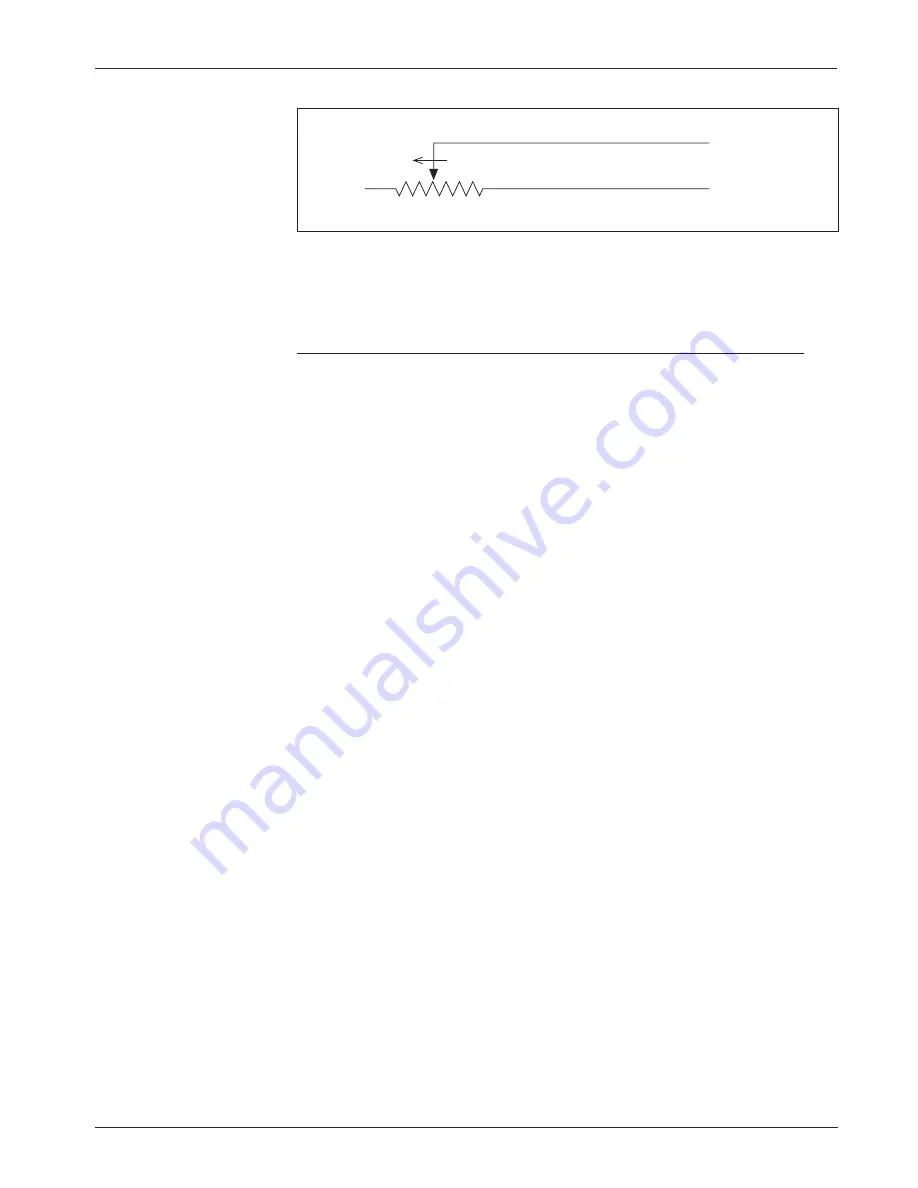
Curtis 1243
GEN
2 Manual
14
2 — INSTALLATION & WIRING:
Throttle
Fig. 10
Wiring for
0–5k
Ω
throttle
(“Type 3”).
a throttle fault is generated and the controller is disabled. Note: The Pot Low
pin (Pin 7) must not be tied to ground (B-).
Wigwag-Style 0–5V Voltage Source and 3-Wire Pot Throttle (“Type 4”)
These throttles (
“
Type 4
”
in the programming menu) operate in true wigwag
style. No signals to the controller
’
s forward and reverse inputs are required; the
action is determined by the wiper input value. The interface to the controller for
Type 4 devices is similar to that for Type 2 devices. The neutral point will be with
the wiper at 2.5 V, measured between Pin 6 and B-.
The controller will provide increasing forward speed as its wiper input
value (Pin 6) is increased, with maximum forward speed reached at 4.5 V. The
controller will provide increasing reverse speed as the wiper input value is
decreased, with maximum reverse speed reached at 0.5 V. The minimum and
maximum wiper voltage must not exceed the 0.5V and 4.5V fault limits.
When a 3-wire pot is used and the Pot Low Fault parameter (see Section 3,
page 36) is set to On, the controller provides full fault protection for Type 4
traction throttles. Any potentiometer value between 1 k
Ω
and 10 k
Ω
is sup-
ported. When a voltage throttle is used, it is the responsibility of the OEM to
provide appropriate throttle fault detection.
Note: If your Type 4 throttle has an internal neutral switch, this internal
neutral switch should be wired to the forward switch input (Pin 12). The
controller will behave as though no throttle is requested when the neutral
switch is high, and will use the throttle value when the neutral switch is low.
WIRING: Fault Outputs
The 1243
GEN
2 has two fault signal outputs (Pins 2 and 3), which can be used
to provide diagnostic information to a display panel. These current-sinking
outputs can drive LEDs or other loads requiring less than 10 mA. Since these
outputs are intended to drive LEDs, each contains a dropping resistor; as a
result, these outputs will not pull down to B-. Wiring is shown in Figure 11.
The Fault 1 and Fault 2 outputs can be programmed to display fault
information in either of two formats: Fault Code format or Fault Category
format (see Section 3, page 51).
Alternatively, Pin 2 can be used to provide a pump input signal (see pump
meter parameter, Section 3, page 48); Pin 3 can be used to interface an external
auxiliary enable circuit (see BDI lockout parameter, Section 3, page 51).
0–5k
Ω
Pot Low input
(Pin 7)
Pot Wiper input
(Pin 6)
FASTER