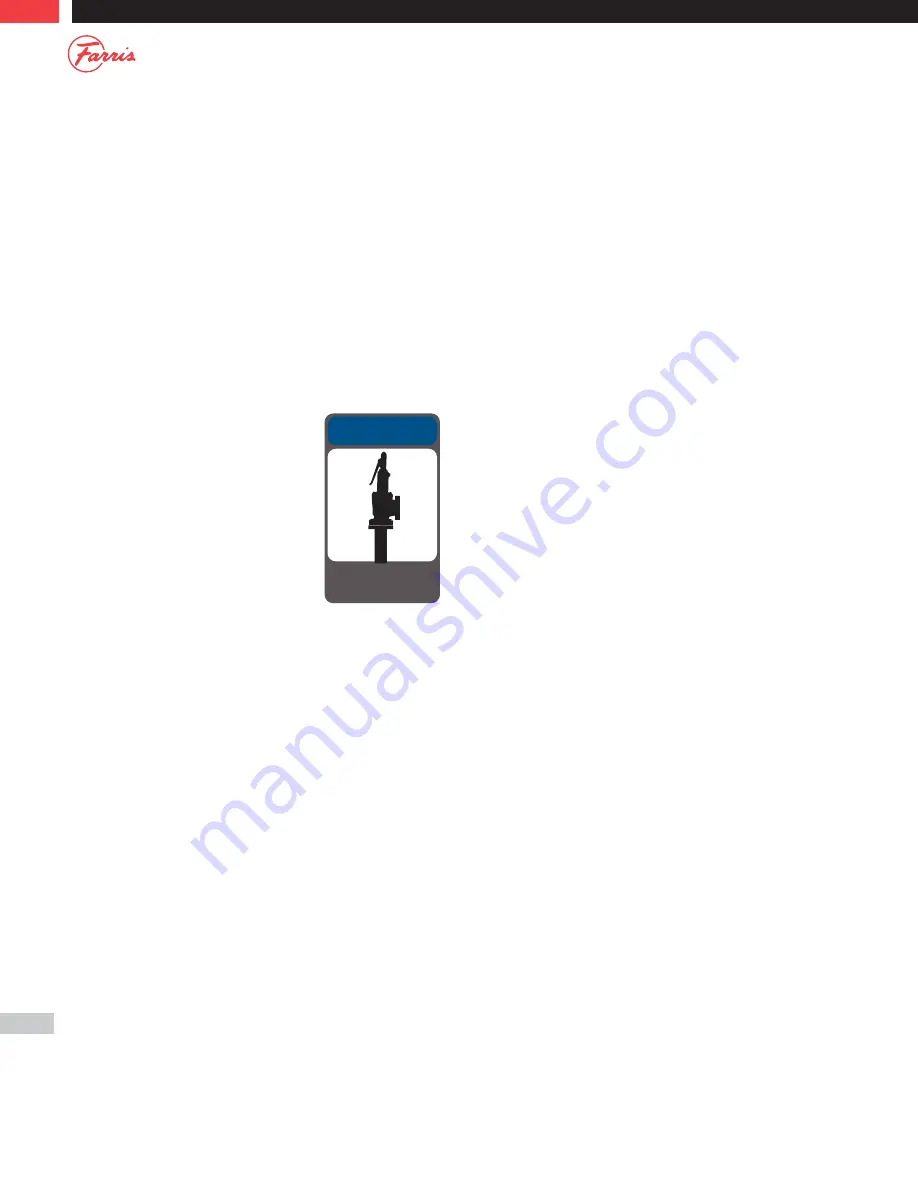
12
Inspection of Inlet and Outlet Piping
When a pressure relief valve is removed from service, the upstream and
downstream piping is often open and available for inspection. However,
where it is the practice to remove pressure relief devices from equipment
during operation by closing block valves, it is usually not possible to make
a complete inspection of piping. Such inspection should be made when
the operation equipment is out of service. Inspection of the piping at the
pressure relief valve will often indicate the condition of other process
piping which is not readily available for inspection. Piping should be
checked for corrosion, indications of thinning and deposits which may
interfere with valve operation. The characteristics of the deposits may supply
clues regarding leakage from the pressure relief valve in a closed system.
In-Situ Testing
In-situ or in place testing is frequently
performed as a substitute for valve removal and
in-shop testing. This should not be considered
as equivalent to shop maintenance; however it
may be employed under controlled situations to
extend the shop service frequency of particular
valves. The most common method of in-situ
testing employs an external power source
applied to the valve to determine the valve set
pressure at some lower system pressure. While
this method can accurately determine the valve
set pressure, valve reseat pressure cannot be determined using the
method. Care must be exercised with this method to avoid possible valve
damage that may go undetected during the in-situ test.
In-Shop Inspection
When a valve is first received in the shop it should be given a visual
inspection to note its condition when removed from service. The results
of this inspection should be noted on appropriate forms. It is generally
considered important to determine the set pressure of the valve when
removed from service and prior to the valve being disassembled. If the
valve opens at the set pressure, the valve need not be tested further to
determine the as-received relieving pressure. If the initial pop is higher
than the set pressure, it is advisable to test a second time. If the valve then
pops at approximately the set pressure, this indicates that the valve was
probably stuck because of deposits. If the valve does not pop near the set
pressure, this indicates that the valve setting was either in error originally
or may have been changed during operation.
Valves which are found acceptable upon shop pre-test cannot be returned
to service with a National Board “VR” stamp being applied unless they are
completely disassembled and complete repairs are undertaken. Some
maintenance programs may however authorize valves found acceptable
on shop pretest to be returned to service based on historical records,
tear-down cycles and all seals and valve identifications remaining intact.
Preparation For Maintenance
Before valve teardown is performed a review of previous maintenance
records will assist in an understanding of past valve performance, settings
and maintenance requirements. A complete maintenance records
management system will allow proper stocking of common replacement
items such as gaskets and seals and adequate stocking of major
replacement parts such as nozzles, discs, and springs. Maintenance
records, when properly updated, can serve to identify the need for ordering
spare parts when valve servicing shows that the useful life of a particular
part has been reached. Rework details and installation of new parts should
be recorded to aid future service activities.
NOTICE
Use care to avoid possible
PRV damage during In-Situ
testing.
Summary of Contents for 2600 Series
Page 1: ...0713T R0 Series 2600 Maintenance Manual ...
Page 47: ...47 Notes ...