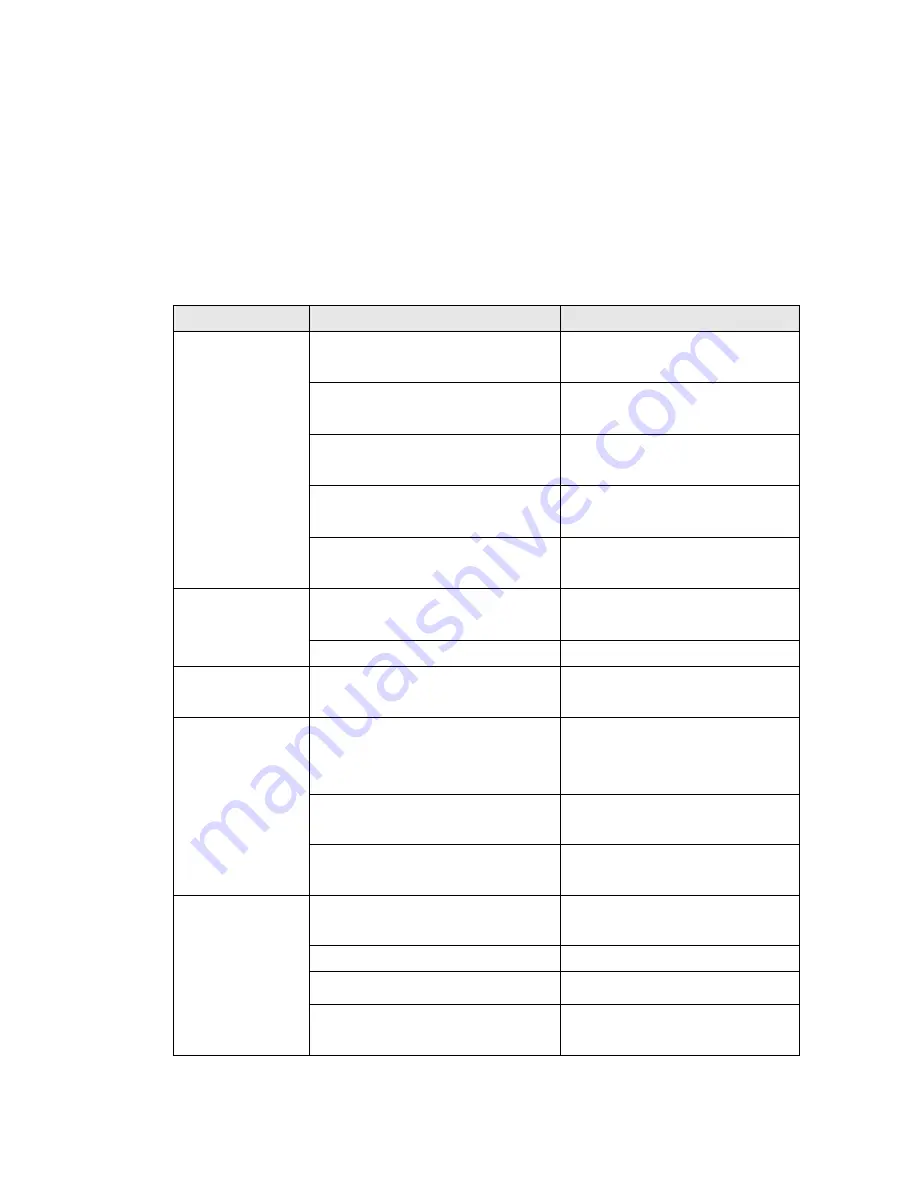
34
Note:
Printer status can be easily shown in the Diagnostic Tool. For more information about the
Diagnostic Tool, please refer to the instruction on the provided CD.
6.2 Print Quality
Problem
Possible Cause
Recovery Procedure
Check if interface cable is
connected to the interface connector.
Re-connect cable to interface.
The serial port cable pin configuration
is not pin to pin connected.
Please replace the cable with pin to
pin connected.
The serial port setting is not consistent
between host and printer.
Please reset the serial port setting.
The port specified in the Windows
driver is not correct.
Select the correct printer port in the
driver.
Not Printing
The Ethernet IP, subnet mask, gateway
are not configured properly.
Configure the IP, subnet mask and
gateway.
Label or ribbon not loaded correctly.
Follow the instructions to load the
media
or ribbon.
No print on the
label
Ribbon ran out.
Load a new ribbon.
Continuous
feeding labels
The printer media setting is not correct.
Run the initialization and
gap/black mark media calibration.
Gap/black mark sensor sensitivity is not
set properly (sensor sensitivity to
low)
Calibrate the gap/black mark sensor.
Make sure label size is set properly.
Set label size exactly as installed
in the labeling software or program
you are printing from.
Paper Jam
Labels may be stuck inside the printer
mechanism near the sensor area.
Remove the stuck label.
Top cover is not closed properly.
Close the top cover completely and
make sure the right side and left side
levers are latched properly
Check if supply is loaded correctly.
Reload the supply.
Ribbon and media are incompatible.
Change the ribbon or label
combination.
Poor Print Quality
Check if dust or adhesives are
accumulated on the print head.
Clean the print head.