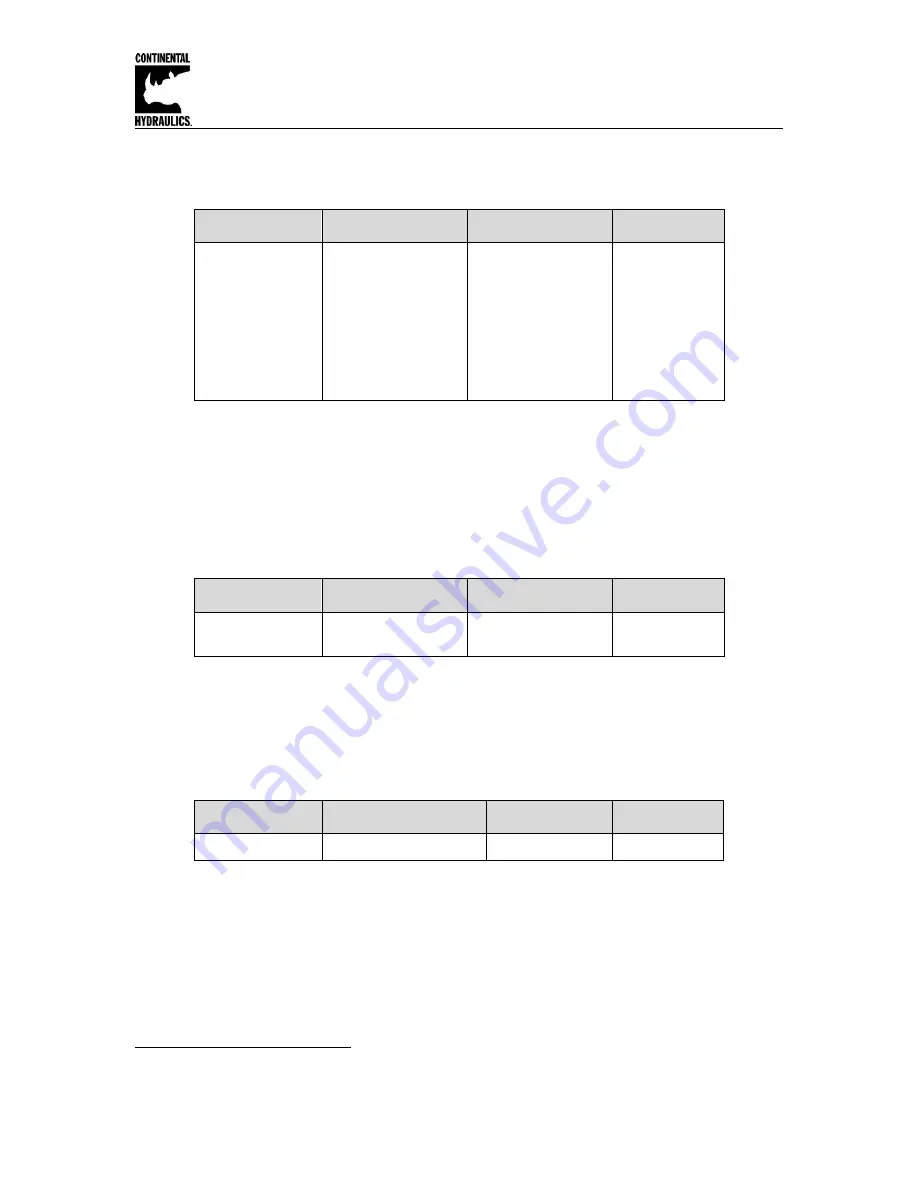
Continental Hydraulics Installation Manual
Page 13 of 27
CEM-SA-B
CHI 1020687 01/2016
SIGNAL (Type of input)
Command
Parameter
Unit
Group
SIGNAL:i x
i=
W|X|V
x=
OFF
U0-10
U10-0
I4-20
I20-4
-
EASY
This command can be used to change the type of input signal (voltages or current) and to define
the direction of the signal. This command is available for all analog inputs (W, X, and V).
OFF= Deactivation of the input
2
.
See
ANIMODE
section (page 24-25) if the Signals used are not listed above, for re-scaling as
required.
N_RANGE: X (Nominal range of the sensor)
Command
Parameter
Unit
Group
N_RANGE:X
x
x= 10… 10000
mm
EASY
N_RANGE (nominal range or nominal stroke) is used to define the length of the sensor. This
value should be always higher than SYS_RANGE. The control parameter cannot be calculated
correctly in case of wrong values.
OFFSET: X (Sensor offset)
Command
Parameter
Unit
Group
OFFSET:X x
x= -
100000… 100000 µm
EASY
Adjustment of the zero point of the sensor.
2
The deactivation can be used to deactivate the velocity (speed) input PIN_9/10 (the VELO value is active).