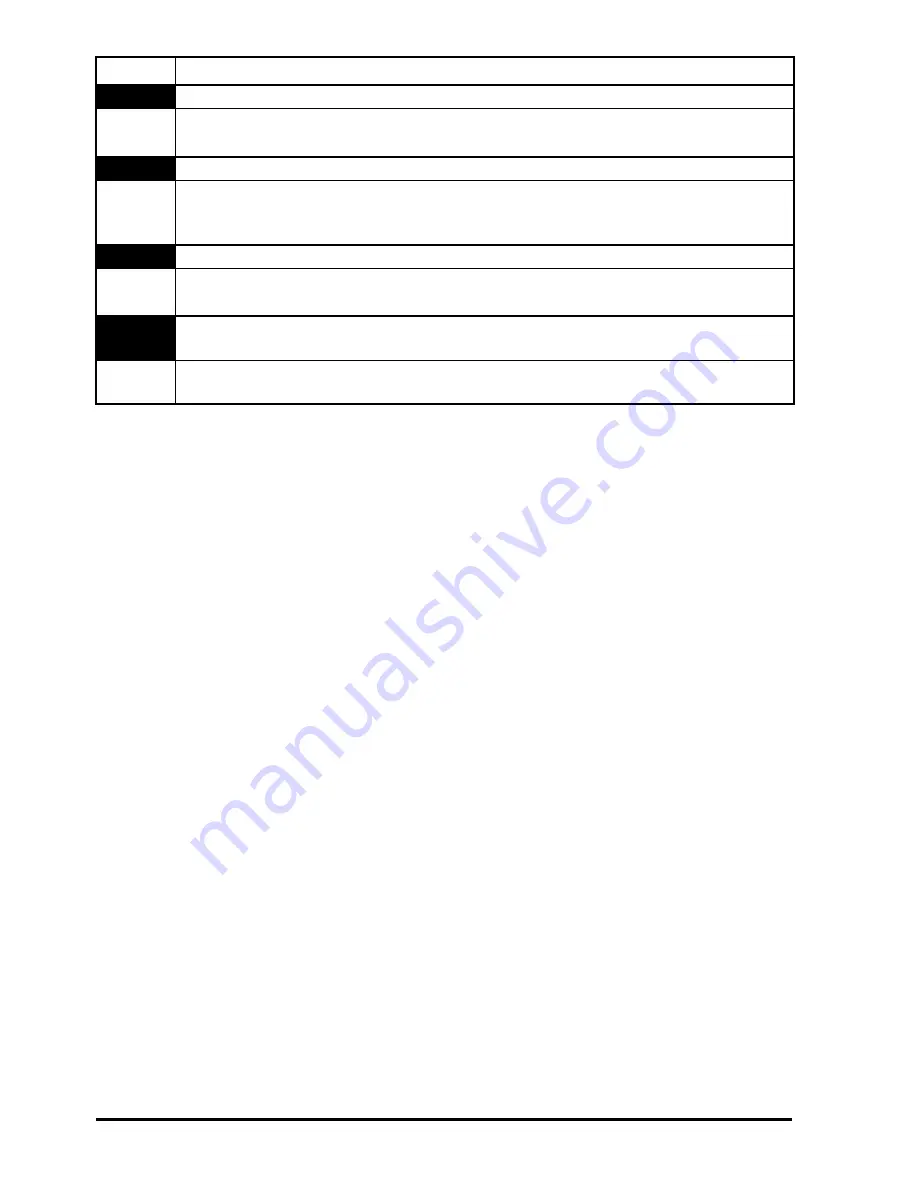
34
SM-Encoder Plus User Guide
www.controltechniques.com
Issue Number: 3
SLX.HF
Solutions Module slot X trip: Solutions Module X hardware fault
200,205,
210
Ensure Solutions Module is fitted correctly
Return Solutions Module to supplier
SLX.nF
Solutions Module slot X trip: Solutions Module has been removed
203,208,
213
Ensure Solutions Module is fitted correctly
Replace Solutions Module
Save parameters and reset drive
SLX.tO
Solutions Module slot X trip: Solutions Module watchdog time-out
203,208,
211
Press reset.
If the trip persists, contact the supplier of the drive.
SL.rtd
Solutions Module trip: Drive mode has changed and Solutions Module
parameter routing is now incorrect
215
Press reset.
If the trip persists, contact the supplier of the drive.
Trip
Diagnosis