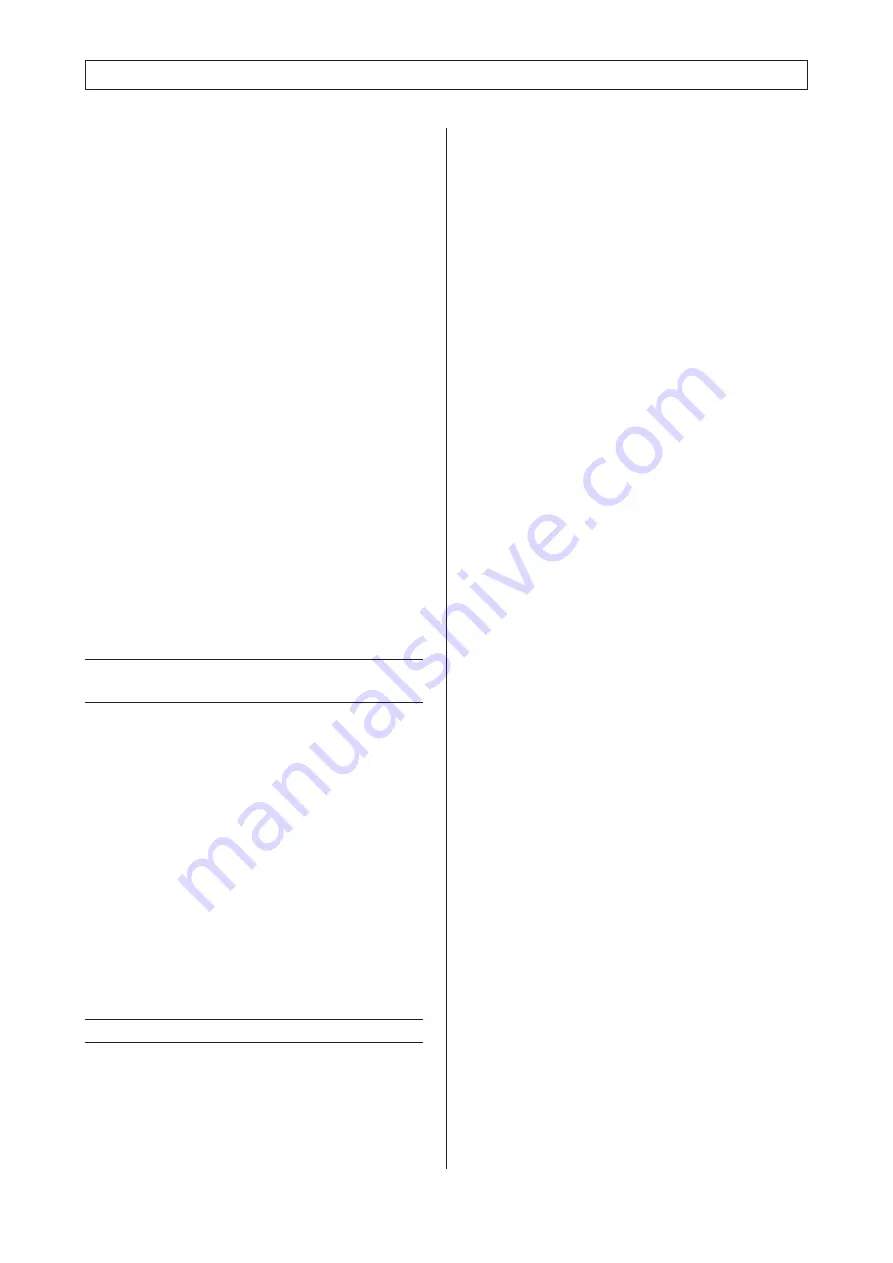
7
Selection and qualification of personnel;
basic responsibilities
Work on/with the machine/unit must be carried out by
reliable personnel only. Statutory minimum age limits
must be observed!
Employ only trained or instructed personnel and
clearly set out the individual responsibilities of the per-
sonnel for operation, set-up, maintenance and repair !
Ensure that only authorized personnel work on or with
the machine !
Define the machine operator's responsibilities giving
the operator the authority to refuse instructions by third
persons that are contrary to safety regulations.
Do not allow persons to be trained or instructed or
persons taking part in a general training course to work
on or with the machine/unit without being permanently
supervised by an experienced person !
Work on the electrical equipment of the machine/unit
must be carried out only by a skilled electrician in ac-
cordance with electrical engineering rules and regula-
tions.
Work on system elements such as hoses may only be
carried out by personnel with special knowledge and
experience of hydraulics !
Installation
In addition to the general technical operation in accor-
dance with the stipulations of the local authorities, we
would like to refer in particular to the following regulati-
ons.
For the lifting of a compressor, a suitable lifting me-
3.3
Changes and modifications to the
machine
Do not make any changes, modifications or attach-
ments to the machine/unit, which could affect safety, wi-
thout the supplier's prior permission !
Unauthorized changes to the machine are not permit-
ted for safety reasons.
Original parts were especially designed for this ma-
chine. We would like to point out that we have not re-
leased and will not release parts and special accesso-
ries which have not been supplied by us. The installati-
on and/or use of such products can therefore affect the
active and/or passive safety.
The manufacturer is not liable for damage resulting
from the use of non-original parts or special accesso-
ries. This applies also to the installation and setting of
safety equipment and valves as well as to welding on
structural or pressurized parts.
3. Safety regulations
3.4
Installation and normal operation
Limit values (pressures, time settings, etc.) have to be
permanently identified !
chanism is to be used, which meets the local safety re-
gulations. All loose or slewable parts must be safely fi-
xed before the machine can be lifted. It is strictly prohi-
bited to stay in the danger zone of a lifted load.
The correct method of lifting (according to the opera-
ting instructions of the load suspension device) has to
be ensured.
All blind flanges, plugs, caps and bags with drying
agent have to be removed prior to the installation of the
pipes. Distributing pipes and pipe connections have to
be of the proper size and suitable for the relevant ope-
rating pressure.
The system has to be installed in such a way that it is
adequately accessible and the required cooling is gua-
ranteed. Never block the air intake. Make sure that the
ingress of humidity via the intake air is kept to a mini-
mum.
The air intake is to be located so that no hazardous
constituent (solvent vapour, etc., but also dusts and
other hazardous material) can be sucked in. This app-
lies also to flying sparks.
The air intake is to be positioned so that no loose clot-
hing of persons can be sucked in.
Make sure that the pressure line from the compressor
to the aftercooler or the air circuit can expand under
heat and does not come into contact with inflammable
material.
The pressure line connected to the air outlet of the sy-
stem must be fitted stress-free.
If a remote control is used, the system must carry a
clearly visible sign with the following note : Attention !
This installation is operated by remote control and can
start up without prior warning !
As an additional safety measure, persons, who start
remotely controlled systems, have to take sufficient
safety precautions in order to ensure that nobody is
checking the system or working on it. For this, a label
with a corresponding warning notice has to be attached
to the remote control equipment.
Compressed air and cooling water lines have to be
clearly marked in line with the local regulations.
If a system comprises several compressors, hand-op-
erated isolator valves have to be installed in order to be
able to shut off each machine individually. When oper-
ating pressure systems, do not rely on the effectiveness
of check valves alone to isolate these systems.
Safety equipment, protective covers or insulation must
not be removed or modified. Any pressure reservoir,
which is located outside the system, the permissible
operating pressure of which is higher than the atmos-
pheric pressure and which is fitted with two or more
pressure supply lines, has to be equipped with addi-
tional safety equipment, which will automatically pre-
vent the admissible operating pressure from rising by
more than 10 %.
The system-specific safety valves used in these com-
pressors only assume the pressure safeguarding func-
tions that are prescribed according to currently valid
standards and regulations.
For the pressure devices/systems installed at the
pressure side connection flange of the compressor, a