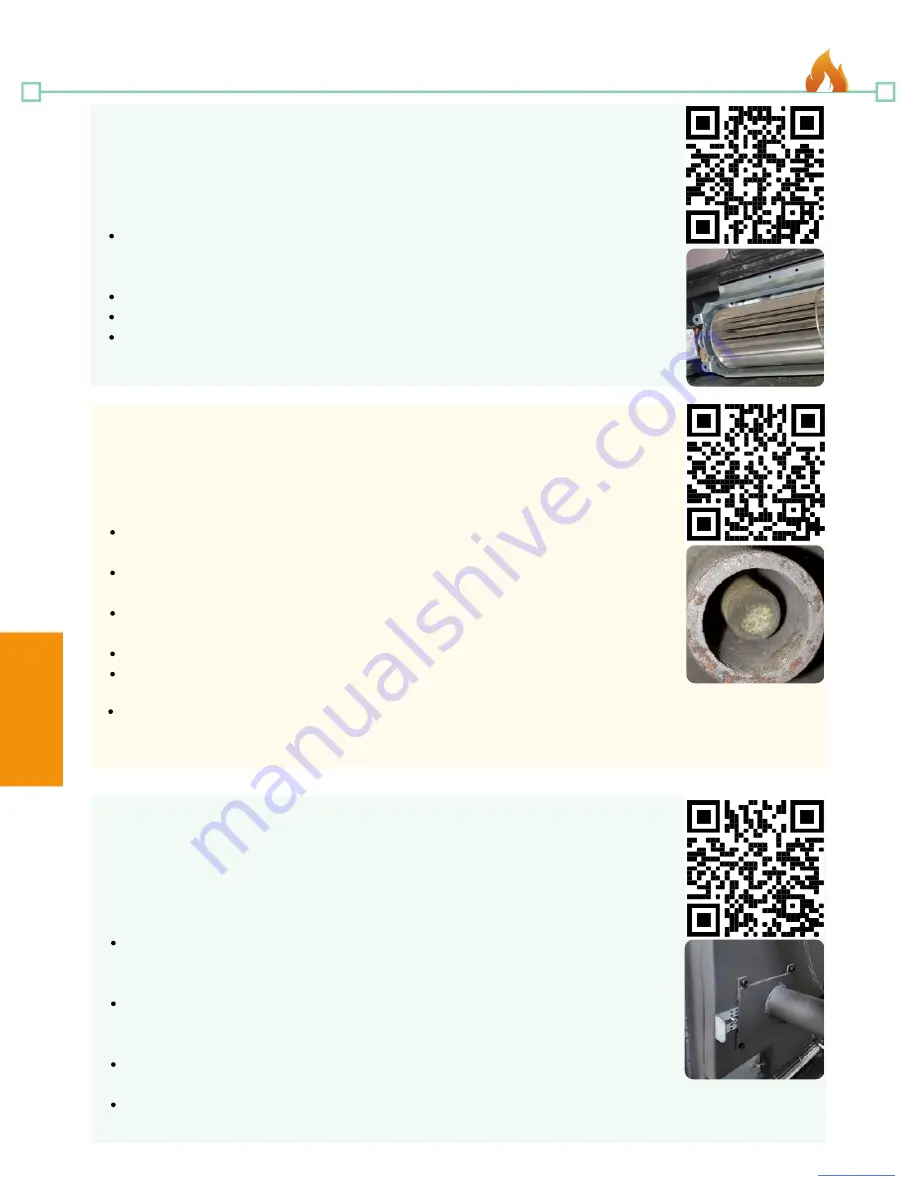
32
Problem: Alarm - High Temperature/Overheat
The stove giving a High Temp or Overheat alarm could be caused by the room blower
not moving enough hot air out of the stove, limited combustion airflow, an improper
fuel-to-air ratio in the settings, or an install with excessive bends/elbows.
Ensure that the room blower fan is working properly, and that the blower voltages
are not set too low.
(If the blower fan is not spinning, try to manually flick it to
check for resistance)
Ensure that the airflow pathways are unobstructed.
(see Maintenance & Cleaning)
Ensure that the exhaust fan is not impeded, and is exhausting correctly.
When operating in Temp mode, ensure that the room temp sensor is not in a cold
location, causing the stove to run on a higher level than needed.
Solutions:
Problem: Alarm - Failure to Ignite
The stove giving a failure to ignite message, means that either a fire failed to ignite, or
that not enough heat was generated at the Proof of Fire sensor to engage the stove's
Heating mode.
Problem: Lazy or Dirty Flame / Buildup of Pellets in the Pot / Dark Black Smoke
or Ash
If you see a buildup of pellets and/or black smoke in the main chamber or at the end
of the exhaust, these are not normal emissions, and usually indicate a reduction of
airflow.
Ensure that the igniter is in a good position, and getting hot at the tip within three
minutes.
(see igniter troubleshooting video)
Ensure that the burn pot is seated and oriented correctly.
(small hole and ring
toward the back of the stove)
Ensure pellets are feeding and being delivered to the burn pot.
(see feeder
troubleshooting video)
Ensure that the front door and ash pan drawer are properly sealed.
Ensure combustion fan is engaging, and the there is sufficient airflow being drawn
through the stove at the air intake pipe.
Solutions:
If the fire is established within 5 minutes and maintains a good flame throughout ignition, but the stove
fails to switch to heating mode, try moving the wires over from the active Proof of Fire sensor to the pre-
installed backup at the exhaust housing.
Troubleshooting
Check for clinkers or blockages in the burn pot, and that the burn pot is seated
flush on the cradle.
(Gaps between the cradle and burn pot can allow air to be
drawn around the pellets instead of through them)
Check for leakages or loose seals/gaskets around the stove, such as around the
glass door or ash pan.
(Ensure the side latches of the ash pan are snug with
about even pressure)
Check for potential blockages in the exhaust chambers or venting.
(see
Maintenance and Cleaning)
Solutions:
Ensure the intake air damper not closed off. (Loosen the 4mm set screw, and pull outward to open)
*
Damper is located at the base of the intake pipe on the inside of the stove, behind the side panel.
Troubleshoot
Summary of Contents for HP22N
Page 2: ......
Page 38: ...Schedules Repairs Date Work Done Date Work Done...
Page 39: ...Schedules Repairs Date Work Done Date Work Done...