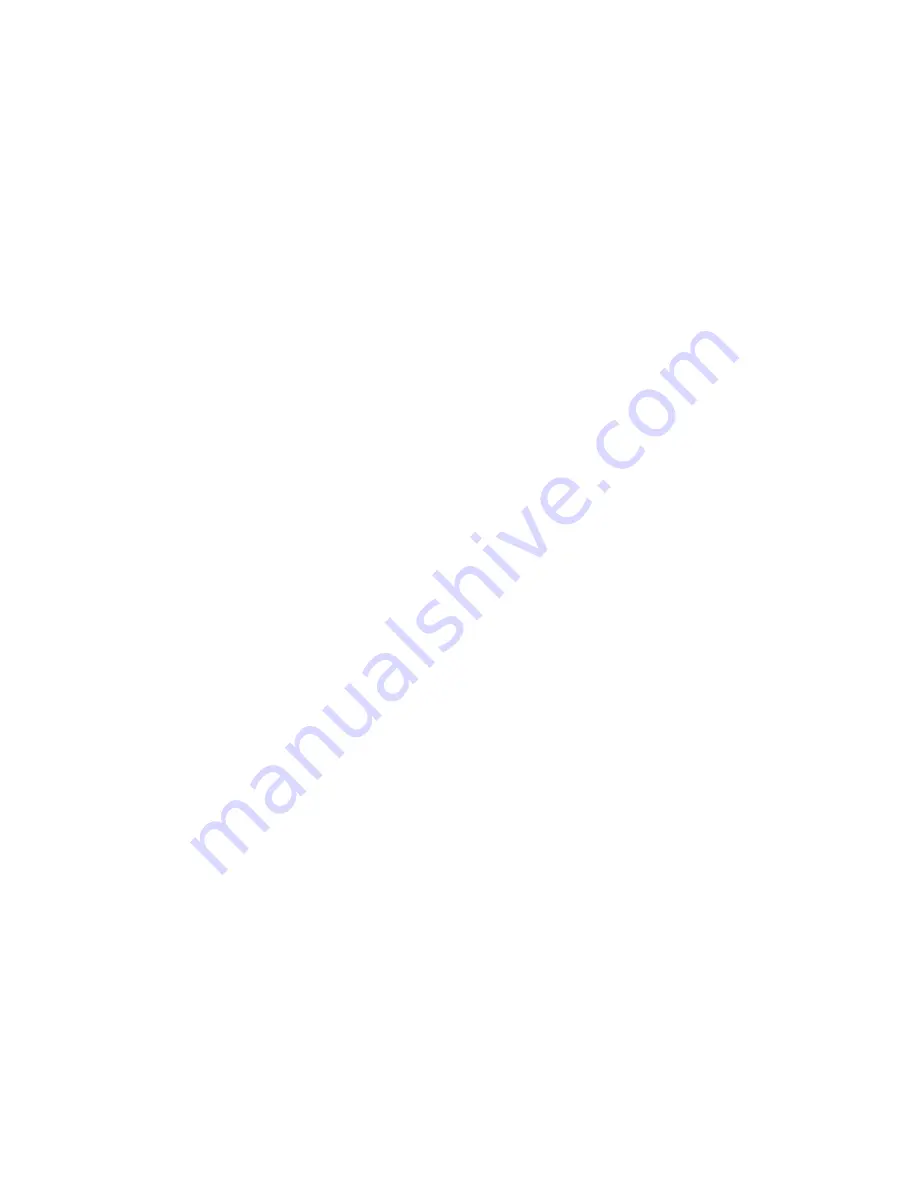
Section IV Page 1
SERVICE INSTRUCTIONS
4.1 GENERAL
This section contains principles of operation, inspection procedures, maintenance
procedures, and troubleshooting. Refer to the following drawings in Section 5,
while reading this section.
4.2 MAJOR COMPONENTS AND THEIR PRINCIPLES OF OPERATION
Following is a list of the major components and their function and operation
A. MAIN AIR SOLENOID VALVE.
Controls the air supply to the unit. When the Unit is ON, the solenoid is
energized thus opening the valve to supply air to the pneumatic circuit.
B. ABRASIVE PINCH and its SOLENOID VALVE ASSEMBLY
The Abrasive Pinch Valve controls the powder/air mixture flow to the nozzle.
When the Power Switch is in the ON position the Abrasive Pinch Valve
Solenoid Valve is energized and allows air pressure to flow to the Abrasive
Pinch Valve. The air enters the bottom of the pinch valve, flows through a
passage to displace the depressor which in turn pushes the plunger up to pinch
the valve tube closed.
When the solenoid valve is de-energized by depressing the Footswitch or Flow
Test Switch the air pressure to the Abrasive Pinch Valve is shut off. The pinch
valve exhausts it's pressure that allows the plunger to be retracted by spring
pressure and open the valve tube. When the Footswitch or Flow Test Switch is
released the pinch valve is again pressurized and the plunger closes or
"pinches" the valve tube.
When the Power Switch is turned to the OFF position the Abrasive Pinch Valve
remains closed to allow any remaining air pressure in the system to bleed off
through the Bleed Off Pinch Valve and hose.
C. BLEED OFF PINCH VALVE ASSEMBLY
When the Power Switch is turned “OFF”, the air pressure to the Bleed Off Pinch
Valve is shut off allowing the pinch valve to exhaust its pressure out through the
Main Air Solenoid and allow its depressor and plunger to be retracted under
spring pressure to open the valve tube. When the valve tube is opened the
pressurized chambers and air lines are allowed to bleed off remaining pressure
through the pinch valve tube and into the bleed off hose.
When the Power Switch is turned to the ON position the exhaust passage of
the Main Air Solenoid is blocked, allowing the Bleed Off Pinch Valve to be
pressurized and push its depressor and plunger up to close or "pinch" the pinch
valve tube. Thus allowing the chambers to pressurize.
Summary of Contents for SWAM-BLASTER LV-1
Page 10: ...Figure 3 1 Operating Controls Indicators Connectors ...
Page 26: ...Section V Page 2 ...
Page 27: ...Section V Page 3 ...
Page 28: ...Section V Page 4 ...
Page 29: ...Section V Page 5 ...
Page 30: ...Section V Page 6 ...
Page 31: ...Section V Page 7 ...
Page 33: ...Section V Page 9 O RING 550 020 23 TOP COVER ASSY P N 3545 1 ...
Page 41: ...Section V Page 17 PINCH VALVE COMPLETE ASSEMBLY 3405 1 ...
Page 45: ...Section V Page 21 GRN WHT BLK NO NC C 4 BLK WHT GRN 3 2 1 ...
Page 47: ...Section V Page 23 ABRASIVE NOZZLE CRYSTAL MARK INC REV 9 08 QUICK NUT ASSY 1721 1 ...
Page 48: ...Section V Page 24 ...