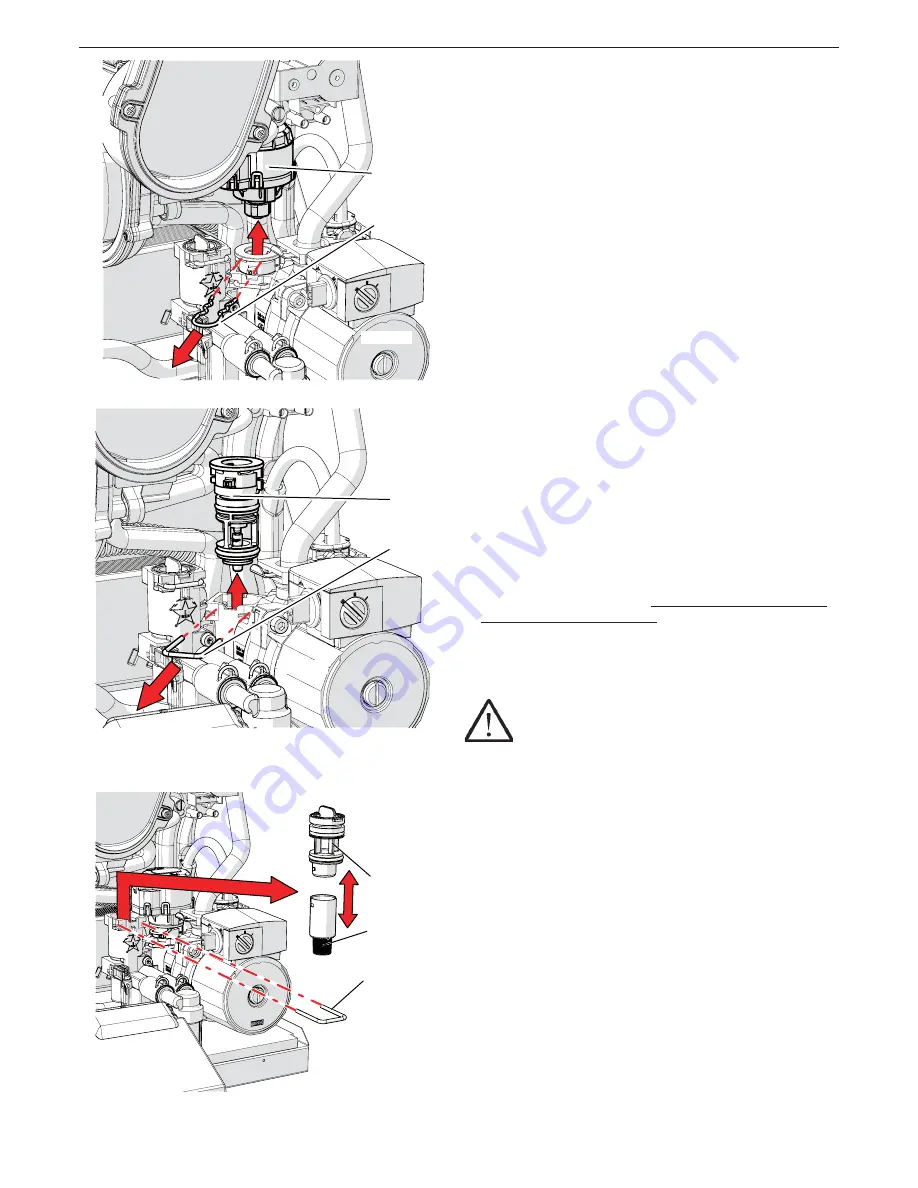
60
MYDENS
COSMOGAS
8 - MAINTENANCE
8.11 - Removing the diverter
valve servo-motor
Proceed as follows, making reference to figure 8.11:
1.- access the internal components of the appliance
following chapter 8.2;
2.- remove the air manifold (detail “C” in figure 6.2) rotating
it towards the outside of the boiler and then pulling it
towards the right (see figure 6.2);
3.- slide the drive bar “A” in 8.11 out;
4.- extract the servo-motor “B” in figure 8.11 upwards.
8.12 - Removing the diverter valve
The diverter valve (detail “47” in figure 3.1) switches
over the flow of water produced from the primary heat
exchanger to the central heating circuit or to the secondary
heat exchanger for the production of d.h.w. If it has to be
replaced, proceed as follows (refer to figure 8.12):
1.- remove the diverter valve servo-motor following chapter
8.11;
2.- empty the central heating circuit, following the procedure
in chapter 8.16;
3.- slide the drive bar “D” out;
4.- slide the diverter valve “E” upwards.
8.13 - Removing the flow meter
The flow meter is used to measure the water flow rate of
the domestic hot water. If it has to be replaced, proceed as
follows (refer to figure 8.13):
1.- empty the domestic hot water circuit, following the
procedure in chapter 8.17;
2.- access the internal components of the appliance
following chapter 8.2;
3.- remove the spring “A”;
4.- extract the flow meter “B”,
paying attention to direction
for the correct re-positioning
at the end of maintenance;
5.- clean the filter “C” making sure to extract it from the
body of the flow meter “B” as indicated in the figure;
6.- wash the filter and re-mount everything in reverse order;
7.- during remounting, make sure the flow meter is
positioned correctly (step highlighted in point 4).
ATTENTION !!! This filter is intended as a
precaution only. A filter with greater capacity must be
installed outside the boiler, on the cold water inlet, as
specified in chapter 5.6.
Figure 8.11 - Removing the servo-motor
Figure 8.12 - Removing supply and return fittings
Figure 8.13 - Removing the flow meter
B
A
020002.01.031
E
D
020002.01.032
A
C
B
020002.01.033
Summary of Contents for MYDENS
Page 67: ...67 MYDENS COSMOGAS 8 MAINTENANCE...
Page 74: ......
Page 75: ......
Page 76: ...COSMOGAS s r l Via L da Vinci 16 47014 MELDOLA FC ITALY info cosmogas com www cosmogas com...