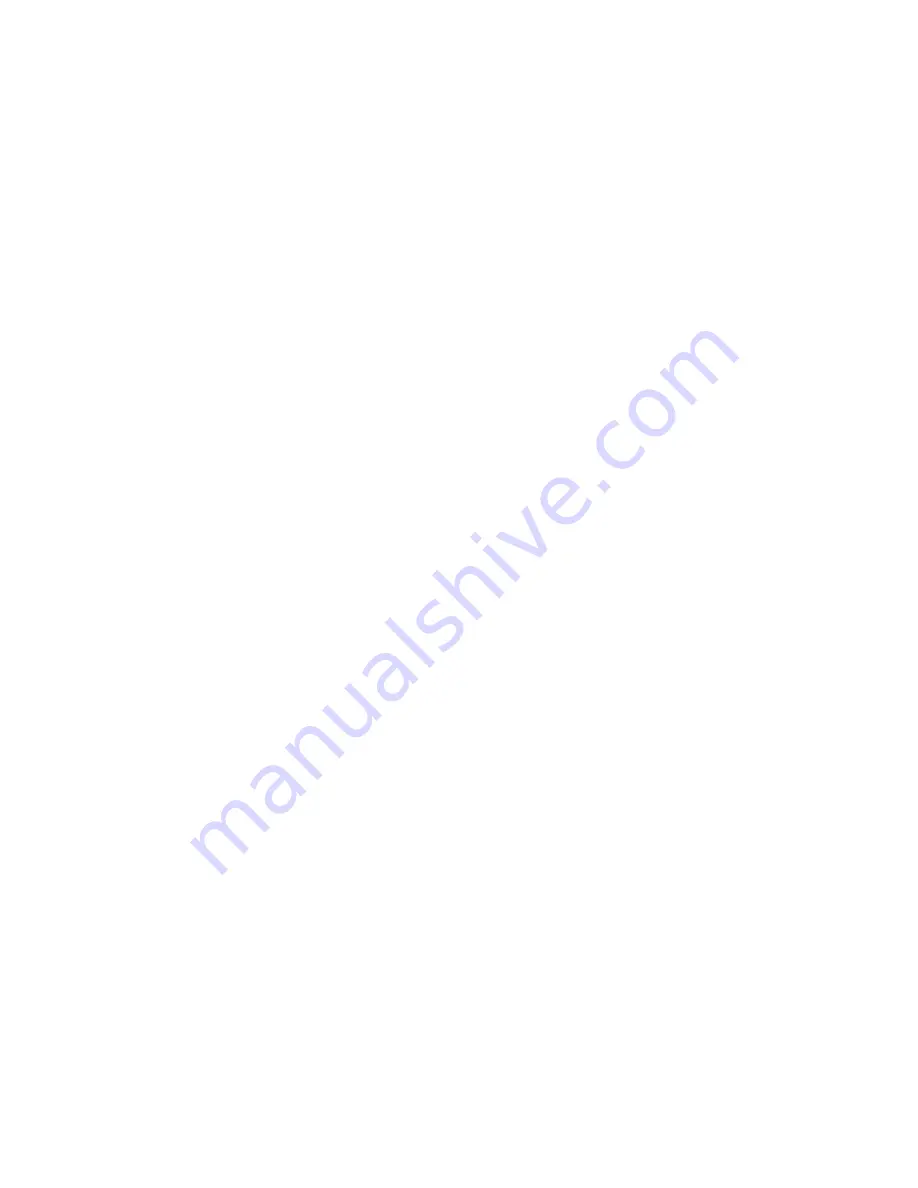
Application manual for YRB-4EML-31S safety relay
Contrinex AG Industrial Electronics
35
DC
Diagnostic coverage
MTTF
Mean time to failure
AOPDDR
Active optoelectronic protective device responsive to diffuse reflection
Device with a sensor function that is generated by optoelectronic transmit and receive
elements, which detects the diffuse reflection of optical radiation generated in the device by
an object located in a protective field specified in two dimensions.
AOPD
Active optoelectronic protective device
Device with a sensor function that is generated by optoelectronic transmit and receive
elements, which detects the interruption of optical radiation generated in the device by an
opaque object located in the specified protective field (or for an optical data link on the axis
of the light beam). In DIN EN 692 (mechanical presses), DIN EN 693 (hydraulic presses),
and EN 12622 (hydraulic trimming presses), the abbreviation AOS is used as a synonym
for AOPD.
SRCF
Safety-related control function - safety function
SRECS
Safety-related electric, electronic, programmable electronic control system