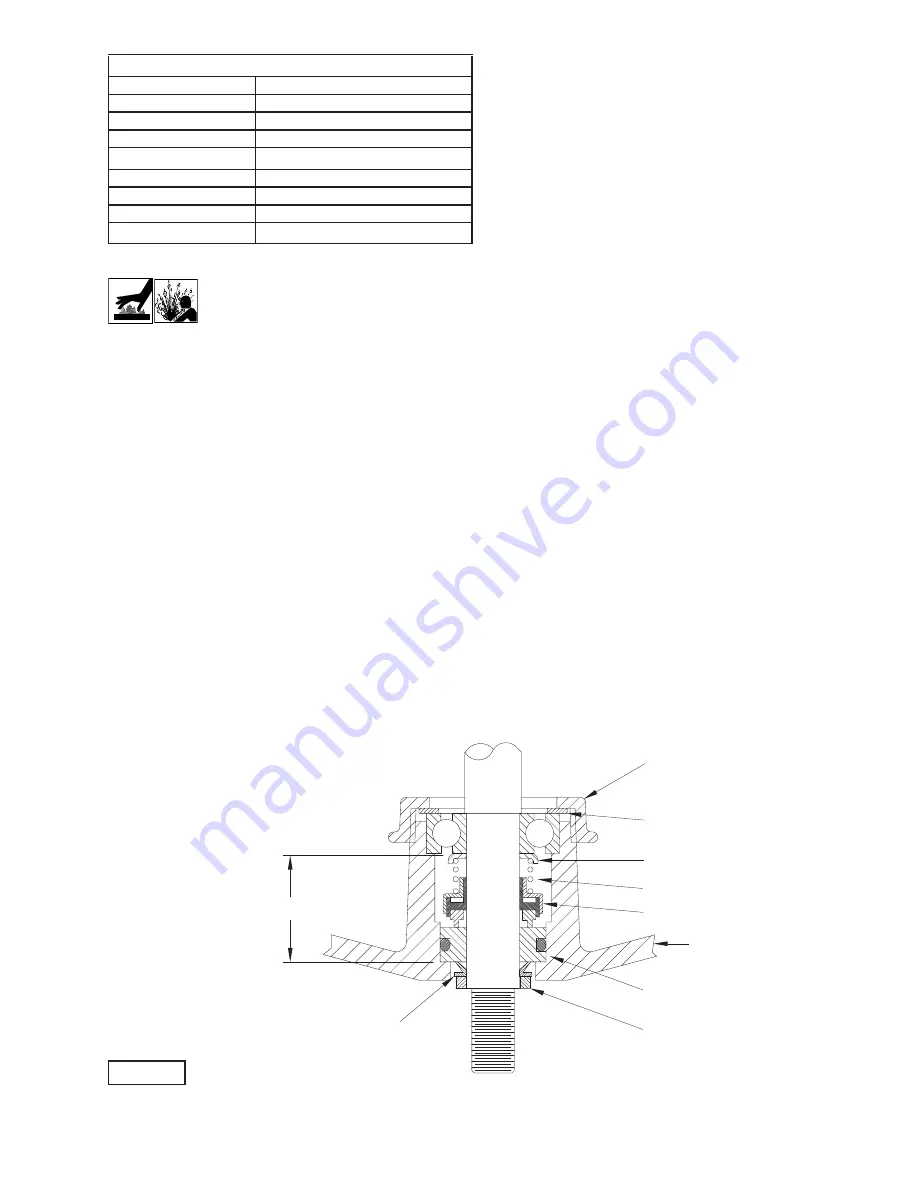
5
TABLE 1 - COOLING OIL - Dielectric
SUPPLIER
GRADE
Sohio / Standard
SE 40, Energol HL22 or HL32
Shell
Turbo Oil 32
Texaco
Rando HD32, 522
Sun Petroleum
Supar 110, Sunvis 816WR, 911 or 916
Mobile
D.T.E. Oil Light or Rubrex 200
G&G
Circu Oil 22
Allegheny Petroleum
Altrapar 22
Woco
Premium 100
Caution! - Pressure builds up extremely
fast, increase pressure by “tapping” air
nozzle. Too much pressure will damage
seal. Do Not exceed 10 P.S.I. in motor
housing.
2) Impeller and Volute Service:
2.1) Disassembly and Inspection:
To clean out volute, disconnect power, remove hex nuts and
lockwashers, vertically lift motor and seal assembly from
volute. Clean out body if necessary. Clean and examine
impeller for pitting or wear, replace if required. Inspect square
ring and replace if cut or damaged. If impeller requires
replacing, remove jam nut and washer, by placing a fl at
screwdriver in the slot of the end of the shaft to hold the shaft
stationary while unscrewing the impeller. Once impeller is
removed, remove pull washer and exclusion seal if damaged
or cut.
2.2) Reassembly:
Position exclusion seal on shaft until it seats against the
stationary portion of seal. Place pull washer on shaft until it
seats against exclusion seal. To install impeller, apply a thin
fi lm of oil to motor shaft and slide impeller straight onto shaft,
keeping keyways lined up, drive key into keyway. Locate
washer, apply Loctite to shaft threads, thread hex nut to shaft
and torque to 40 ft. lbs. Rotate impeller to check for binding.
Position o-ring on volute fl ange and position impeller and
motor housing assembly over studs and onto volute. Apply
thread locking compound to each stud. Thread nut onto studs
and torque to 20 ft. lbs. Check for free rotation of motor and
impeller.
3) Motor, Bearing and Seal Service
3.1) Disassembly and Inspection:
To examine or replace the motor, bearing and shaft seal,
disassemble volute and impeller as outlined in paragraph 2.1.
Drain oil from motor as outlined in paragraph 1.2.
Position unit upright, using blocks to avoid resting unit on
shaft. After removal of cord motor housing remove cable
lead wires from motor lead wires and temperature sensor
wires (if equipped) from sensor cord, by disconnecting wire
connectors. Also disconnect ground screw from motor.
The wiring connections should be noted to insure correct
connections when reassembling.
Motor -
Remove the motor bolts and lift motor stator from
motor rotor and seal plate. Unscrew conduit bushing from
seal plate and lift motor rotor, shaft, bearing, rotating portion
of seal, washer and conduit bushing from seal plate.
Inspect windings for shorts and check resistance values.
Check rotor for wear, if rotor or the stator windings are
defective, the complete motor must be replaced. To test
the temperature sensor (if equipped), check the continuity
between the black and white wires. If found to be defective
contact a motor service station or Barnes Service
Department. Check motor capacitor on single phase units
and replace if defective.
FIGURE 2
SEAL ASSEMBLY
RETAINING RING
SEAL PLATE
SPRING
ROTATING MEMBER
STATIONARY
CONDUIT BUSHING
WASHER
PULL WASHER
EXCLUSION SEAL
MOTOR END
(INBOARD END)
PUMP END
(OUTBOARD END)