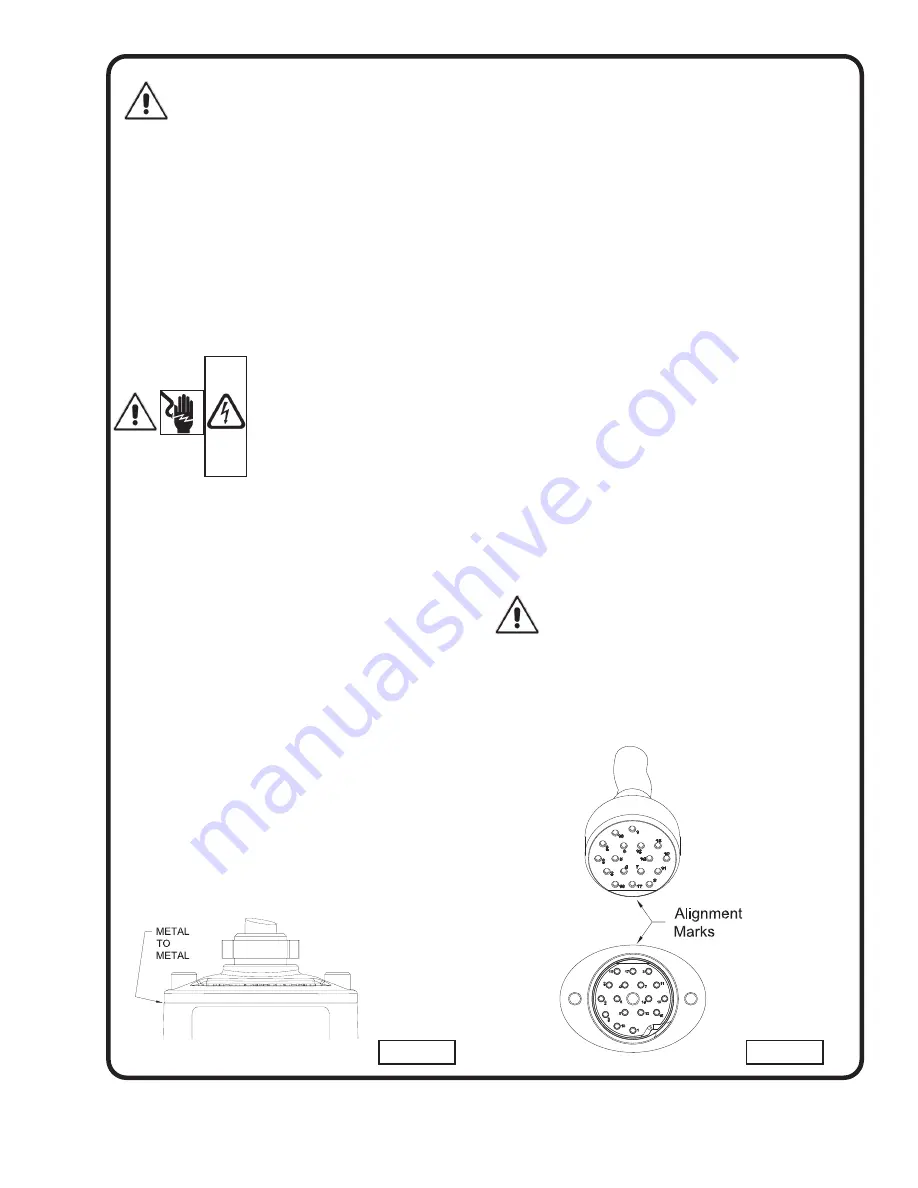
7
WARNING! Level control used within the hazardous
location, must be in an intrinsically safe control
circuit suitable for use in Class 1, Division 1, Groups
C&D, Hazardous Locations.
B-3) Liquid Level Controls:
It is recommended to use a liquid level control system that allows
the on and off point to be separated by at least twelve inches.
An additional set point (lag point) should be incorporated with an
alternator switching system for a duplex (two pump) station. A high
level alarm may be required to alert maintenance personnel that
there is a high water situation in the wet well should the output of
the pump station drop below the inflow rate. A low level cut off may
be installed to provide system shutdown if the main level control
system malfunctions. The off point should be positioned so that the
liquid level never drops below the minimum continuous duty point
for the pump shown in figure 1.
B-4.1) Electrical Connections:
WARNING! - All model pumps and
control panels must be properly
grounded per the NATIONAL
ELECTRIC CODE or CANADIAN
ELECTRIC CODE, State, Province and
local codes. Improper grounding voids
warranty.
B-4) Power/Control Cord:
The power/control cord used with pump has a patent pending
“quick disconnect” feature that allows the cord to be easily
attached and disconnected at the pump. The maximum amperage
rating for the cord is cast in the top of the cast stainless mounting
plate. The voltage connection for the motor is determined by the
cord assembly used. Low voltage cords (208 & 230 Volt) utilize
a molded quick connect plug that is colored black. High voltage
cords (460 & 575 Volt) utilize a molded quick connect cord that
is colored orange.
It is important to verify that the cord being
used is rated for the nameplate voltage and amperage rating
shown on the pump nameplate.
Refer to Chart on page 7.
No
internal wiring adjustments are necessary for dual and tri-voltage
pumps. All jumper connections to set the proper voltage are made
by the cord plug itself.
A flat alignment mark is molded into the plug and mating socket on
the pump. These should be used as a visual indication as to the
correct orientation of the plug. Insert the plug into the pump and
install the two 12 mm socket head cap screws into the clamping
plate. Slowly tighten the two screws alternating back and forth until
the clamping plate is drawn down flush to the top of the cord boss
on the pump. The two screws should be torqued until the plate is
down to a point where
metal to metal
contact is made between
the stainless steel plate and pump housing. (See Fig. 2)
The cord assembly mounted to the pump must not be modified
in any way except for shortening to a specific
application. Any
splice between the pump and the control panel must be
made in accordance with all applicable electric codes. It is
recommended that a junction box with seal fittings (if used)
be mounted outside the sump or be of at least
Nema 7
explosion proof construction if located within the wet well. A listed
water and vapor tight seal fitting
MUST
be used in conduit leaving
the wet well to prevent moisture and gasses from reaching the
control panel. Prior to installation, the pump power cable should
be inspected for nicks or damage. If damaged, the cord should be
replaced before installation.
CORD CLAMPING PLATE SHOULD BE DRAWN METAL
TO METAL (50FT/LBS BOLT TORQUE). IF A GAP EXISTS
CONTINUE TO TIGHTEN BOLTS. DO NOT USE ANY TYPE OF
SEALANT OR GREASE ON THE CORD ENTRY.
DO NOT USE THE POWER CORD TO LIFT PUMP.
B-4.1) Electrical Connections:
When the electrical connections are made, the lead wires from the
power cable should be stripped so that the ground wire is at least
two inches longer than the power leads. This will ensure that if the
cable is inadvertently pulled out of the connection point, the ground
wire will be the last lead to break the circuit.
B-4.2) Wire Size:
If additional cable is required consult a qualified electrician for
proper wire size. Voltage drop due to wire resistance between the
pump and power connection point should be limited to 3%
when additional cable is added.
WARRANTY NOTE:
Both the temperature sensor and moisture detection
system must be connected to the motor circuitry
such that the motor will be de-energized or sound
alarm if excessive motor temperatures are reached
and/or if water is detected in the seal chamber and/or
motor chamber. Failure to have the above mentioned
systems installed and operative, nullifies warranty.
FIGURE 2b
FIGURE 2a