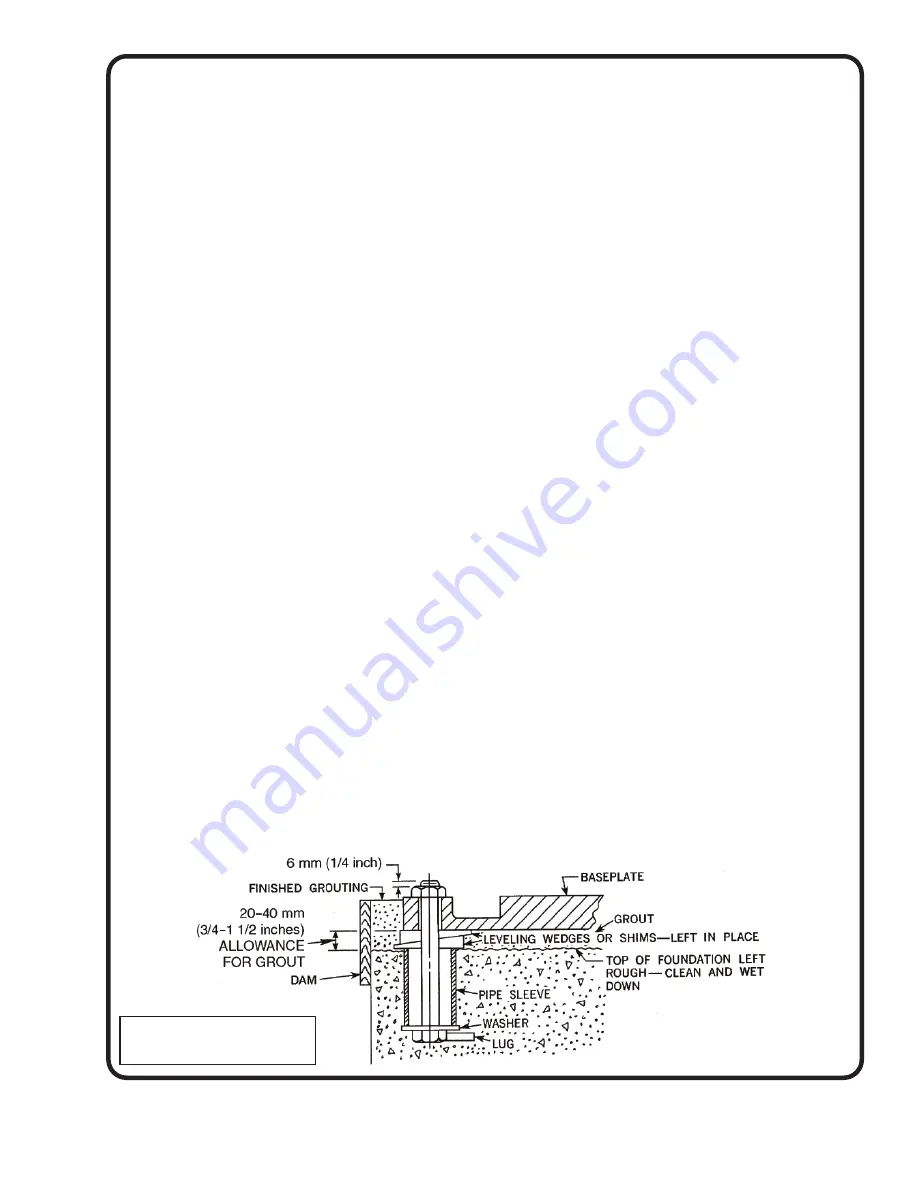
3
A - GENERAL INFORMATION
TO THE PURCHASER:
Congratulations! You are the owner of one of the fi nest
pumps on the market today. These pumps are products
engineered and manufactured of high quality components.
With years of pump building experience along with a
continuing quality assurance program combine to produce
a pump which will stand up to the toughest applications.
Check local codes and requirements before installation.
Servicing should be performed by knowledgeable pump
service contractors or authorized service stations.
RECEIVING:
Upon receiving the pump, it should be inspected for
damage or shortages. If damage has occurred, fi le a claim
immediately with the company that delivered the pump.
If the manual is removed from the crating, do not lose or
misplace.
STORAGE:
Short Term -
Pumps are manufactured for effi cient
performance following long inoperative periods in storage.
For best results, pumps can be retained in storage, as
factory assembled, in a dry atmosphere with constant
temperatures for up to six (6) months.
Long Term -
Any length of time exceeding six (6) months,
but not more than twenty four (24) months. The units
should be stored in a temperature controlled area, a roofed
over walled enclosure that provides protection from the
elements (rain, snow, wind blown dust, etc..), and whose
temperature can be maintained b40 deg. F and
+120 deg. F. Pump should be stored in its original shipping
container and before initial start up, rotate impeller by hand
to assure seal and impeller rotate freely.
SERVICE CENTERS:
For the location of the nearest Deming Service Center,
check your Deming representative or Crane Pumps &
Systems Service Department in Piqua, Ohio, telephone
(937) 778-8947 or Crane Pumps & Systems Canada, Inc.,
Bramton, Ontario, (905) 457-6223.
B - BEFORE YOU BEGIN
Motor driven pumps are carefully aligned on sub-base
before shipment. However, after they are placed upon the
foundation and sub-base is bolted down, the alignment
must be rechecked and in MOST CASES it will be found
necessary to carefully realign the unit. Quite often a noisy
pump is due to pump and motor not being properly aligned.
IN SUCH CASES WE DISCLAIM ALL RESPONSIBILITY
FOR PROPER WORKING OF PUMP.
Pumps are normally furnished with standard stuffi ng box
construction as shown on page 5. Flushing type stuffi ng box,
or mechanical shaft seal on pages 5 and 6 can be furnished
in lieu of standard stuffi ng box.
The single shaft seal on page 5 is used for handling clear
liquids at temperatures below their boiling point or 212°F
(100°C) as recommended by the seal manufacturer. A
portion of this liquid is by-passed into the seal chamber
through the by-pass tube (127) to serve as a lubricant and
as a coolant. The by-pass from the pump discharge must be
minimum of 20 pounds pressure above the suction pressure
of the pump to insure proper operation of the seal.
The double shaft seal on page 6 is used when pumping
abrasive or non-lubricating liquids or liquids of excessive
temperature. If the discharge pressure ever exceeds 25
pounds, a sealing liquid at 15 to 20 pounds higher than
maximum discharge pressure must be circulated through
the seal chamber. Clear water under such pressure can be
used in most applications as a sealing liquid for lubrication
and cooling.
If the discharge pressure is constantly under 25 pounds and
the temperature is less than the boiling point of the liquid
being pumped or 212°F (100°C), then seal chamber can be
fi lled with a quality light weight ball bearing grease. A spring-
loaded compression type grease cup should be installed to
maintain pressure in the seal chamber.
C - INSTALLATION
1. A good rigid foundation must be provided for pump
base.
2. Place pumping unit on foundation with bolts, of the
proper size, imbedded in the concrete. A pipe sleeve,
about 2½” diameters larger than the bolt, should be
used to allow for fi nal positioning of the bolts. See
Figure 1.
Figure 1. Foundation Bolt
Location and Anchorage