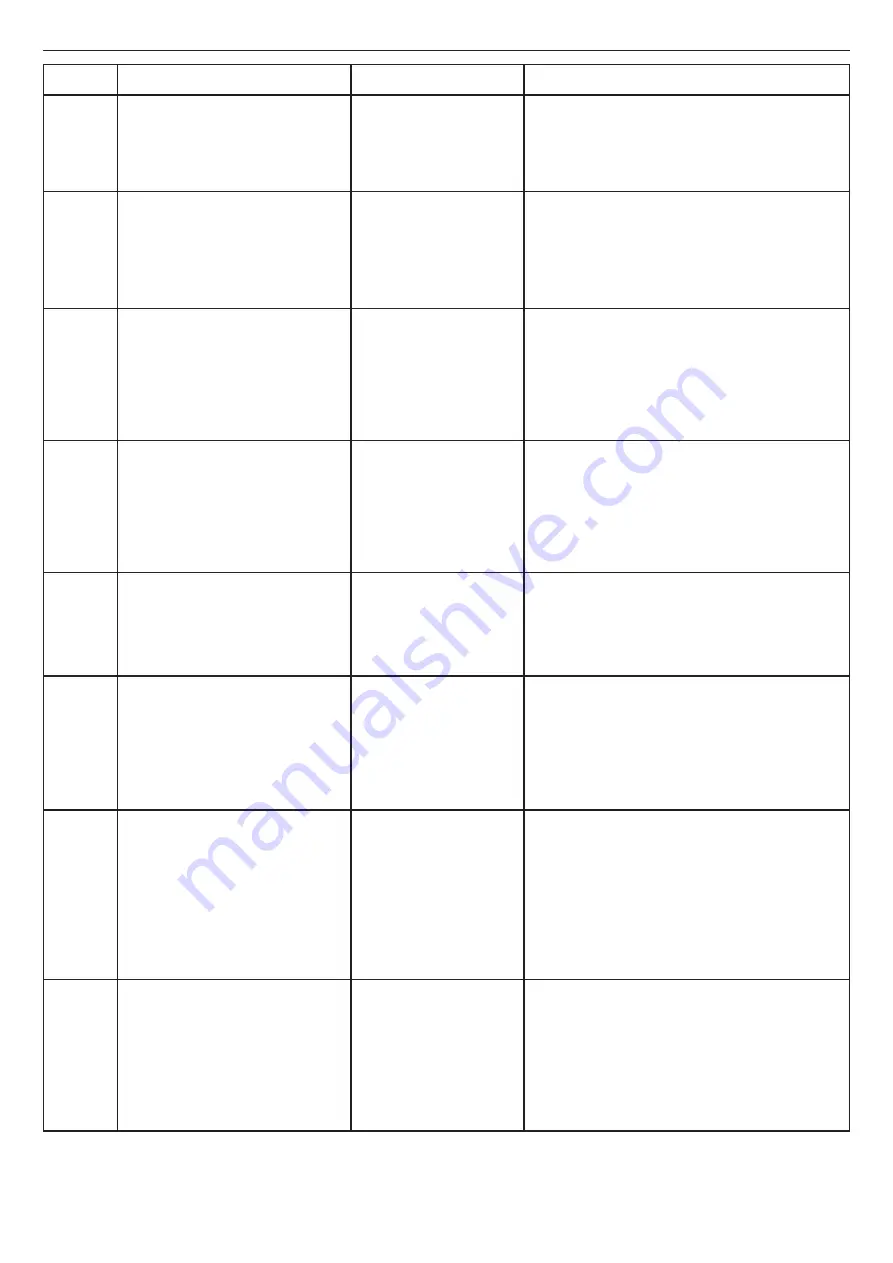
41
FRYO PI
COSMOGAS
8 - DIAGNOSTIC
Code
Description
Operation status
Possible causes and solutions
00 Eb
Water flow switch fault
Compressor stopped
If the water flow switch is “closed” with no flow, this
message will appear. We may be in the presence of an
external pump that is running when the internal pump is
off. Check that the water flow switch does not get stuck in
the “closed” state.
00 EC
Water flow too low
Compressor stopped
The too low flow rate message appears if protection “00
P7” trips 3 times in a given time. To reset it, remove the
voltage for 30 seconds and restore the power supply.
Check the hydraulic system, especially the filters. Check
the operating status of the pump.
00 P1
System 1 communication fault
System 1 stopped
Too much communication data lost. Check that the
connection wiring is intact and well connected. The cable
must be a maximum of 30 meters long. Check that there
are no disturbances in the vicinity of the unit. The unit
resets as soon as the problem disappears. Check that
the switches n ° 1, 2 and 8 on the gas side control board
are set to “OFF”.
00 P2
Communication failure between display
and gas side control board
System stopped
Too much communication data lost. Check that the
connection wiring is intact and well connected. Verify
that the display is not installed very far away or in a high
voltage conduit. The unit resets as soon as the problem
disappears. Check that the switches n ° 1, 2 and 8 on the
gas side control board are set to “OFF”.
00 P3
Communication failure with display
The appliance will stop
Too much communication data lost. Check that the
connection wiring is intact and well connected. The cable
must be a maximum of 30 meters long. Check that there
are no disturbances in the vicinity of the unit. The unit
resets as soon as the problem disappears.
00 P4
Communication failure with Master
appliance
The appliance stops only
when the external Master
is connected and activated,
otherwise the unit continues
to work with the current
settings.
This fault appears only if there is an external Master unit
connected to the appliance that controls it via Modbus.
Too much data lost. Check that the connection wiring is
intact and well connected. The cable must be maximum
30 meters long. Check that there are no disturbances in
the vicinity of the unit. The appliance resets as soon as
the problem disappears.
00 P5
Antifreeze function in cooling
Compressor stopped. If the
message does not disappear
within 3 minutes, it means
that it occurred 3 times within
a certain time. In this case,
disconnect the power for
30 seconds and restore the
power supply to restore the
system.
Check that the cooling temperature is not too low (section
7.2.4). Check that the water flow rate is not too low.
Check the status of the filters. Check that the refrigerant
is sufficient through the pressure on the evaporator (sec
-
tion 7.3, Parameter “19”). Check that the room tempera
-
ture is not below 15 ° C.
00 P6
Antifreeze function in cooling system 1
Compressor 1 speed redu-
ced to 0. If the message does
not disappear within 3 minu
-
tes, it means that it occurred
3 times within a certain time.
In this case, disconnect
the power and restore it to
restore the system.
Check that the cooling temperature is not too low. Check
that the water flow rate is not too low. Check the status of
the filters. Check that the refrigerant is sufficient through
the pressure on the evaporator. Check that the ambient
temperature is not below 15 ° C.
Summary of Contents for FRYO 6PI
Page 2: ......
Page 58: ...58 FRYO PI COSMOGAS...
Page 59: ...59 FRYO PI COSMOGAS...
Page 60: ...COSMOGAS s r l Via L da Vinci 16 47014 MELDOLA FC ITALY info cosmogas com www cosmogas com...