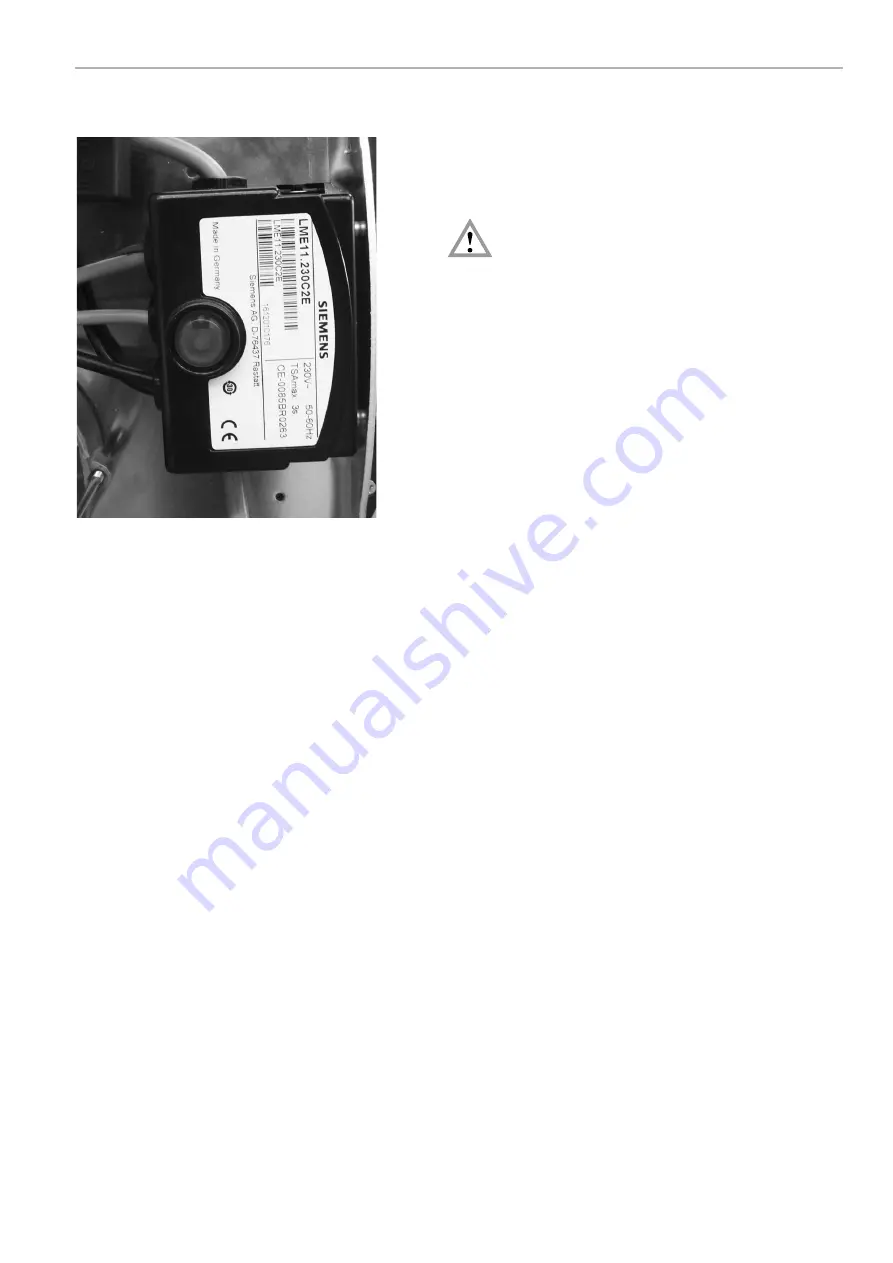
7
E
. 0
4.
99
•
G
.0
8.
08
.1
9
Function
Function
Control unit LME
Testing the control unit for proper functioning
Danger of fatal injury from electric shocks!
Disconnect electrical cable from power supply before
carrying out any work on live parts! Troubleshooting
may only be carried out by authorised and trained per-
sonnel! Unlocking may only be carried out by an autho-
rised specialist.
After startup and after maintenance of the burner, the following controls to perform.
Burner startup with broken lines to the flame detector:
•
Disconnect the cable to the flame monitor and restart the burner.
At the end of the safety time the controller makes a lockout
•
Reestablish the connection.
Burner operation with simulated loss of flame:
•
Pull the compact unit the square plug from the gas pressure switch and jumper the contacts in the
connector.
•
Start the burner.
•
Connect operation are the ball valve.
After loss of flame, the controller makes a lockout.
•
Remove the jumper in the connector and insert it back to the gas pressure switch of the compact unit.
Burner operation with simulated air pressure loss:
•
Pull are the operation from the air hose to the "+" input of the air pressure switch.
The controller makes a lockout.
•
Insert the air hose back onto the air pressure switch
Safety and switching functions
In the event of a flame failure during operation, the fuel supply is immediately switched off and the control
box goes into fault mode. A restart takes place in all cases following a mains power failure. A fault is trig-
gered immediately if there is flame detection during pre-ventilation. The position of the air pressure monitor
is continuously checked. There can be no start-up if it is not in its neutral position. A fault is triggered if the
working contact fails to close during pre-ventilation, or reopens. In the event of a lack of air during operation,
the air pressure monitor contact opens and the valves close immediately. The device goes into fault mode.