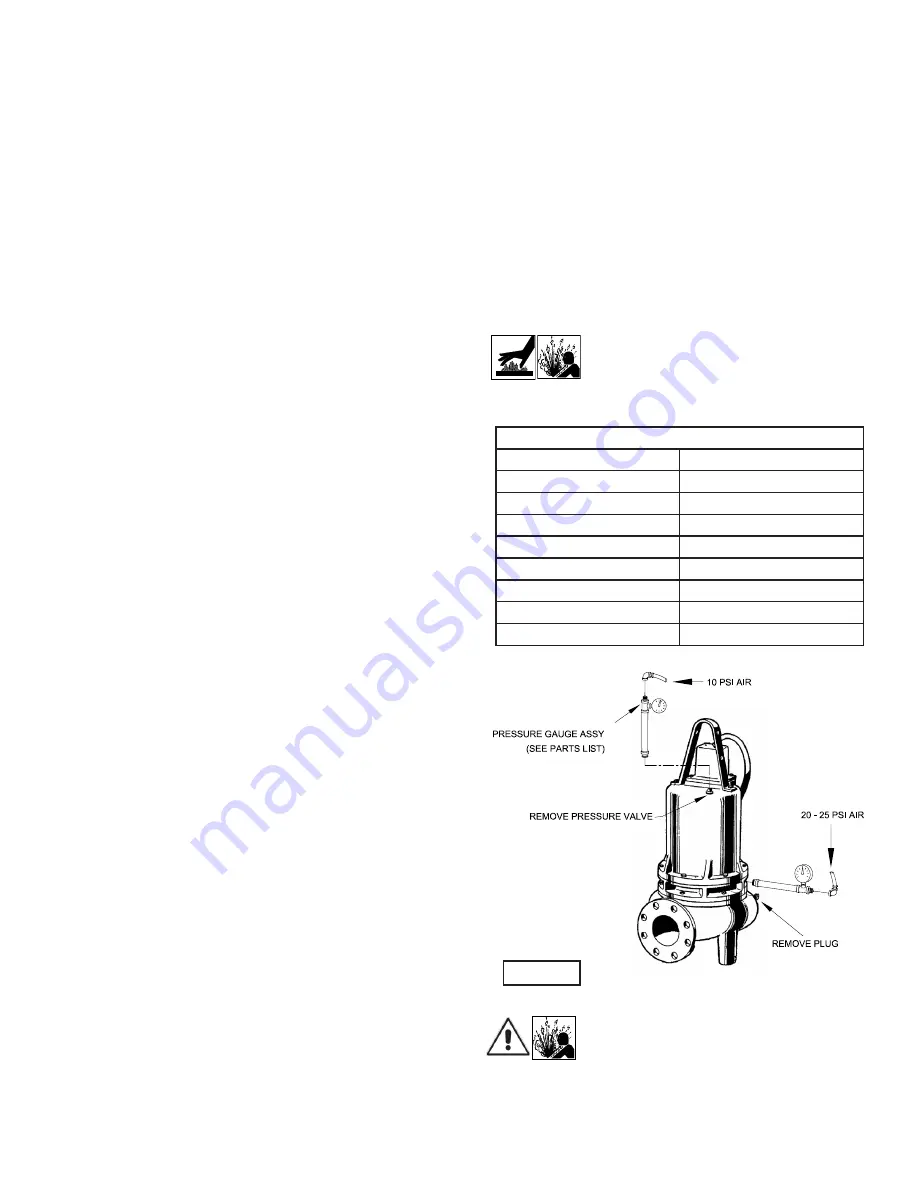
8
SECTION E: PREVENTATIVE MAINTENANCE
As the motor is oil filled, no lubrication or other maintenance
is required, and generally Crane Pumps & Systems will give
very reliable service and can be expected to operate for
years on normal sewage pumping without failing. However
as with any mechanical piece of equipment a preventive
maintenance program is recommended and suggested to
include the following checks:
1) Inspect motor and seal chambers for oil level and
contamination and repair as required per section F-1.
2) Inspect impeller and body for excessive build-up or
clogging and repair as required per section F-2.
3) Inspect motor and bearings and replace as required per
section F-3.
4) Inspect seal and diaphragm for wear or leakage
and repair as required per section F-4.
SECTION F: SERVICE AND REPAIR
NOTE:
All item numbers in ( ) refer to Figures 10 4SEV-L
Pumps.
F-1) Lubrication:
Anytime the pump is removed from operation the cooling oil
in the motor housing (2) and seal chamber, must be checked
visually for oil level and contamination.
F-1.1) Checking Oil:
Motor Housing -
To check oil, set unit upright. Remove cap
screws (6), lift conduit box assembly (10) from motor housing
(2) but
DO NOT
disconnect conduit box wiring from motor
leads. With a flashlight, visually inspect the oil in the motor
housing (2) to make sure it is clean, clear and that oil level is
above all internal componentry.
Seal Chamber -
Place pump on its side with pipe plug (22)
downward, remove pipe plug (22) and drain oil from the seal
chamber. If the oil is found to contain considerable water
or other contamination or little oil drains out, the shaft seal
(46) and diaphragm (32) should be inspected and replaced if
required.
F-1.2) Testing Oil:
1. Place pump on it’s side, remove cap screws (6),
lift conduit box assembly (10) from motor housing
(2) and drain oil into a clean, dry container. In
separate container drain seal chamber by
removing pipe plug (22).
2. Check oil for contamination using an oil tester with
a range to 30 Kilovolts breakdown.
3. If oil is found to be clean and uncontaminated
(measure above 15 KV. breakdown), refill the
motor housing and seal chamber as per section
F-1.3.
4. If oil is found to be dirty or contaminated (or
measures below 15 KV. breakdown), the the pump
must be carefully inspected for leaks at the shaft seal
(46), conduit box assembly (10), diaphragm
(32), O-ring (42), pipe plug (22) and pressure
valve (5) before refilling with oil. To locate the leak,
perform a pressure test as per section F-1.4. After
leak is repaired, refill with new oil as
per section F-1.3.
F-1.3) Replacing Oil:
Motor Housing -
Drain all oil from motor housing and
dispose of properly. Refill with (see parts list for amount) new
cooling oil as per Table 1. An air space must remain in the
top of the motor housing to compensate for oil expansion
(see Fig. 10). Set unit upright and fill only until the motor, as
viewed through the conduit box opening, is just covered and
no more. Reassemble the O-ring (11), conduit box assembly
(10) and cap screws (6), apply thread locking compound
to each cap screw (6) thread before installing. Torque cap
screws (6) to 15 ft., lb.
Seal Chamber -
Refill chamber completely full with new
cooling oil per Table 1 or reuse the uncontaminated oil. (See
parts list for amount.)
Important! - Do not overfill oil! Overfilling
of motor housing with oil can create
excessive and dangerous hydraulic
pressure which can destroy the pump
and create a hazard. Overfilling oil voids
warranty.
TABLE 1 - COOLING OIL - Dielectric
SUPPLIER
GRADE
BP
Enerpar SE100
Conoco
Pale Paraffin 22
Mobile
D.T.E. Oil Light
G & G Oil
Circulating 22
Imperial Oil
Voltesso-35
Shell Canada
Transformer-10
Texaco
Diala-Oil-AX
Woco
Premium 100
Caution! - Pressure builds up extremely
fast, increase pressure by “tapping” air
nozzle. Too much pressure will damage
seal. Do Not exceed 10 P.S.I. in motor
housing & 20-25 P.S.I. in seal chamber.
FIGURE 2
Summary of Contents for Barnes 084605
Page 15: ...15 FIGURE 10 4SEV Pump Series ...