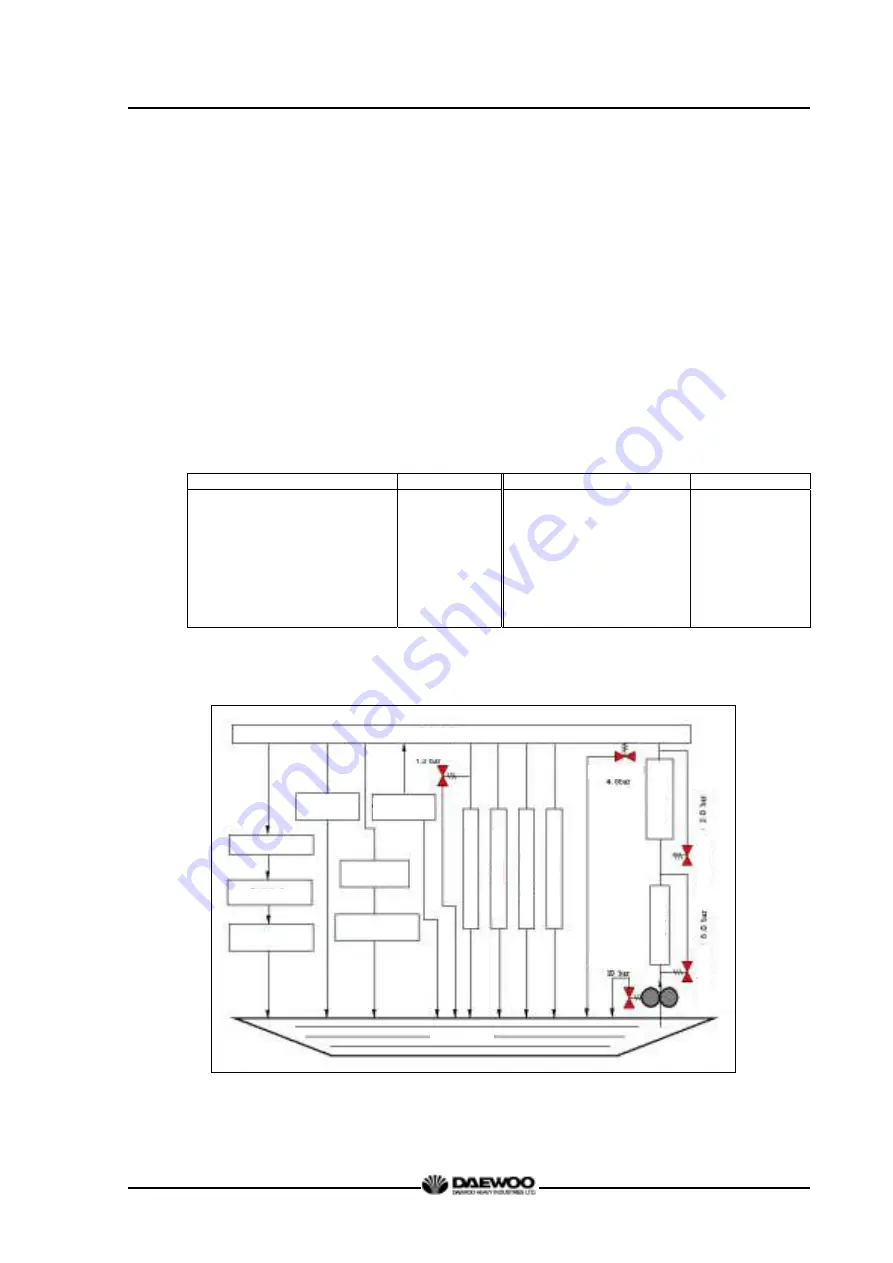
D1146/D1146TI/DE08TIS
MAINTENANCE MANUAL
102
Printed in Jan. 2001 PS-MMA0415-E1A
4.2. Lubricating System
4.2.1. General descriptions and specifications
z
General descriptions
All the engine oil pumped up from the oil pan by the gear type oil pump is filtrated
through the oil cooler and oil filter, and this filtrated oil is forced through the main oil
gallery in the cylinder block from where it is distributed to lubricate the various
sliding parts, and fuel injection pump in order to ensure normal engine
performance.
z
Specifications
Item Specifications
Item Specifications
Lubricating system
Forced pressure
circulation
Oil filter type
Full flow
Oil pump type
Gear type
Bypass for filter element
Relief valve opening pressure
10
±
1.5 kg/cm
2
Valve opening pressure
1.8
∼
2.3 kg/cm
2
Bypass for oil cooler
Bypass for entire oil filter
Opening pressure
5+1 kg/cm
2
Valve
opening
pressure 4.0
~
4.8 kg/cm
2
Adjusting valve for spray nozzle
Opening pressure
1.5
∼
1.8 kg/cm
2
z
Diagram of lubricating system
Main oil gallery
Relief valve
Camshaft
bearing
Idle gear
bush
Cylinder head
Rocker arm shaft
Rocker arm bush
Crankshaft
bearing
Connecting rod
bearing
Oil pan
Relief valve
Relief valve
Bypass va
lve
Bypass va
lve
Oi
l co
o
le
r
Oi
l
fil
te
r
Ai
r com
p
re
sso
r
Fue
l
in
jec
ti
on pump
Tu
rb
oc
h
ar
ge
r
P
is
ton sp
ray n
o
zz
le
Summary of Contents for D1146
Page 1: ...PS MMA0415 E1A MAINTENANCE MANUAL Diesel Engine D1146 D1146TI DE08TIS 65 99897 8056 Feb 2001...
Page 28: ...D1146 D1146TI DE08TIS MAINTENANCE MANUAL 24 Printed in Jan 2001 PS MMA0415 E1A...
Page 29: ...D1146 D1146TI DE08TIS MAINTENANCE MANUAL 25 Printed in Jan 2001 PS MMA0415 E1A...
Page 32: ...D1146 D1146TI DE08TIS MAINTENANCE MANUAL 28 Printed in Jan 2001 PS MMA0415 E1A...
Page 145: ...z WORLDWIDE NETWORK...
Page 146: ......
Page 147: ......