If however, poor voltage regulation on-load or voltage collapse is experienced, refer to the
following paragraphs on each function to
A) Check that the symptoms observed do ind icate adjustment is necessary.
B) make the adjustment correctly.
5.7.1.1 UFRO (UNDER FREQUENCY ROLL OFF)
The AVR incorporates an under speed protection circuit that gives a voltage/speed (Hz)charac-
teristic as shown:
65
The UFRO control potentiometer sets the "knee Point". Symptoms of incorrect setting are a)
the light emitting diode (LED) indicator, just above the UFRO control potentiometer, being
permanently lit when the generator is on load, and b) poor voltage regulation on load, i.e. ope-
ration on the sloping part of the characteristic
Clockwise adjustment lowers the frequency (speed) setting of the "knee point" and extingui-
shes the LED. For Optimum setting the LED should illuminate as the frequency falls just below
nominal frequency, i.e. 4Hz on a 50Hz generator or 57Hz on a 60Hz generator.
IMPORTANT!
If the LED is i lluminated and no output voltage is present, refer to EXC
TRIP and/or OVER/V sections below.
5.8 ACCESSORIES
Refer to the "ACCESSORIES" Section of this manual for setting up procedures related to gene-
rator mounted accessories.
If there are accessories for control panel mounting supplied with the generator refer to the
specific accessory fitting procedures inserted inside the back cover of this book. Replace AVR
access cover after all adjustments are completed.
Warning!
Failure to refit covers can result in personal injury or death.
6. INSTALLATION-PART 2
6.1 GENERAL
The extent of site installation will depend upon the Generating set build, e. g. if the generator is
installed in a canopied set with integral switchboards and circuit breaker, on site installation will
be limited to connecting up the site load to the generating set output terminals. In this case
reference shou ld be made to the generating set manufacturer's instruction book and any
pertinent local regulations.
If the generator has been installed on a set without Switchboard or circuit breaker the following
points relating to connecting up the generator should be noted.
6.2 GLANDING
IMPORTANT!
To avoid the possibility of swarf e ntering any electrical components in the
terminal box, panels must be removed for drilling.
Summary of Contents for DAGFS Series
Page 10: ...9 2 Connect the battery red wire for anode black wire for cathode ...
Page 11: ...10 3 Press diesel pump to exhaust air until feel pressure 4 Turn on the emergency stop button ...
Page 14: ...13 Final step Finish set up the generator and then turn on breaker for auto protection ...
Page 26: ...25 ...
Page 27: ...26 ...
Page 28: ...27 ...
Page 29: ...28 TYPICAL APPLICATIONS ...
Page 30: ...29 ...
Page 31: ...30 7 EXPLODING VIEW AND PARTS LIST applies to all models CYLINDER BLOCK ASSEMBLY ...
Page 34: ...33 CYLINDER HEAD ASSEMBLY ...
Page 36: ...35 2 4 4 NUMBER PART NAME QUANTITY 34 35 36 Host ring Bolt M10X20 Spring washerφ10 ...
Page 37: ...36 CRANK AND CONNECTING ROD MECHANISM ...
Page 39: ...38 VALVE ACTUATING MECHANISM ...
Page 41: ...40 FUEL SUPPLY SYSTEM ...
Page 43: ...42 LUBRICATING SYSTEM ...
Page 46: ...45 COOLING SYSTEM ...
Page 49: ...48 ELECTRIC SYSTEM ...