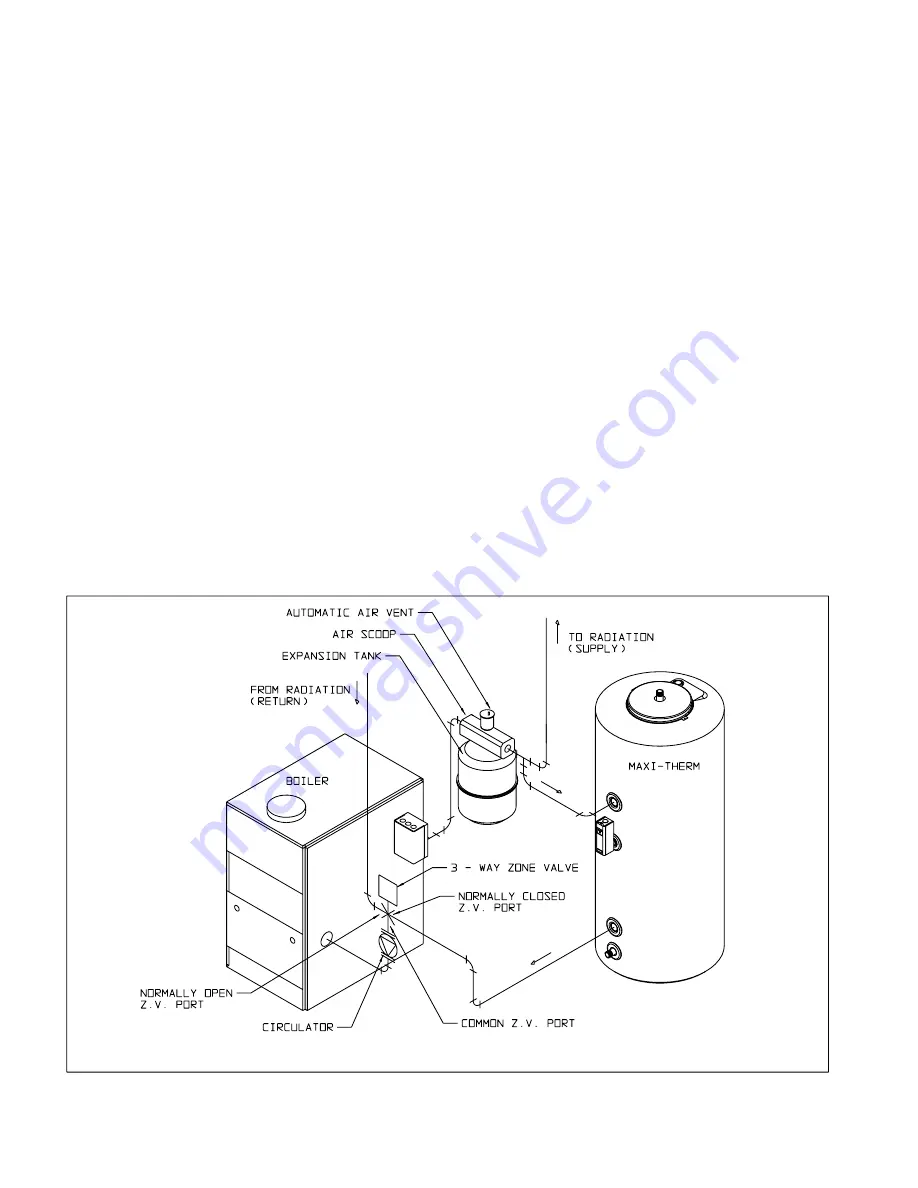
RADIANT PANEL OR OTHER “LOW TEMPERATURE” SYSTEM
The First Hour Ratings published in this manual are based on a boiler supply temperature of 180F. If, for
any reason, the boiler water temperature going to the heating system is held to levels under 180F, special piping
is needed to provide boiler water to both the Maxi-Therm and the heating system at the proper temperatures.
Two ways of doing this are with a heat exchanger or a 4-way valve.
In either system, the Maxi-Therm must be connected to the boiler before any means are used to control the
temperature of the water going to the system. The temperature of the water going through the Maxi-Therm coil
is thus limited only by the boiler high limit setting, which should be set at 180F or higher.
Figure 9 illustrates the use of a heat exchanger to control the temperature of the water going to the “low
temperature” system. The low temperature system water is completely isolated from the water passing through
the boiler and Maxi-Therm. For this reason, the low temperature system must be equipped with its own
expansion tank, fill, and air removal apparatus. The temperature in this system may be controlled through the
use of an aquastat in the low temperature side.
Figure 10 illustrates the use of a 4-way valve to control maximum heating zone temperature while allowing
180F boiler water to enter the Maxi-Therm zone. The four way valve may be manually set to provide the
maximum allowable temperature to the heating zone or it may be provided with a motor to control the valve in
response to some parameter (outdoor temperature for example).
MAXI-THERM MANIFOLD PIPING (BOILER SIDE)
Multiple Maxi-Therm installations must be done in the “reverse-return” manner illustrated in Figure 11. The
reason for this is to create the same pressure drop (and therefore the same flow) through the coil of each Maxi-
Therm. The boiler manifold piping must be sized so that each coil has the flow rate called for in Table 1. For
example, if two MT040G’s are to be manifold together, the circulator and zone piping common to both tanks
must be capable of moving 16 GPM (2 x 8 GPM)
Because the pressure drop through Maxi-Therm coils varies from size to size, it is hard to predict the flow
rate that will be developed through each coil when two Maxi-Therms of different sizes are placed in the same
manifold. For this reason it is best not to mix Maxi-Therms of two different sizes in the same zone.
Figure 8: Boiler-Side Piping a 3-Way Zone Valve
22