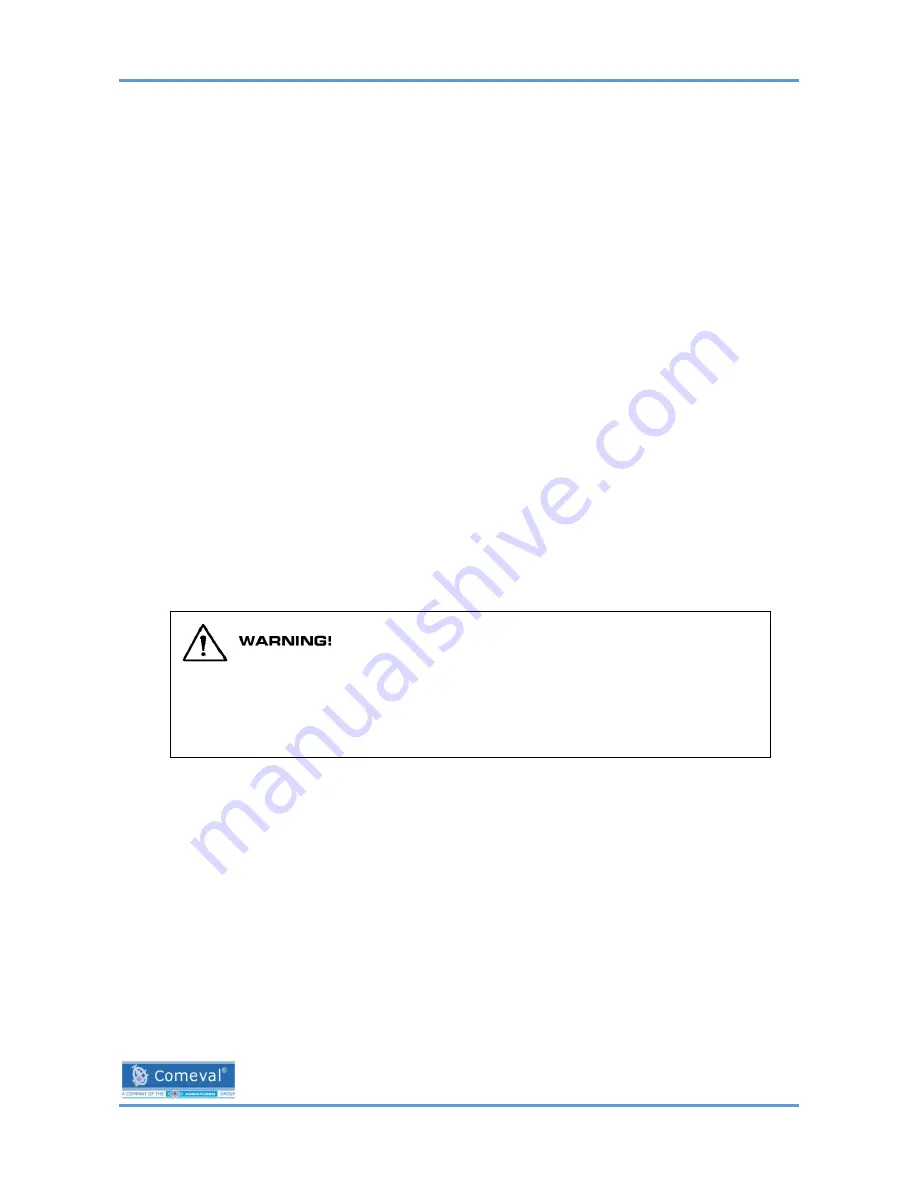
XLC 420
6
For further information please consult us at: www.comeval.es
Using the valve with extreme low flow rate and/or excessive differential pressure
conditions may cause pulsations and instability. Please make reference to the
recommended flow and pressure charts or contact CSA for assistance with the proper
sizing.
Installation
The automatic control valve XLC 400 must be always installed in a horizontal position with the
bonnet upwards. Smaller valves, (up to
150 mm) can be installed in a vertical pipe shouldn’t be
unavoidable. Prior to that consult us and specify the orientation in the order. A stable and non
pulsating source of pressure is necessary for the proper performance of CSA control valves,
whose minimum pressure is displayed on the technical brochure and always 0,5 bar on the pilot in
addition to the headloss produced during working conditions.
Gate valves or other sectioning devices must be installed upstream and downstream of
CSA control valves to allow for maintenance.
The operating fluid must be free of air, air valves (CSA Mod. FOX 3F AS combination anti-
slam) should be installed downstream and upstream. This to avoid the accumulation of air
pockets during working conditions, allow air discharge during pipe filling and entrance in
case of pipe burst and draining.
A suitable by-pass should be provided for servicing of the valve without interrupting the
flow. For the by-pass sectioning do not use standard gate valve, likely to get damaged
during modulation, but rely on globe pattern gate valves and/or CSA direct acting pressure
sustaining / relief valves Mod. VSM.
If not included in the order install pressure gauges upstream and downstream if necessary,
a flow measurement device is always recommended to make sure hydraulic conditions
remain within the values used for sizing.
A strainer with suitable basket and mesh should be installed ahead of the valve to protect
internal components from debris, particles and foreign material.
Sufficient space should be provided around the valve for disassembly.
Check direction of flow and make sure it is according to the marking on the valve’s casting.
Make sure the flanges and pipes connection are according
to the valve’s standard. The
nuts and bolts setting has to be conducted in the proper way, gradual and symmetrical, in
order not to produced additional stress and deformation.
During handling be sure not to damage the glass of the position indicator, if present.