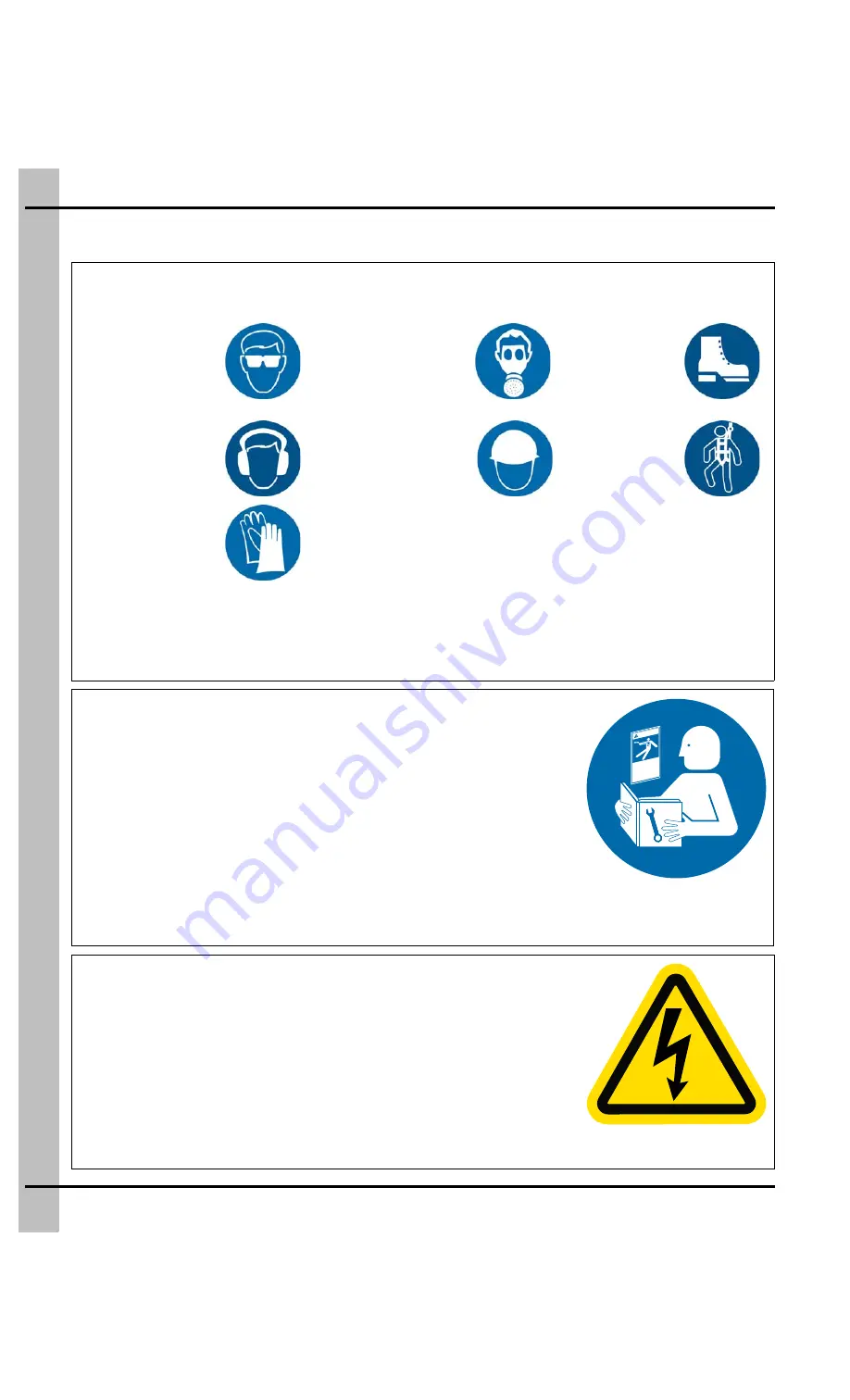
1. Safety
6
PNEG-2348
IR Hopper Sensor Installation
Safety Cautions
Use Personal Protective Equipment
Eye
Protection
Hearing
Protection
Hand
Protection
Head
Protection
Respiratory
Protection
Foot
Protection
Fall
Protection
• Use appropriate personal protective equipment:
• Wear clothing appropriate to the job.
• Remove all jewelry.
• Tie long hair up and back.
ST-0004-1
Follow Safety Instructions
• Carefully read all safety messages in this manual and
safety signs on your machine. Keep signs in good condition.
Replace missing or damaged safety signs. Be sure new
equipment components and repair parts include the current
safety signs. Replacement safety signs are available from
the manufacturer.
• Learn how to operate the machine and how to use controls
properly. Do not let anyone operate without instruction.
• If you do not understand any part of this manual or need
assistance, contact your dealer.
ST-0002-1
Install and Operate Electrical Equipment Properly
• Electrical controls must be installed by a qualified electrician and
must meet the standards set by applicable local codes (National
Electrical Code for the US, Canadian Electric Code, or EN60204
along with applicable European Directives for Europe).
• Lock-out power source before making adjustments, cleaning, or
maintaining equipment.
• Make sure all equipment is properly grounded.
ST-0027-4