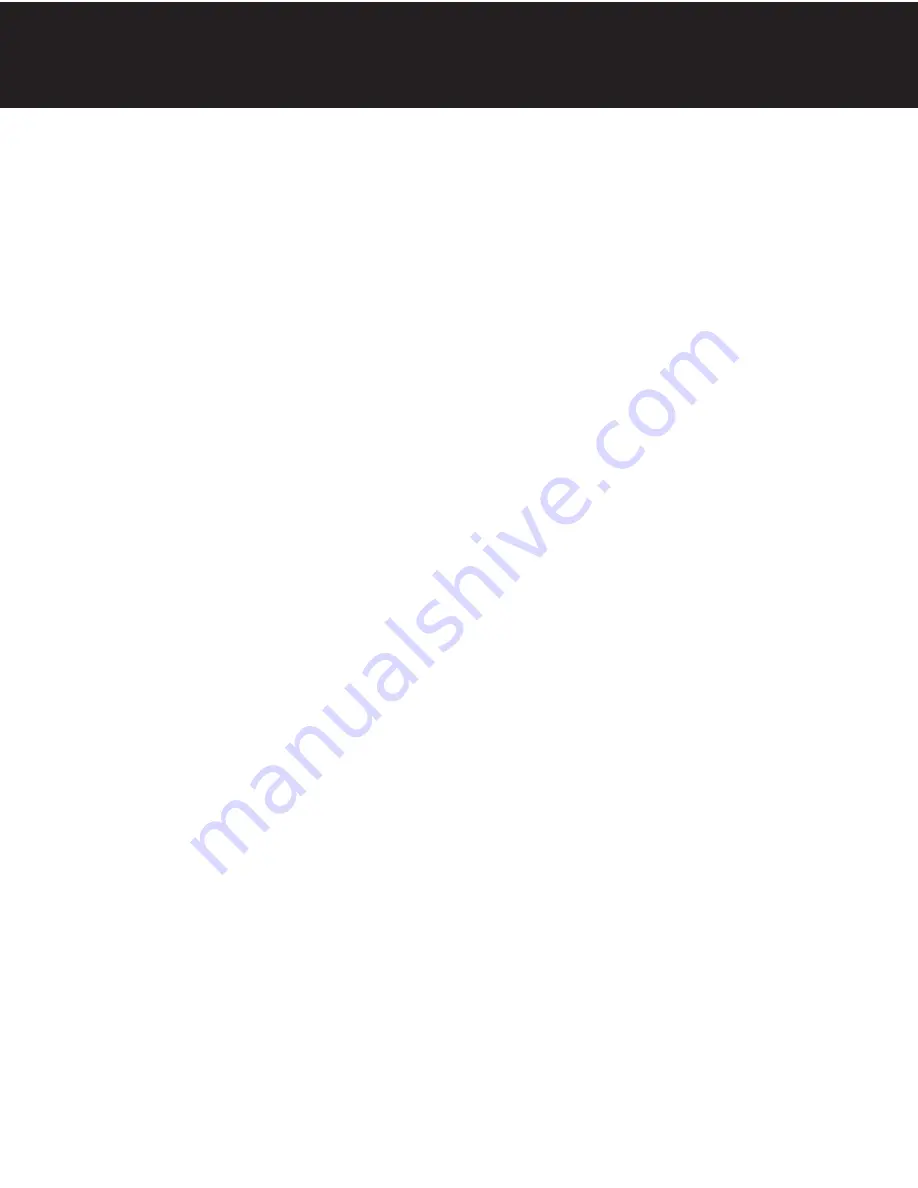
SIGNATURE 2 SERIES
Note:
• If household plumbing is galvanized and you intend to make the installation with copper (or vice versa), obtain
di-electric unions to prevent dissimilar metal corrosion.
Caution:
• If sweat soldering copper pipe (remember to always use lead free solder and flux), cover yoke and bypass
valve with wet rags to prevent heat damage to connections and control valve. If using PVC or plastic pipe,
primers and solvent cements specifically recommended for use with potable water are required.
Installation Procedure
- Water Supply Connection and Bypass Valve -
To allow for filter servicing, swimming pool filling or lawn sprinkling, a manual Bypass Valve has been installed
at the factory. The Bypass allows raw water to be manually routed around the filter.
1. Position filter at desired location for installation. If a water softener is to be installed, the filter should be
positioned first and then the softener.
2. The filter material is shipped separately from the mineral tank. The tank must be loaded with material after
tank has been placed at the desired location.
A. Remove the control valve by unscrewing from the tank. (Do not fill through dome hole, if installed.)
B. Use cap provided to place over top of distributor tube to prevent material from entering tube while
filling.
C. Place media funnel (part # U-1006) in hole on top of tank.
D. Pour several gallons of water in the tank. (Fill tank about 1/3 full.)
E. Pour in the required filter media. No gravel is required. The required quantity of media is listed in the
filter specifications.
Note:
If rebedding an existing unit and the system utilizes a standard tube & basket style
distributor, a “D” gravel underbedding will be required.
F.
After filling the tank with material, use a garden hose or several buckets to fill the tank with
water.
This will permit the filtering media to become soaked while preparing the installation and will
prevent the control valve from being plugged with floating material on initial backwash.
G. Remove funnel and clean filter media from tank threads.
H. Remove cap from distributor tube.
I. Replace control valve on mineral tank. Do not use Teflon tape or paste on valve threads, as the
valve to tank o-ring seals this joint.
Caution:
Be extremely careful to position distributor tube into control valve distributor tube pilot hole.
Installation
5