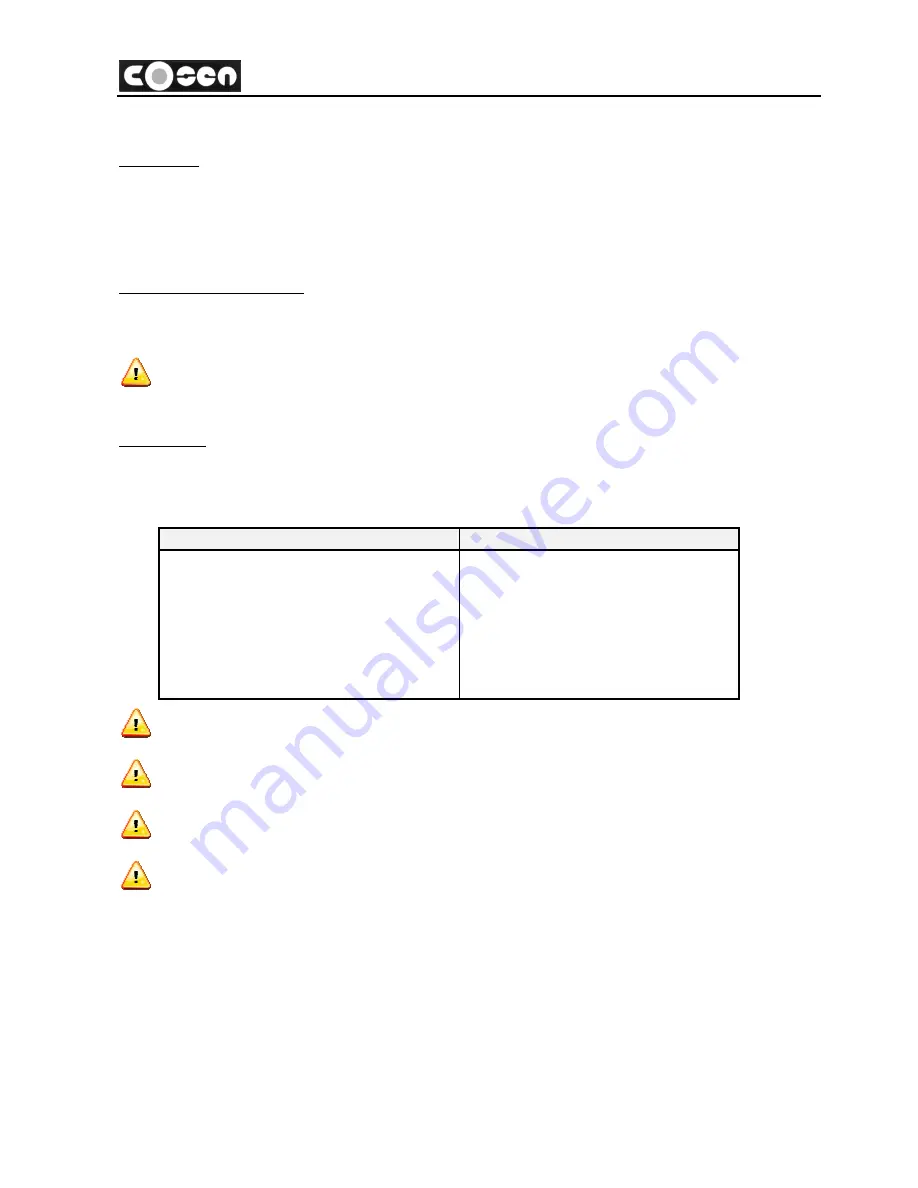
OPERATING INSTRUCTION
SECTION 4
4-2
Wet cutting
If you choose dry cutting or low-speed cutting, the chips may accumulate in machine parts and may
cause operation failure or insulation malfunction. We suggest you choose wet cutting to avoid machine
damage.
Cutting unknown materials
Before cutting an unknown material, consult the material supplier, burn a small amount of chips from
the material in a safe place, or follow any other procedure to check if the material is flammable.
Caution: Never take your eyes off the machine while in operation.
Cutting fluid
For cooling and lubrication purpose, we recommend you use water-soluble cutting fluids. The
following table lists out its pros and cons for your reference.
Pro
Con
Have a high cooling effect
Not flammable
Economical
Does not require cleaning of the cut
products
Remove machine paint
Lose its rust protection effect if
deteriorated
Tend to create foam
Subject to decay
Decline in performance, depending on
the quality of the water used for
dilution
Note: Never use water as your coolant.
Note: Always add coolant into water for better mix result.
Note: Consult your coolant supplier for bandsaw use regarding coolant type and mix ratio.
Note: Before starting a cutting job, make sure there is sufficient amount of coolant in the tank.
Check the fluid level through the sight gauge. Please refer to machine specifications in this manual
(Section 2) for tank capacity.
Summary of Contents for C-325NC
Page 3: ......
Page 7: ......
Page 8: ......
Page 9: ......
Page 10: ......
Page 11: ......
Page 12: ......
Page 13: ......
Page 14: ......
Page 15: ......
Page 16: ......
Page 26: ...Section 3 MOVING AND STALLATION ...
Page 27: ......
Page 28: ......
Page 29: ......
Page 30: ......
Page 31: ......
Page 32: ......
Page 33: ......
Page 34: ......
Page 35: ......
Page 36: ......
Page 37: ......
Page 69: ...Section 5 ELECTRICAL SYSTEM ...
Page 71: ...ELECTRICAL SYSTEM Section 5 5 2 Fig 5 1 control panel layout ...
Page 72: ...ELECTRICAL SYSTEM Section 5 5 3 Fig 5 2 circuit board layout ...
Page 73: ...ELECTRICAL SYSTEM Section 5 5 4 Fig 5 3 power supply layout ...
Page 74: ...ELECTRICAL SYSTEM Section 5 5 5 Fig 5 4 1 PLC I O layout ...
Page 75: ......
Page 77: ...HYDRAULIC SYSTEM Section 6 6 2 Fig 6 1 HYDRAULIC CIRCULIC ...
Page 78: ......
Page 79: ......
Page 80: ......
Page 81: ......
Page 82: ......
Page 83: ......
Page 84: ......
Page 85: ......
Page 86: ......
Page 87: ......
Page 88: ......
Page 89: ......
Page 90: ......
Page 91: ......
Page 92: ......
Page 93: ......
Page 94: ......
Page 95: ......
Page 96: ......
Page 97: ...Section 10 PART LIST ...
Page 98: ...10 1 ...
Page 99: ...10 2 ...
Page 100: ...10 3 ...
Page 101: ...10 4 ...
Page 102: ...10 5 ...
Page 103: ...10 6 ...
Page 104: ...10 7 ...
Page 105: ...10 8 ...
Page 106: ...10 9 ...
Page 107: ...10 10 ...
Page 108: ...10 11 ...
Page 109: ...10 12 ...
Page 110: ......