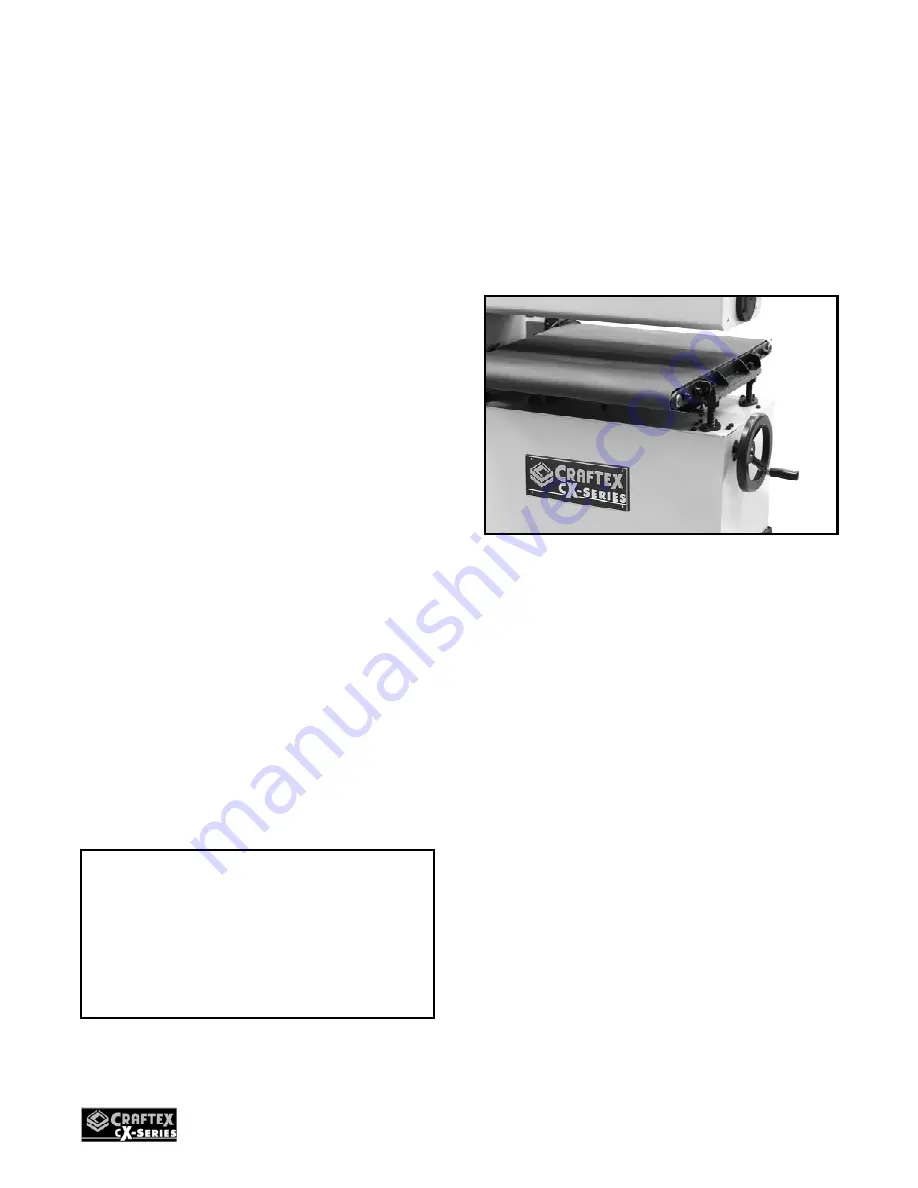
10
WORK-PIECE INSPECTION
Before cutting the work-piece, make sure to
inspect it for nails, staples, small pieces of
stone or metal and any other object which
is dangerous to come in contact with the
sanding paper / sanding drum.
If the wood contains any of these objects
and it comes in contact with the sanding
drum, the object might fly and hit the
operator or seriously damage the sander.
For a safe cutting method always inspect
your work-piece carefully before sanding
and always wear eye protection.
Some woods with excessive twisting or
wrapping are un-stable while sanding. This
situation can be dangerous, because during
operation the work-piece can move
unexpectedly which can either damage the
machine or hurt the operator.
If the wood is slightly cupped, make sure
the cupped face of the wood is held against
the conveyor belt. If the bowled side of the
work-piece is not held against the conveyor
belt, there will be a great possibility that the
work-piece move unexpectedly while
sanding, and cause kickback or injury to the
operator.
Some stock with large knots can damage
the sanding paper / sanding drum and wet
stock will give a poor result.
DEPTH OF CUT
One full turn of the height adjustment hand
wheel anti-clockwise, will give 1/64" depth
of cut. However the correct depth of cut
when surface sanding depends on many
variables, such as the hardness of the
wood, the width of the work-piece and the
feed rate.
Figure-6 Table height adjustment hand
wheel
To set the depth of cut:
Rotate the table height hand wheel and
allow a gap between the work-piece and
the sanding drum.
Turn ON the feed belt and the sanding
drum and feed the work-piece into the
sander.
Raise the feed belt slowly until the work-
piece makes light contact with the sanding
drums.
After a few passes, turn the hand wheel to
a 1/4 turn for a 1/64" depth of cut
(maximum depth of cut).
WARNING!
If the work-piece is excessively wrapped,
it is dangerous to cut because it is
unstable and will cause kick back,
damaging the machine and causing
injury to the operator. Do not cut these
work-piece with excessive wrapping.
Summary of Contents for CX509
Page 1: ...MODEL CX509 18 OPEN END DRUM SANDER USER MANUAL Version 1 0 ...
Page 18: ...18 PARTS DIAGRAM ...
Page 19: ...19 PARTS LIST ...
Page 20: ...20 ...
Page 21: ...21 ...
Page 22: ...22 ...