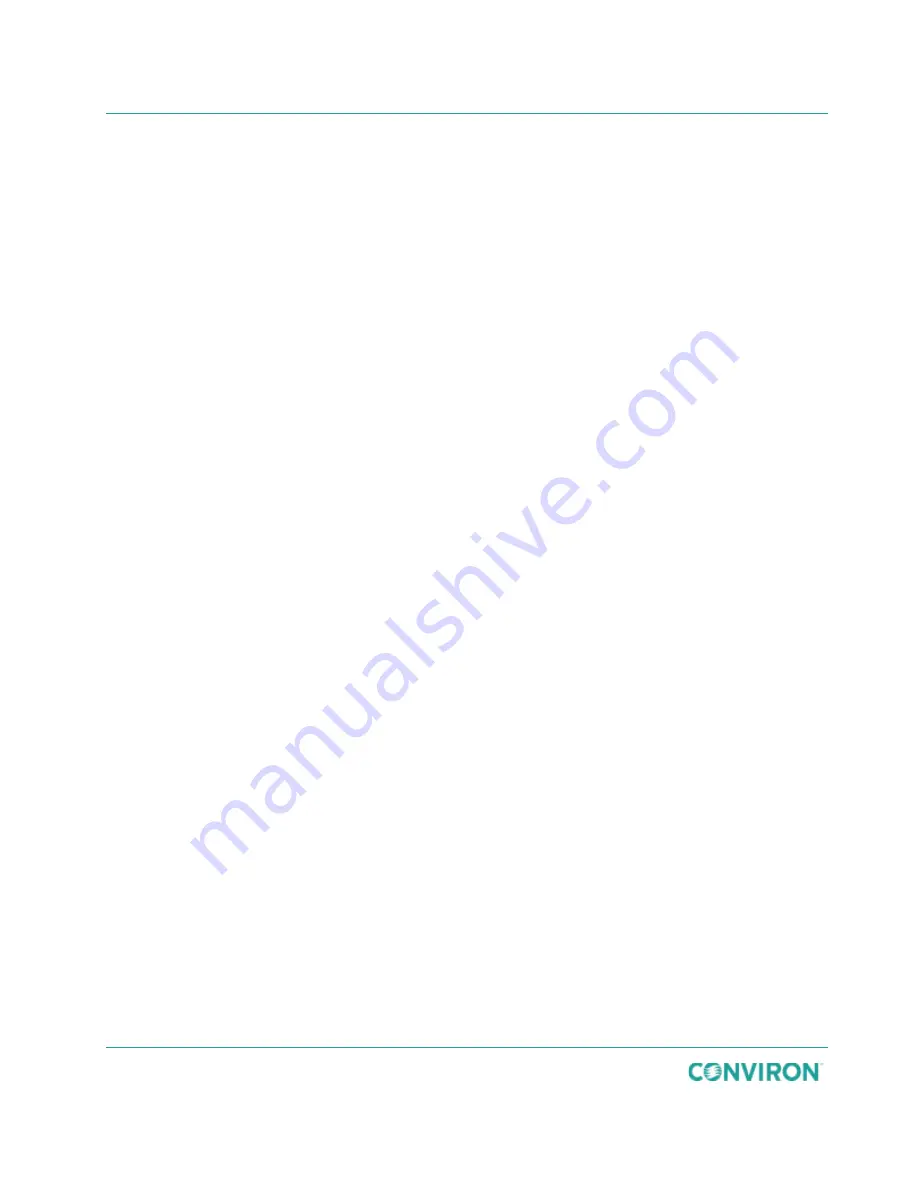
iv September 10, 2020 | 296742-ENG R00
TABLE OF CONTENTS
– CMH Option .......................................................... 11
– Spray Nozzle Humidification (SNH Option) ...................................... 12
Chemical Dryer Dehumidification
– (CD Option) ...................................................................... 13
Carbon Dioxide Additive Control (CO
Option) ........................................................................ 13
Control ...................................................................................... 13
Control ........................................................................................ 14