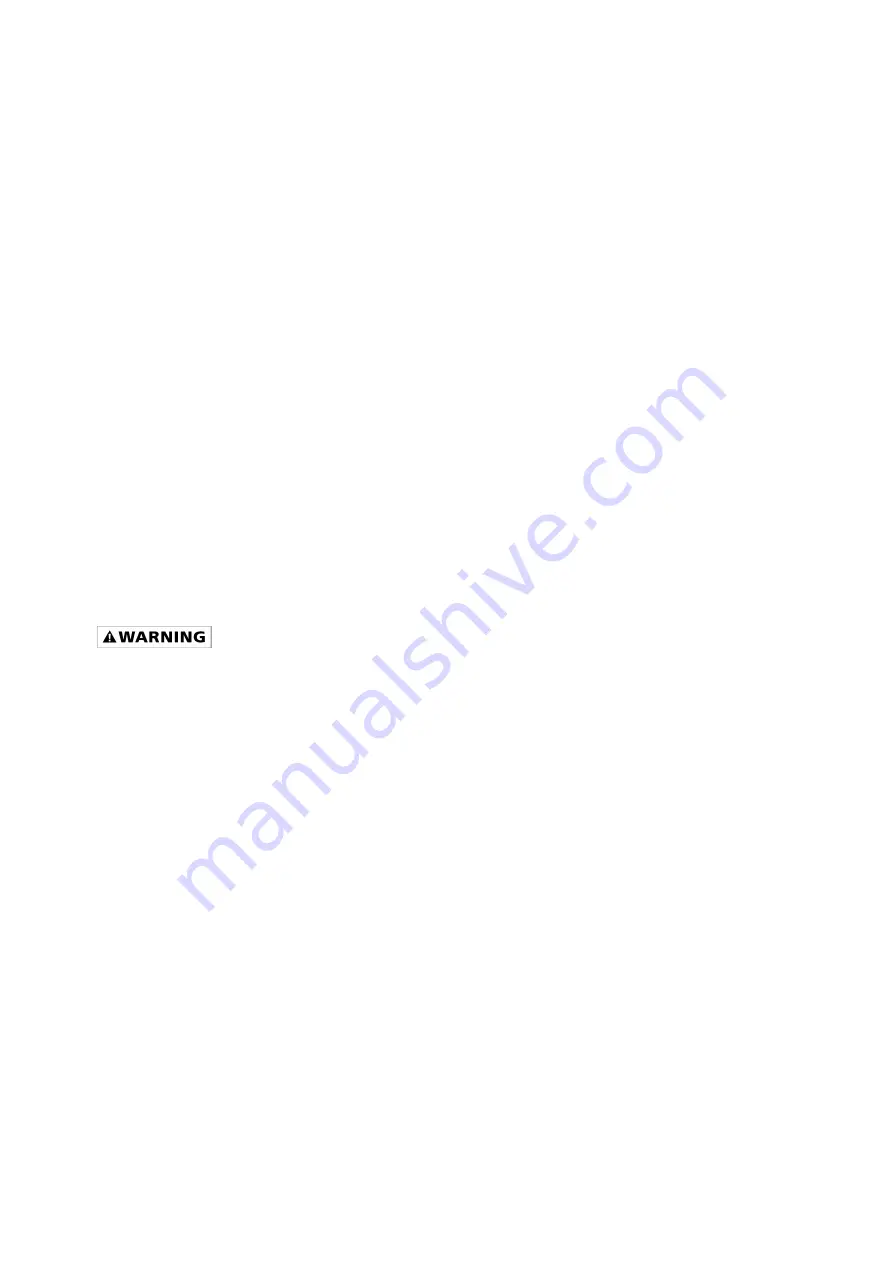
Page of 44
9
POWER CORD AND PLUG
Plug this unit into a 230V, 50-amp circuit breaker power supply when operating on 230V. If running
on 120V power using the supplied 120V power cord adapter, plug this unit into a 120V, 20-amp
circuit breaker power supply.
INERT GAS REGULATOR AND HOSE
The Inert Gas Regulator installs on the shielding gas cylinder for MIG welding with solid wires. The
regulator controls the compressed gas and allows you to adjust the flow rate of the gas. The gas hose
connects to the regulator/flow gauge and delivers the shielding gas from the shielding gas bottle to the
welder.
MULTI-FUNCTION ADJUSTMENT/SELECTOR KNOB
The Multi-Function Adjustment/Selector Knob is used by the operator to interact with the LCD Synergic
Control. It is used for the selection and adjustment of welding processes, materials, and selections within
the LCD Synergic Control screen.
WELDING VOLTAGE CONTROL
The voltage control allows the operator to make manual voltage adjustments to the LCD Synergic
programming.
GROUND CABLE AND CLAMP
The ground cable and clamp are attached to the work piece to complete the circuit allowing the flow of
current needed to weld.
INSTALLATION
Electrical Shock
•
High voltage danger from power source! Consult a qualified electrician for proper
installation of receptacle. This welder must be grounded while in use to protect the
operator from electrical shock.
•
Do not remove grounding prong or alter the plug in any way. Use only the supplied
adapter between the plasma cutter's power cord and the power source receptacle. Make
sure the POWER switch is
OFF when connecting your welder’s power cord directly to a
properly grounded 230 VAC, 60 HZ, Single Phase, 50 Amp input power supply. Or, when
using the supplied 120V adapter, connect the 120V Adapter to a properly grounded 120V,
20 Amp input power supply.
1. POWER REQUIREMENT 230V - AC single phase 230V (220-240V) 50/60 HZ fused with a
50-amp time delayed fuse or circuit breaker is required. DO NOT OPERATE THIS UNIT if the
ACTUAL power source voltage is less than 215 volts AC or greater than 240 volts AC.
2. POWER REQUIREMENT 120V - AC single phase 120V (110-130V) 50/60 HZ fused with a
20-amp time delayed fuse or circuit breaker is required. DO NOT OPERATE THIS UNIT if the
ACTUAL power source voltage is less than 110 volts AC or greater than 130 volts AC.
2.1
When connecting this unit to 120V power, connect the 120V adapter cord to the
power cord pigtail that is attached to the machine.
3. EXTENSION CORD - We do not recommend an extension cord because of the voltage drop
produced. This drop, in voltage can affect the performance of the welder. If you need to use an
extension cord, check with a qualified electrician and your local electrical codes for your specific
area.