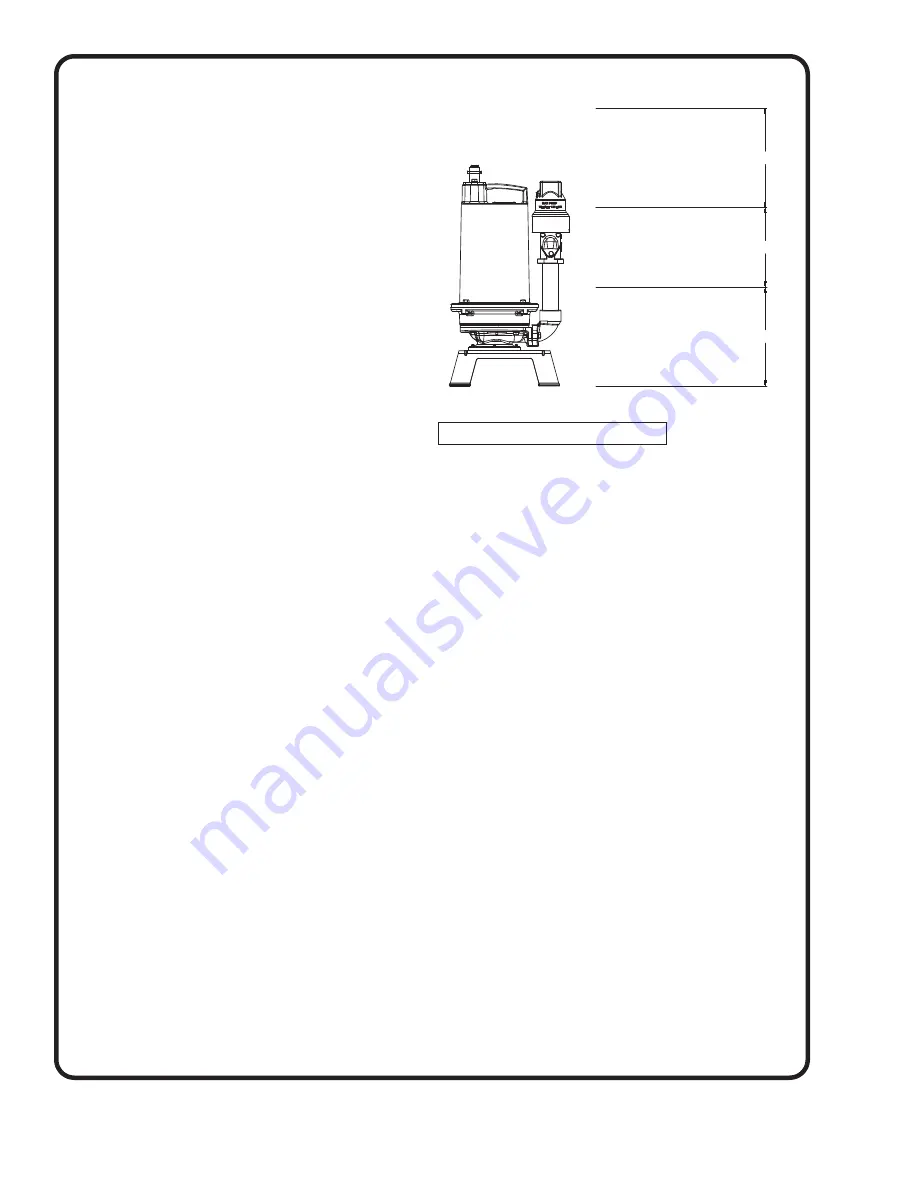
6
RECEIVING/UNPACKING:
Upon receiving the pump, it should be inspected for dam-
age or shortages. If damage has occurred, file a claim
immediately with the company that delivered the pump.
Unpack pump and record pump serial and model number
before installing. If the manual is removed from the pack-
aging, do not lose or misplace.
STORAGE:
Short Term-
For best results, pumps can be retained in
storage, as factory assembled, in a dry atmosphere with
constant temperatures for up to six (6) months.
Long Term-
Any length of time exceeding six (6) months,
but not more than twenty-four (24) months. The units
should be stored in a temperature controlled area, a roofed
over walled enclosure that provides protection from the
elements (rain, snow, wind-blown dust, etc.), and whose
temperature can be maintained between 4°C and 49°C.
If extended high humidity is expected to be a problem, all
exposed parts should be inspected before storage and all
surfaces that have the paint scratched, damaged, or worn
should be recoated with a air dry enamel paint. All surfaces
should then be sprayed with a rust-inhibiting oil.
Pump should be stored in its original shipping container.
On initial start up, rotate impeller by hand to assure seal
and impeller rotate freely. If it is required that the pump be
installed and tested before the long term storage begins,
such installation will be allowed provided:
1.) The pump is not installed under water for more than
one (1) month.
2.) Immediately upon satisfactory completion of the
test, the pump is removed, thoroughly dried,
repacked in the original shipping container, and
placed in a temperature controlled storage area.
3.) Before placing pump into service, pump should be
brought to operational temperature range.
Excessive or direct heating or cooling should NOT
be used.
OPERATION TEMPERATURE RANGE:
2ºC to 40ºC.
SERVICE CENTERS:
For the location of the nearest Barnes Service Center, check
your Barnes representative:
INSTALLATION:
Location -
The pump is designed to fit into your basin by
being mounted on a pump base.
THIS PUMP MUST BE
INSTALLED WITH A MINIMUM OF 75MM AND A
MAXIMUM OF 115MM OF CLEARANCE UNDER THE
PUMP FOR THE ENTRANCE OF SEWAGE SOLIDS.
Discharge -
Assemble discharge piping or hose assembly
(whichever is required by your application), to the pump.
Discharge piping should be as short as possible. Both a
check valve and a shut-off valve are required for each pump
being used. The check valve is used to prevent backflow
into the sump. Excessive backflow can cause flooding and/
or damage to the pump. The shut-off valve is used to stop
system flow during pump or check valve servicing.
Package Systems-
Refer to manual supplied with basin
package system.
ELECTRICAL CONNECTIONS:
Pump Cables -
The cord assembly mounted to the pump
must
NOT
be modified in any way except for shortening
to a specific application. Any splice between the pump
and the control panel must be made in accordance with
the National Electric Code or the Canadian Electric
Code and all applicable state, province and local electric
codes. It is recommended that a junction box, be mounted
outside the sump or be of at least Nema 4 (EEMAC-4)
construction if located within the wet well.
DO NOT USE
THE POWER OR CONTROL CABLES TO LIFT PUMP!
Overload Protection -
The type of in-winding overload
protector used is referred to as an inherent overheating
protector and operates on the combined effect of
temperature and current. This means that the overload
protector will trip out and shut the pump off if the windings
become too hot, or the load current becomes too high.
It will then automatically reset and start the pump after
the motor cools to a safe temperature. In the event
of an overload, the source of this condition should be
determined and rectified immediately.
DO NOT LET THE
PUMP CYCLE OR RUN IF AN OVERLOAD CONDITION
OCCURS !
·
·
·
·
10" (254)
8" (203)
10" (254)
STANDARD "ALARM"
POSITION
BOTTOM OF BASIN
PUMP "ON"
POSITION
PUMP "OFF"
POSITION
FIGURE 2 - Normal Operating Points
Summary of Contents for Barnes PGPT Series
Page 8: ...8 FIGURE 5 WIRING DIAGRAM ...
Page 12: ...Notes ...