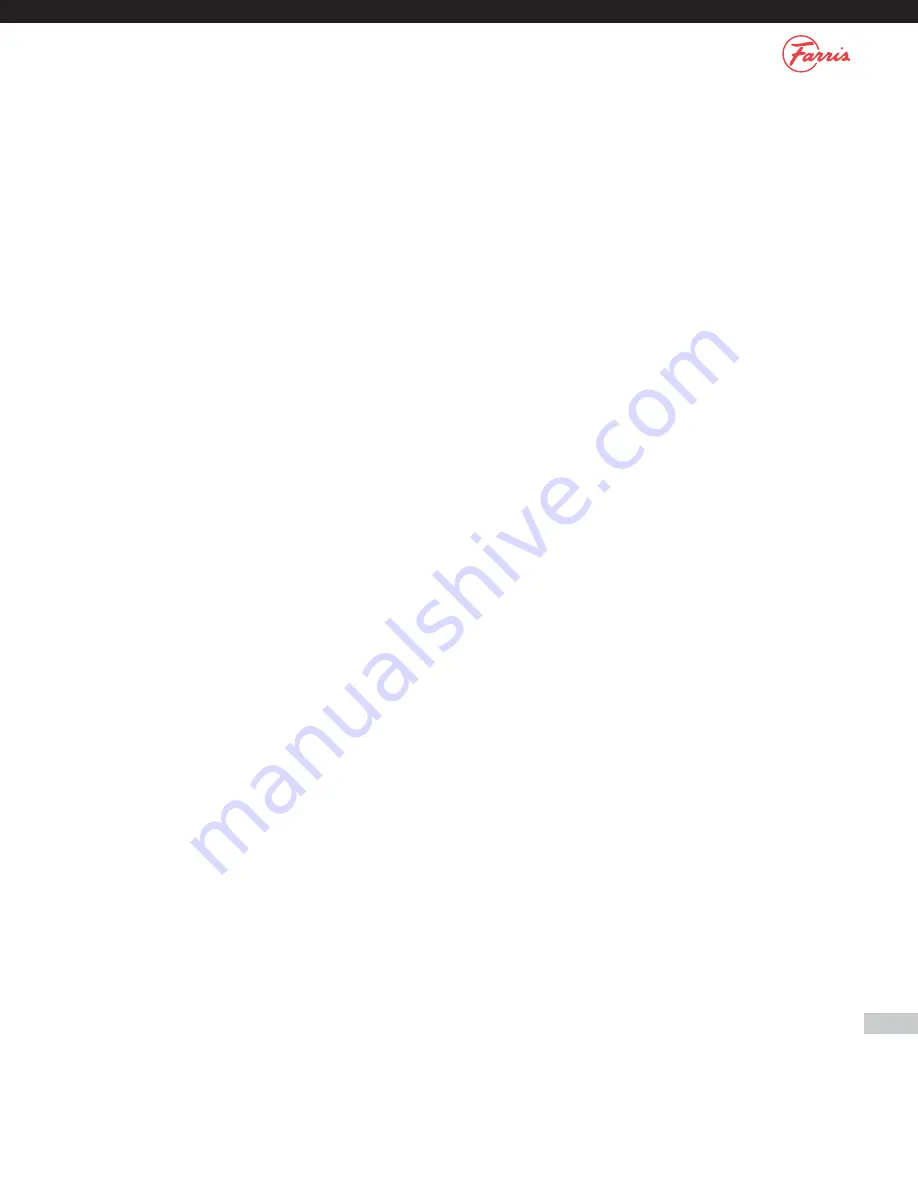
27
11. Troubleshooting
Chatter
The valve is oversized for installation.
If the inlet capacity is less than 25% of the valve capacity there will be a
tendency for the valve to chatter.
The inlet piping is of excessive length or the inlet pipe diameter is less
than the inlet size of the valve.
Design inlet piping systems so that the pressure drop to the valve is
less than 3%. The inlet pipe diameter should be at least the inlet size
of the valve.
The outlet piping is of excessive length or the diameter is less than the
valve flange size.
Design outlet piping so that the diameter is at least the outlet size of the
valve and that pressure on the outlet does not build up causing the valve
to shut.
Incorrect Set Pressure
Misreading the nameplate
Always compensate for backpressure and temperature when bench
testing the safety-relief valve by following the Cold Differential Test
Pressure.
The blowdown ring position changed
Check that the lock screw stud has engaged between the teeth on the
blowdown ring to prevent rotation. This could also cause erratic blowdown
characteristics as well as leakage.
Internals are misaligned.
See section on leakage.
Jam nut is loose.
Tighten jam nut.
Rough handling.
A safety-relief valve is a precision instrument and should be handled with
care. It is also recommended that the valve be popped once or twice to
realign the parts after rough handling.
Pressure surge at inlet.
Sudden impact of a fluid may cause the valve to open prematurely.
Pressure build-up should be gradual.
The valve contains a bellows and the bonnet is not vented.
Remove bonnet pipe plug so that the bonnet is exposed
to atmospheric pressure.
Leakage
The seats are damaged.
Lap the seats to remove the damage. If the scratches are deep, machining
may be required. Remove any foreign particles from the system to prevent
scoring the seats.
The system operating pressure is too close to the valve set pressure.
Always have at least 10% (or 5 psig, whichever is greater) differential
between operating pressure vs. set pressure for metal seated and soft
seated valves. See Table 10.5.
Misaligned lifting gear.
Adjust the stem test washer so that there is 1/8 inch clearance between
either the cam or lever and the stem test washer. See Appendix D.
Horizontal mounting.
Safety-relief valves must be mounted with the stem in the vertical plane. If
mounted horizontally the valve will experience excessive friction on the
guides and will not align properly.
Lock screw stud not adjusted properly.
Adjust the length of the lock screw stud so that it does not press into the
blowdown ring causing misalignment.
Misaligned internals.
Disassemble valve and check all universal ball joints, flatness of disc and
nozzle seat and repair or replace.
Other.
Check for bent stem, springs with uneven ends or out of alignment. A com-
mon cause of bent stems is overgagging. Test gags are designed to be
finger tightened only.
Blowdown
Blowdown is excessive/the valve is hanging up
Lower the blowdown ring until the desired blowdown is achieved. Also
check for dirt or other foreign material in the seating area or on the guiding
surfaces.
Blowdown is too short.
Raise the blowdown ring to lengthen the desired blowdown.
Summary of Contents for 2600 Series
Page 1: ...0713T R0 Series 2600 Maintenance Manual ...
Page 47: ...47 Notes ...