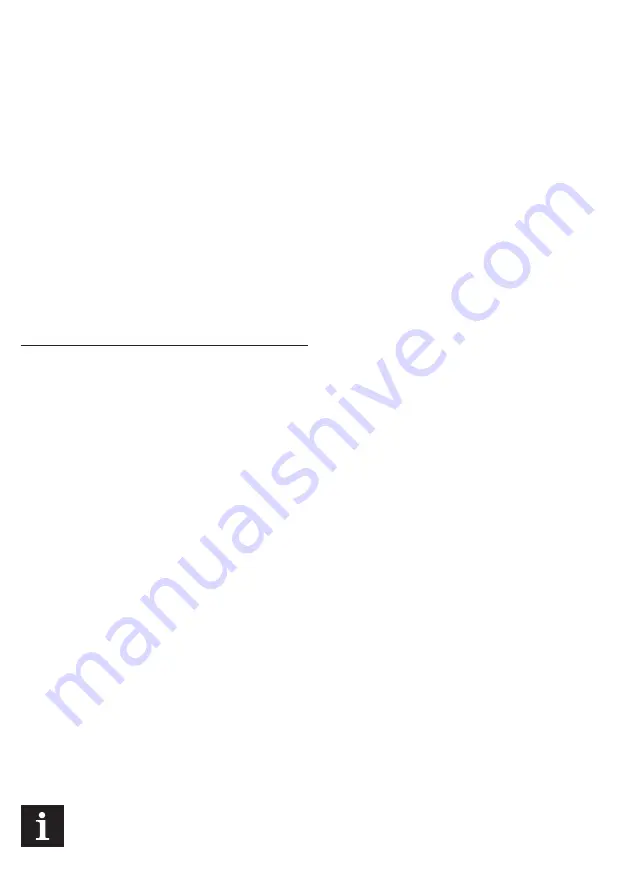
21
English
Scale marking is done such that turning of control
4
for
one mark will change the welding current on 10%� If con-
trol
4
set in position 0 - function hot start switched off� If
control
4
set in position 10 - increase of the welding cur-
rent at the moment of ignition of the welding arc on 100%�
Arc force ("ARC FORCE" control)
The arc force function allows the sticking of the elec-
trode to a piece to be welded to be prevented�
When reducing the distance between the electrode
and the piece to be welded, the welding current is in-
creased for a short time which allows the metal of the
electrode and a work piece to be fused immediately,
thus increasing the arc gap�
[CT33139, CT33127, CT33126]
Control
9
can change the arc dynamics - lesser values
provide for smaller metal splashing while bigger values
provide for deeper fusion penetration�
Easy start
The easy start function (increased voltage of idle run-
ning) facilitates the lighting up of the welding arc�
Recommendations on the machine op
-
eration
Preliminary works (see fig. 3)
•
Finish the edges of work pieces to be welded is rec-
ommended�
•
Angle of flare (a, see fig. 3.1)
- is carried out
when metal is more than 3mm thick� Absence of
grooving can result in spilling on section of weld, and
also in overheating and burning of metal; atabsence
of grooving, for maintenance of weld penetration al-
ways try to increase size of a welding current�
•
Backlash (b, see fig. 3.2)
- correctly fixed before
welding, allows full weld penetration on section of
weld at imposing the priming layer of a seam�
•
The length of a sheet bevel (c, see fig. 3.3)
-
adjusts smooth transition from thicker welded detail
to more thin, thus stress concentrators in welded
structures are eliminated�
•
Clean welding surfaces from rust and paint coatings�
•
Please remember that a large quantity of heat is
released during welding which can damage the sur-
rounding items, therefore, carefully choose the site
and take appropriate actions to prevent fire.
Electrodes
The right choice of electrodes, to a great extent, pre-
determines the welding seam quality and the opera-
tion speed� Before purchasing electrodes, carefully
examine the recommendations of their use� Consult a
specialist if necessary� It is also important to observe
the electrode storage conditions�
General operation recommendations (see fig. 3)
The recommendations below apply to all
machines connected through a socket
connector. In the case of stationary con
-
nection the machine assembly and net
-
work connection will be done beforehand.
•
Place the machine in an even, dry, not vibrating
surface observing all above-mentioned safety proce-
dures�
•
Connect the ground wire�
•
Connect the welding cables to the machine� Weld-
ing can be performed with direct and reverse polarity�
The selection of polarity depends on the materials to
be welded and the recommendations on how to use
electrodes�
•
Direct polarity
- connect electrode holder
14
to socket "-"
10
, connect earth clamp
13
to sock-
et "+"
11
� In such a mode the electrode heats less
than the basic metal, the electrodes get fused slow-
er, the welding joint is completed with a deeper pen-
etration�
•
Reverse polarity
- connect electrode holder
14
to socket "+"
11
, connect earth clamp
13
to sock-
et "-"
10
� In such a mode the work piece is heated
less than the electrode which can be used for weld-
ing high-carbon, alloy and special steels sensitive to
overheat as well as for welding sheet metal�
•
Press the lever of the electrode holder
14
and install
the electrode end (the end free from coating) into elec-
trode holder
14
and then release the lever�
•
Fix earth clamp
13
on one of the parts to be welded�
•
Connect the machine to the mains and switch it on�
•
Set the welding current value using control
5
� The
selection of welding current depends on the electrode
to be used, thickness of material to be welded, spatial
position of a seam etc�
•
Choose additional welding parameters (arc force
etc), if your machine has these functions�
•
Ignite the welding arc in one of two ways: ignition
by touching (see fig. 3.4); ignition by scratching (see
fig. 3.5).
•
The main practices of welding electrode handling
are described below:
•
usually welding is carried out with vertically po-
sitioned electrode or at its inclination concerning a
seam, in a corner forward or back� When welding by
a corner back, it is provided better fusion and smaller
width of a seam (but performance of work in this case
demands the certain skill);
•
progressive motion of an electrode (see
fig. 3.6)
- on a direction of an axis of the electrode, for
maintenance of necessary arch length which should
make 0,5-1,1 of electrode diameter� The length of an
arch renders the serious influence on quality of a weld
-
ed seam and its form� A long arch causes intensive oxi-
dation and nitration of the fused metal, and increased
splashing of it;
•
longitudinal movement of an electrode (see
fig. 3.7)
- for formation of a welded seam� Speed of
movement of an electrode depends on electric cur-
rent, electrode's diameter, type and spatial position of
a seam;
at the high speed of an electrode
the basic metal
has no time for fusion, what results in insufficient
depth of weld fusion spill is formed;
insufficient speed of moving of an electrode
re-
sults in overheating and arc burn (through fusion)
of metal;
correctly chosen speed of longitudinal movement
along an axis of a welded seam allows obtaining its
width on 2-3mm more than diameter of an electrode;
•
lateral movement of an electrode (see fig. 3.8)
-
for formation of the widened welded seam� An elec-
trode is moved in lateral oscillatory movements more
often with constant frequency and the amplitude,
combined with progressive motion of an electrode
Summary of Contents for 425249
Page 1: ......
Page 5: ...5...
Page 6: ...6...
Page 7: ...7...
Page 8: ...8...
Page 88: ...88 IEC 60974 9 9 S CROWN...
Page 89: ...89 20 40 40 CROWN www crown tools com CROWN 50...
Page 90: ...90 10 20 1...
Page 93: ...93 14 11 13 10 14 14 13 5 3 4 3 5 3 6 0 5 1 1 3 7 2 3 3 8 2 3 14 20 30 2 www crown tools com...
Page 95: ...95 IEC 60974 9 9 S CROWN...
Page 96: ...96 20 C 40 C 40 C CROWN www crown tools com CROWN...
Page 97: ...97 50cm 10 20 1 CT...
Page 101: ...101 2 www crown tools com...
Page 103: ...103 IEC 60974 9 9 S CROWN...
Page 104: ...104 20 C 40 C 40 CROWN www crown tools com CROWN...
Page 105: ...105 50 10 20 1 CT XX XXXXXXX...
Page 106: ...106 1 2 e 3 4 HOT START 5 WELDING CURRENT 6 7 8 9 ARC FORCE 10 11 12 13 14 15 16 17 1 3 16 1...
Page 108: ...108 3 14 10 13 11 14 11 13 10 14 14 13 ee 5 3 4 3 5 3 6 0 5 1 1 3 7 2 3 3 8 2 3 14 20 30 2...
Page 109: ...109 www crown tools com...
Page 111: ...111 IEC 60974 9 9 S CROWN...
Page 112: ...112 20 C 40 C 40 CROWN www crown tools com CROWN 50...
Page 113: ...113 10 20 1 CT XX XXXXXXX...
Page 125: ...125 IEC 60974 9 9 idie S CROWN...
Page 126: ...126 20 C 40 C 40 CROWN www crown tools com CROWN 50...
Page 127: ...127 1 10 20 CT XXXXXXX...
Page 130: ...130 3 14 10 13 11 14 11 13 10 14 14 13 5 3 4 3 5 3 6 0 5 1 1 3 7 2 3 3 8 2 3 14 20 30 2...
Page 131: ...131 www crown tools com...
Page 132: ...132...
Page 133: ...133...
Page 134: ...134...
Page 135: ...135...
Page 136: ...136...
Page 137: ...137...
Page 138: ...138...
Page 139: ...139...
Page 140: ...140...
Page 141: ...141...
Page 142: ...142...
Page 143: ...143...
Page 144: ...144...
Page 145: ...145...
Page 146: ...146...
Page 147: ...147...
Page 148: ......