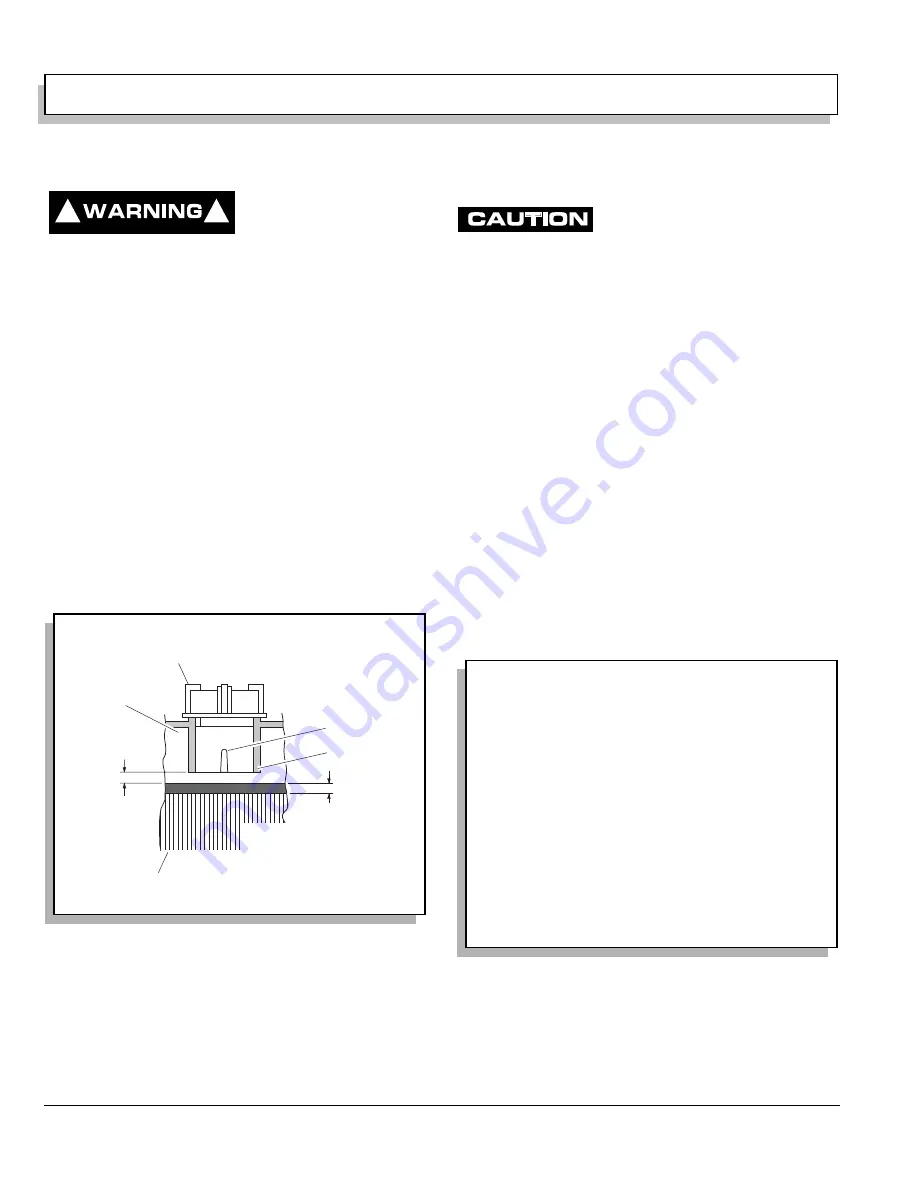
BATTERIES AND CHARGING
Page E-2
Owner’s Manual and Service Guide
Read all of manual to become thoroughly familiar with this vehicle. Pay particular attention to all Notes, Cautions and Warnings
At Each Charging Cycle
To reduce the possibility
of fire, never attach a
battery charger to a vehi-
cle that is to be unattended beyond the normal charg-
ing cycle. Overcharging could cause damage to the
vehicle batteries and result in extreme overheating.
The charger should be checked after 24 hours and
unplugged after the charge cycle is complete.
Before charging the batteries, inspect all plugs/recepta-
cles of the battery charging system for dirt or debris.
Charge the batteries after each days use.
Monthly
•
Inspect all wiring for fraying, loose terminations,
corrosion or deterioration of insulation.
•
Check that the electrolyte level is correct and add
suitable water as required.
•
Clean the batteries and wire terminations.
Electrolyte Level and Water
The correct level of the electrolyte is 1/2" (13 mm) above
the plates in each cell (Ref Fig. 1 on page E-2).
This level will leave approximately 1/4" - 3/8" (6 - 10 mm)
of space between the electrolyte and the vent tube. The
electrolyte level is important since any portion of the
plates exposed to air will be ruined beyond repair. Of
equal importance is too much water which will result in
electrolyte being forced out of the battery due to gassing
and the increase in volume of the electrolyte that results
from the charging cycle.
Do not overfill batteries. The charging
cycle will expel electrolyte and result in
component damage.
A battery being charged will ‘gas’ with the majority of the
gassing taking place at the end of the charging cycle.
This gas is hydrogen which is lighter than air. Water and
sulfuric acid droplets will be carried out of the battery
vents by the hydrogen gas; however, this loss is minimal.
If the battery electrolyte level is too high, the electrolyte
will block the vent tube and the gas will force it out of the
vent tube and battery cap. The water will evaporate but
the sulfuric acid will remain where it can damage vehicle
components and the storage facility floor. Sulfuric acid
loss will weaken the concentration of acid within the elec-
trolyte and reduce the life of the battery.
Over the life of the battery, a considerable amount of
water is consumed. It is important that the water used be
pure and free of contaminants that could reduce the life
of the battery by reducing the chemical reaction. The
water must be distilled or purified by an efficient filtration
system. Water that is not distilled should be analyzed
and if required, filtration installed to permit the water to
meet the requirements of the water purity table (Ref Fig.
2 on page E-2).
Even if the water is colorless, odorless, tasteless and fit
for drinking, the water should be analyzed to see that it
does not exceed the impurity levels specified in the table.
Automatic watering devices such as the one included in
the Battery Maintenance Kit can be used with an
Fig. 1 Correct Electrolyte Level
!
!
Vent Cap
1/4" to 3/8"
(6 to 10 mm)
Plates
1/2" (13 mm)
Vent
Gas Vent
Expansion
Space
Electrolyte level should
be at least 1/2" (13 mm)
above the plates and
1/4" to 3/8" (6 to 10 mm)
below vent
Impurity
Parts Per
Million
Color................................................................................ Clear
Suspended ...................................................................... Trace
Total Solids ...................................................................... 100
Calcium & Magnesium Oxides .......................................... 40
Iron ..................................................................................... 5
Ammonia ............................................................................ 8
Organic & Volatile Matter .................................................. 50
Nitrites ................................................................................ 5
Nitrates.............................................................................. 10
Chloride .............................................................................. 5
Fig. 2 Water Purity Table
Summary of Contents for MINUTE MISER
Page 7: ...Page iv Repair and Service Manual TABLE OF CONTENTS Notes...
Page 11: ...Owner s Manual and Service Guide SAFETY INFORMATION Page viii Notes...
Page 27: ...SAFETY Page B ii Repair and Service Manual Notes...
Page 37: ...BODY Page C ii Repair and Service Manual Notes...
Page 41: ...WHEELS AND TIRES Page D ii Repair and Service Manual Notes...
Page 45: ...BATTERIES AND CHARGING Page E ii Repair and Service Manual Notes...
Page 55: ...ELECTRONIC SPEED CONTROL Page F ii Repair and Service Manual Notes...
Page 61: ...MOTOR Page G ii Repair and Service Manual Notes...
Page 67: ...ELECTRICAL SYSTEM AND BATTERY CHARGER Page H ii Repair and Service Manual Notes...
Page 81: ...Page J ii BRAKES Repair and Service Manual Notes...
Page 87: ...BRAKES Page J 6 Repair and Service Manual Notes...
Page 89: ...REAR AXLE Page K ii Repair and Service Manual Notes...
Page 95: ...PAINT Page L ii Repair and Service Manual Notes...
Page 99: ...LIGHTNING PROTECTION AND GROUNDING Page M ii Repair and Service Manual Notes...
Page 105: ...GENERAL SPECIFICATIONS Page N ii Repair and Service Manual Notes...
Page 109: ...Page N 4 Repair and Service Manual GENERAL SPECIFICATIONS Notes...
Page 111: ...STEERING Page P ii Repair and Service Manual Notes...