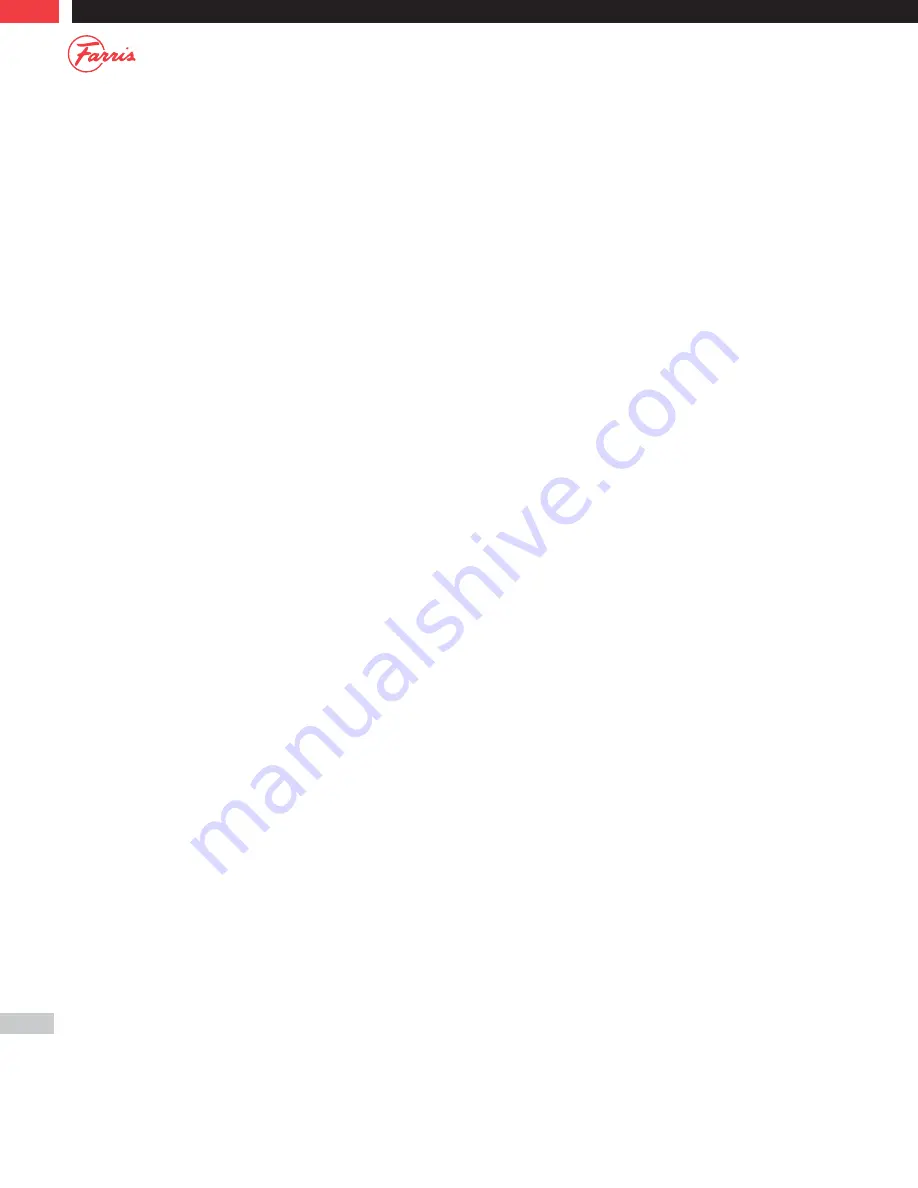
18
3. Lap the disc until all blemishes and score marks have been removed. As
the figure eight motion is executed, frequently lift the disc away from
the block to get a fresh bite on the compound. Most important, do not
contaminate compounds with dirt. Store lapping blocks and lapping
glass in a clean, dust-free area.
4. Follow the same procedure for lapping the nozzle. When lapping
nozzles, the nozzle can be placed on a table and a lapping block placed
on the nozzle. Be sure that the lapping block does not tip over the side
of the nozzle (which would cause rounding of the edges). Use a light,
rapid figure eight stroke, lifting the block from the nozzle occasionally.
5. When finished, be sure that all parts are carefully cleaned of all lapping
compound using a suitable solvent. Residual compound may damage
the seating surfaces during valve operation. When reassembling the
parts in the valve be careful not to scratch or score the seating surfaces.
6. If the nozzle or disc is badly scored or pitted a fine machine cut should
be made to reface the surfaces following instructions in the refacing
section of this manual.
Lapping Procedures (Machine)
Lapping machines come in a variety of styles. There are limitations to the
parts that can be lapped, which may be due to constraints of the lapping
machine or the nature of the part to be lapped.
Limitations:
1.
The size of the lapping machine.
Obviously, you will be limited by the size of the lapping plate on the
machine. A part that is larger than the lapping plate capacity will have
to be hand lapped.
2.
The weight of the part to be lapped.
Some parts will be too heavy to lap on the machine, relative to the area
to be lapped. These parts will have to be hand lapped.
3.
How well the part can be balanced on the lapping machine.
Due to geometry and weight distribution of the part, the part may
tend to wobble or fall over in the lapping machine. For these types
of parts a holding fixture should be designed or the part should be
lapped by hand.
General Operation
This is a general procedure for the use of lapping machines. ALWAYS
FOLLOW THE MANUFACTURER’S OPERATING INSTRUCTIONS.
Thoroughly clean all contaminates from the seat area of the nozzle or disc
to be lapped. Place the nozzle or disc seating area on the lapping plate.
Turn on the machine and adjust the flow of lapping fluid which should be
enough to keep the lapping plate covered with a thin film. The lapping
plate should be neither dry nor overly lubricated.
The duration of time that the nozzle or disc should be lapped is dependent
on the weight of the part, the hardness of the material, and the area to be
lapped. A combination of a heavy part with a small area to be lapped made
from a soft material will take the shortest time to lap. A combination of a
light part with a large area to be lapped made from a hard material will
take the longest time to lap.
Once the lapping is complete, remove the nozzle or disc from the lapping
plate and remove the lapping fluid with soft tissue and suitable solvent.
Protect the seating areas with soft tissue covered by a plastic cap.
Lapping Machine Maintenance and Seat Inspection
Seat flatness is critical to achieving leak tight seats. As the width of most
pressure relief valve seats is quite narrow, it is difficult to check seat
flatness directly with a monochromatic light. Instead, a standard test
block should be kept on the lapping machine that can be periodically
checked to determine the condition of the lapping plate. If the test block
“reads” flat then all parts lapped on the machine will also be flat. Since
the lapped surface needs to be reflective in order to “read” the surface
flatness using a monochromatic light source and optical flat, a polishing
stand is a needed accessory. Remove the test block from the lapping
machine and clean off all lapping fluid. Rub the test block on the polishing
stand as if you were hand lapping the test block. Only a few strokes will be
necessary to make the surface reflective enough to allow reading the lines
produced by the monochromatic light. For full details on how to read these
lines and the subsequent adjustments of the machine consult the lapping
machine manufacturer.
The quality of the lapped surface produced by the lapping machine can
only be as good as the level of maintenance of the machine itself.
Summary of Contents for 2600 Series
Page 1: ...0713T R0 Series 2600 Maintenance Manual ...
Page 47: ...47 Notes ...